Analyzing Maintenance System Software for Better Efficiency
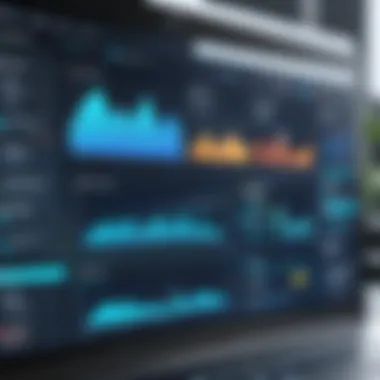
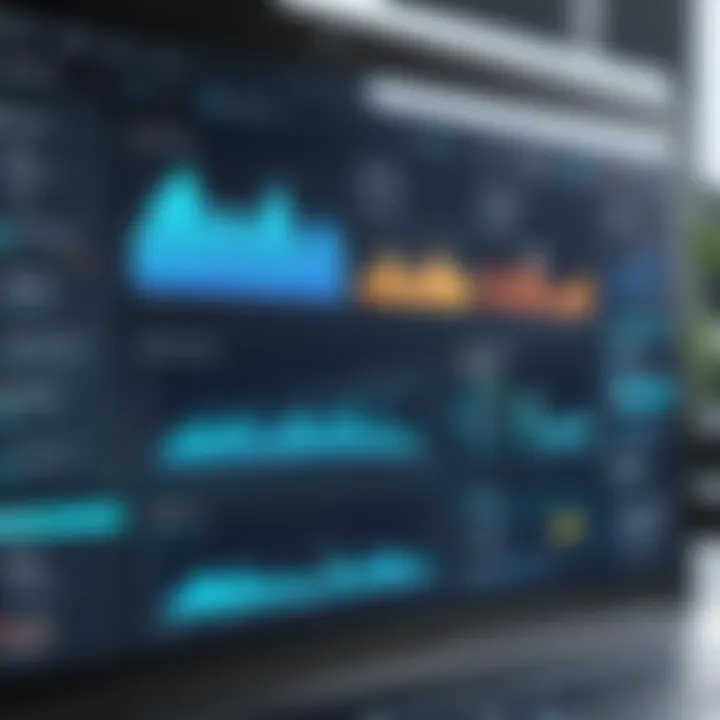
Intro
In today's fast-paced business environment, the capability to effectively manage maintenance operations is more than just a desire; it's a necessity. Organizations across various sectors, from manufacturing to facility management, increasingly depend on maintenance system software to streamline processes, ensure equipment reliability, and bolster overall operational efficiency. This software serves as a pivotal tool for decision-makers, IT professionals, and entrepreneurs, aiding them in navigating the complexities of maintenance management.
As we journey through this exploration, we’ll uncover the essential functionalities, benefits, and some hurdles associated with maintenance system software. Understanding these elements not only illuminates its significance but also guides stakeholders in choosing the right software that aligns with their organizational goals.
Overview of Core Features
Description of Essential Functionalities
At the heart of every maintenance system software lies a set of core features designed to tackle various operational challenges. These functionalities typically include:
- Asset Management: Centralizes information about all assets, helping maintenance teams keep track of equipment's history, warranties, and service schedules.
- Work Order Management: Streamlines the creation, assignment, and monitoring of work orders, allowing for quick responses to maintenance needs.
- Preventive Maintenance: Schedules routine maintenance tasks to prevent equipment failures before they happen, significantly reducing downtime.
- Inventory Management: Monitors stock levels for spare parts, enabling timely ordering and reducing delays in repairs.
- Reporting and Analytics: Generates insightful reports that help identify trends, predict issues, and enhance decision-making.
These functionalities enhance visibility and control over maintenance processes, enabling teams to be proactive rather than reactive.
Comparison of Features Across Top Software Options
When considering various maintenance system software, it's crucial to compare their features. For instance, a few notable options include SAP PM, IBM Maximo, and CMMS by eMaint. Each offers unique characteristics:
- SAP PM offers robust asset management capabilities and integration with other SAP modules, making it ideal for large enterprises.
- IBM Maximo emphasizes scalability and customization, catering well to diverse industries and regulatory requirements.
- eMaint’s CMMS focuses on user-friendly interfaces and plug-and-play features, which suits small to medium-sized businesses eager to adopt maintenance management.
While functionalities vary, the key is to align these features with specific business needs.
"Not all that glitters is gold; a shiny interface does not always equate to robust capabilities. Choosing wisely is paramount."
User Experience and Interface
Insights into UI/UX Design Aspects
User experience (UX) and user interface (UI) design play significant roles in the effectiveness of maintenance system software. A well-designed UI enhances usability, promoting quick adaptation among staff. For instance, clear navigation, intuitive dashboard layouts, and easily accessible menu options all contribute to a seamless user experience.
However, it's also crucial to account for the unique user demographics. Field workers, who might not be tech-savvy, require straightforward interfaces, while IT professionals might appreciate more complex functionalities. Thus, a balanced design catering to varied user needs is essential.
Importance of Usability and Accessibility
Usability, in the context of maintenance system software, cannot be overstated. High usability translates to less time spent on training and troubleshooting, which in turn boosts productivity. Accessibility is equally important—ensuring that software can be accessed on multiple devices, including mobile phones and tablets, allows workers on the ground to perform tasks efficiently.
In closing, a combination of a robust set of features and an exceptional user experience tailors maintenance system software into an indispensable tool for organizations aiming to enhance their operational efficiency.
Understanding Maintenance System Software
Maintenance system software plays a pivotal role in today’s fast-paced landscapes, where uptime and efficiency can mean the difference between success and failure. Organizations across various sectors increasingly rely on these systems to oversee maintenance operations, ensuring that equipment and assets function optimally.
This software centralizes crucial data and processes, allowing for seamless management of maintenance tasks. With the right software in place, decision-makers can reduce downtime, extend the lifespan of their equipment, and allocate resources more effectively. Furthermore, as industries evolve, the importance of integrating technology in maintenance practices becomes even more evident.
Below, we will explore the definition, purpose, and historical context of maintenance system software, delving into its significance for modern organizations.
Definition and Purpose
Maintenance system software is a digital platform that facilitates the management of maintenance tasks and resources. Its main objective is to streamline maintenance operations, increase productivity, and reduce the costs associated with manual record-keeping and repairs. At its core, this software helps organizations in tracking their assets, scheduling routine checks, and managing work orders.
Some key purposes of maintenance software include:
- Monitoring asset performance: By keeping an eye on equipment conditions, organizations can proactively address issues before they escalate.
- Automating work orders: Instead of relying on paper or spreadsheets, teams can manage work orders digitally, reducing the chances of errors.
- Data analytics: The software often includes reporting features that provide insights into maintenance trends and expenditures, allowing for informed decision-making.
In essence, maintenance system software is vital for any organization that aims to maintain operational efficiency and maximize its assets’ lifecycle.
Historical Context
The trajectory of maintenance system software can be traced back several decades. In the past, maintenance management predominantly relied on manual processes, record-keeping on paper, and ad-hoc scheduling of repairs. This method was time-consuming, prone to human error, and often led to increased downtime due to unplanned outages.
As technology advanced, so did the means of managing maintenance. The introduction of computerized maintenance management systems (CMMS) in the late 20th century marked a significant turning point. These systems allowed companies to automate various tasks, such as tracking maintenance schedules and managing inventory, ultimately transforming maintenance practices into a more structured and data-driven approach.
In recent years, the integration of cloud computing, mobile applications, and the rise of the Internet of Things (IoT) have further revolutionized maintenance system software. Today’s solutions enable real-time monitoring, remote access, and automated analytics, making maintenance operations not just reactive but anticipatory. This evolution facilitates better planning and enhanced decision-making capabilities for organizations.
As we continue to delve into maintenance systems, understanding their definition and historical progression is essential in grasping their significant role in modern-day operations. With this knowledge, one can appreciate the strategies that underpin effective maintenance solutions.
Core Features of Maintenance System Software
The selection of maintenance system software isn't just about finding a tool that ticks boxes; it involves understanding the critical features that can profoundly influence operational functionality, efficiency, and ultimately, profitability. Each feature represents a cog in the larger machine of an organization's maintenance strategy. When decision-makers grasp these features, they can better align software selection with organizational goals, paving a path to smoother operations and less downtime.
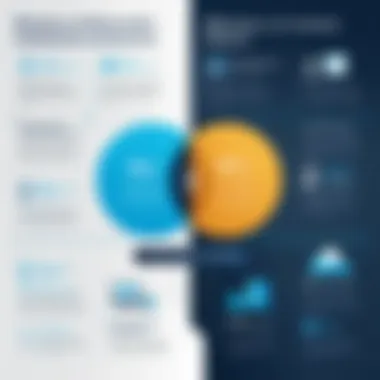
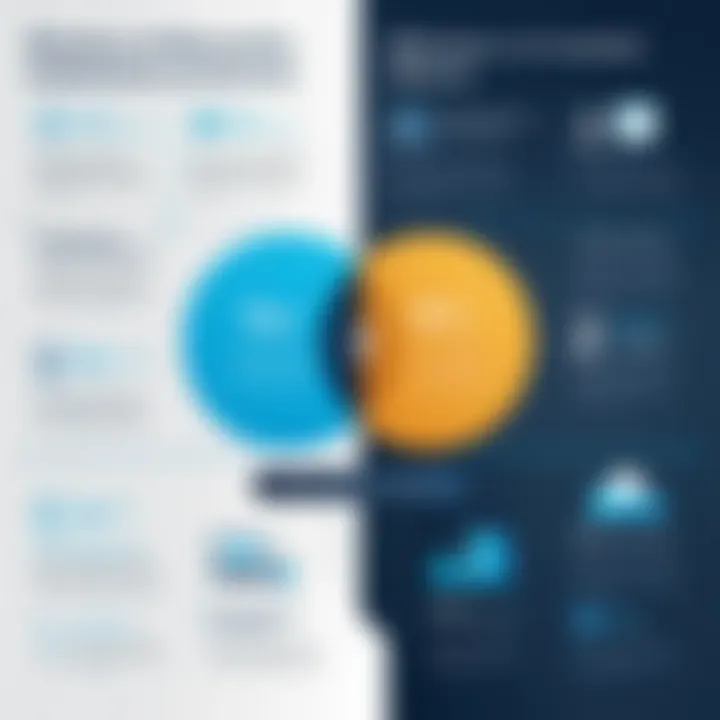
Asset Management
Asset management is the backbone of any maintenance system software. It involves keeping track of all equipment, machinery, and tools that are essential for day-to-day operations. With a robust asset management feature, companies can monitor their assets in real-time, ensuring each piece of equipment is utilized to its fullest potential. This not only aids in maximizing lifespan but also streamlines maintenance schedules.
Imagine a manufacturing plant where each machine's health and usage stats are just a click away. With a few taps, maintenance managers can access the history and performance of their assets. This transparency leads to informed decision-making and allows for timely interventions before minor issues escalate into costly repairs.
"Knowing what you have is half the battle; knowing how to take care of it is the other half."
Work Order Management
Work order management is another crucial component. In any business, tasks arise that need attention, whether that's a broken conveyor belt or scheduled servicing of a fleet of vehicles. Effective work order management allows teams to create, assign, and track these tasks from start to completion. This feature reduces miscommunication between departments and increases accountability.
Through automation, maintenance software can prioritize work orders based on urgency, meaning critical repairs aren't shoved to the bottom of the list. Plus, with digital records, historical data on repairs can inform future decisions, helping avoid repeat issues. A smoother workflow means less lost time and an uptick in productivity.
Scheduling and Planning
Scheduling and planning take the work out of organizing maintenance tasks. Maintenance systems come equipped with tools that let users set up recurring maintenance work, ensuring nothing slips through the cracks. You could think of it like setting your coffee maker for the morning; it’s done for you, allowing you to focus on what matters—brewing the perfect cup.
Scheduling features often include calendars and alerts, making it easy for teams to stay on track with their duties. It effectively paves the way for preventive maintenance rather than waiting for failures to occur. A proactive approach here reduces emergency situations, saving companies from unduly high costs and operational disruptions.
Inventory Tracking
Inventory tracking wraps all these features together by maintaining visibility over spare parts and resources. Gone are the days of scrambling for a replacement part or ordering items after a breakdown has happened. With effective inventory tracking, organizations can keep tabs on their supplies and oversee reorder points.
It's like having a well-organized pantry in your kitchen; you always know what ingredients you have, reducing waste while ensuring you can whip up a meal at a moment’s notice. This aspect also ties directly into budgeting; knowing inventory levels can help in forecasting needs and managing costs effectively.
Types of Maintenance Strategies
Understanding the various maintenance strategies can significantly affect an organization’s operational efficiency. This section explores the key strategies—preventive, predictive, and corrective maintenance—emphasizing how they fit into the broader framework of maintenance system software. These strategies are not just about keeping machines running, but more about enhancing overall productivity and minimizing costs.
Preventive Maintenance
Preventive maintenance is like regular check-ups for your equipment. It involves routine inspections and servicing to prevent unexpected breakdowns. This approach might seem straightforward, but the impact can be profound. Rather than waiting for something to break, organizations schedule maintenance based on time intervals or usage levels. This reduces the likelihood of sudden, costly failures.
For instance, a manufacturing plant might decide to inspect its machinery every six months, changing lubricants or replacing worn-out parts before they lead to bigger issues. The benefits? Reduced downtime, longer equipment lifespan, and a smoother operational flow.
Benefits of Preventive Maintenance:
- Extends equipment life
- Reduces unplanned downtime
- Increases operational efficiency
Implementing this strategy is not without its challenges. Each piece of equipment may require a tailored plan, and keeping track of maintenance schedules can become complex. However, this is where maintenance system software shines, providing tools for scheduling and tracking tasks effectively.
Predictive Maintenance
Predictive maintenance takes it a step further by using data analytics to anticipate when maintenance should be performed. It monitors equipment in real-time, leveraging sensors, IoT technologies, and machine learning algorithms to predict failures before they occur. Think of it as having a crystal ball for machinery health.
For example, in a facility using smart HVAC systems, temperature and humidity readings can signal whether a unit will require repair soon. This makes it possible to mitigate issues before they escalate and helps in planning maintenance work during low-impact times, thereby minimizing interruptions to work.
Key Advantages of Predictive Maintenance:
- Optimized maintenance schedules
- Reduces costs related to downtime
- Enhances safety by identifying hazards early
However, predictive maintenance is not just about technology; it requires a cultural shift within the organization towards data-driven practices. This might necessitate training employees to be comfortable with the tools available.
Corrective Maintenance
Corrective maintenance is what typically comes to mind when thinking about repairs. It involves reacting to equipment failures and making necessary repairs after an issue has surfaced. While it seems spontaneous, it's a valid strategy that many industries employ, especially when costs or operational pressure limits the adoption of more proactive approaches.
Consider a situation where a production line experiences a sudden halt due to machinery failure. Corrective maintenance becomes crucial, as the focus shifts to getting the operation back up and running quickly.
Circumstances Favoring Corrective Maintenance:
- Budget constraints
- Non-essential equipment
- When equipment reliability is low
While this strategy may keep operations going in the short term, it often leads to spiraling costs over time because of the reactive nature of repairs. Relying solely on corrective maintenance can also compromise product quality and employee safety. Thus, it's usually recommended to balance corrective measures with preventive or predictive methods when possible.
"A stitch in time saves nine." This old adage rings true in maintenance as proactive approaches tend to save money and headaches in the future.
Advantages of Implementing Maintenance Software
When it comes to ensuring operational success, maintenance software plays a pivotal role. This section delves into the benefits of such systems, showcasing how they not only streamline operations but also contribute to the bottom line. For decision-makers, understanding these advantages can be the key to making informed choices that elevate performance and drive value across their organizations.
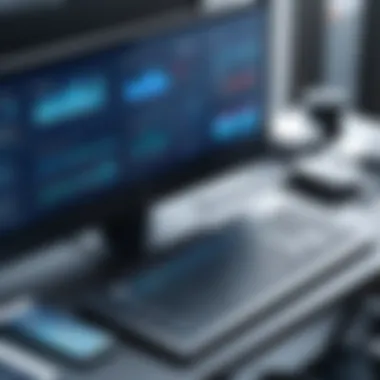
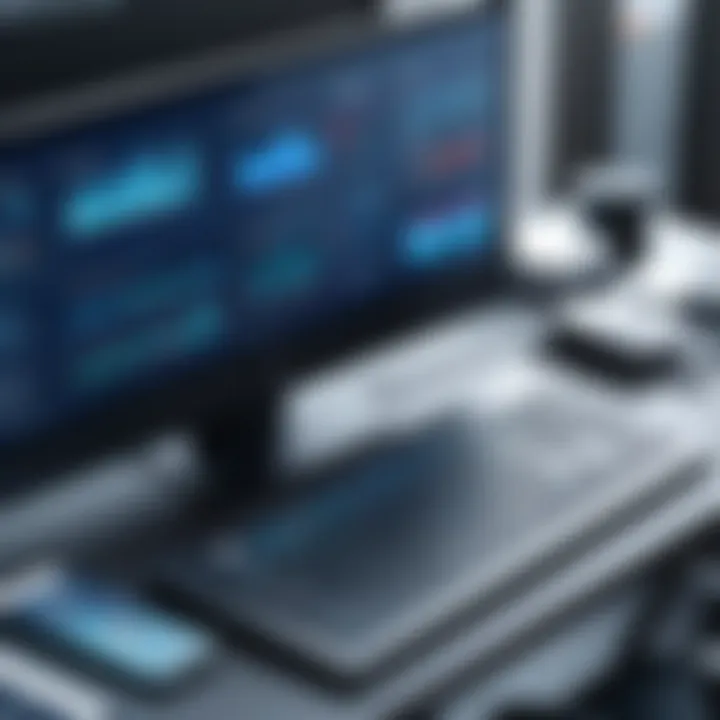
Increased Efficiency
One of the most evident gains from adopting maintenance software is the boost in efficiency. Traditionally, maintenance tasks often rely on manual processes that can be slow and prone to error. By automating these tasks, companies can minimize downtime and streamline workflows.
For instance, consider a manufacturing plant that implements a computerized maintenance management system (CMMS). This system not only schedules regular maintenance tasks but also tracks their completion in real-time. Technicians can access equipment history and maintenance records with just a few clicks, reducing the time taken to locate information significantly. The result? Tasks get done quicker, machines run smoother, and employee productivity sees an uptick.
Moreover, workflow automation eliminates the bottleneck caused by paper-based systems. When a work order comes in, alerts can be sent out immediately, ensuring that necessary actions are taken without delay. Ultimately, increased efficiency translates to faster response times and enhanced overall performance.
Cost Reduction
Cost concerns often hover over any investment decision. Utilizing maintenance software could actually provide a cushion for these worries. First and foremost, by maintaining equipment more effectively, organizations can extend the lifespan of their assets. Regular maintenance reduces the risk of catastrophic failures that often come with a hefty repair bill.
Additionally, with improved scheduling and inventory management, organizations avoid unnecessary purchases. Maintenance software helps track spare parts and equipment needs precisely, which means that businesses can stock only what they need when they need it, rather than over-ordering. This just-in-time inventory approach can lead to significant cost savings.
In a study conducted by the National Center for Biotechnology Information, companies using CMMS reported reductions in total maintenance costs by as much as 20-25%. It's not just about initial investment, but how to make that investment return a yield over time.
Enhanced Compliance
In today's world, compliance with industry regulations and standards isn’t just a box to check; it ’s a necessity that can impact a company’s reputation and operational viability. Maintenance software ensures that safety checks, inspections, and maintenance schedules are not just adhered to but meticulously recorded. This foster better accountability and transparency, proving indispensable in sectors like healthcare and manufacturing where compliance is paramount.
Imagine a facility that utilizes maintenance software to log every service performed on its medical equipment. In case of an audit, this facility can present a comprehensive record of compliance efforts. More importantly, this capability not only saves time but also reduces the risk of costly fines associated with non-compliance.
Furthermore, by automating reminders for maintenance tasks, businesses ensure that deadlines are met, and nothing falls through the cracks. Enhanced compliance, thus, can serve as both a shield against risks and a potential differentiator in a competitive market.
"Adopting maintenance software can lead to increased efficiency, reduced costs and enhanced compliance, fundamentally transforming how an organization operates."
These advantages underline the significance of integrating maintenance software into operations; they provide a robust framework for efficiency, cost management, and adherence to compliance standards.
Challenges in Maintenance System Software Adoption
Adopting maintenance system software can be like navigating a minefield. While the benefits can be extensive, the hurdles are just as significant. Organizations looking to implement these systems must confront various obstacles that can hinder effective usage. Recognition of these challenges is crucial not only to avoid potential pitfalls but also to ensure that the integration process is as smooth as possible. This section will explore user resistance, integration issues, and cost concerns, which are often intertwined but require distinct considerations.
User Resistance
One of the biggest roadblocks in adopting new maintenance software is user resistance. Employees might be set in their ways, clinging to traditional methods that they are comfortable with. Change can send shivers down anyone’s spine, particularly if the existing systems seem to function adequately. Resistance often stems from a fear of the unknown. Staff might worry about their job security, worrying automation could make them redundant. Moreover, people may doubt the claimed efficiencies of the new software, viewing it as yet another passing fad.
To counteract user resistance, organizations should focus on engagement and education. Providing thorough training sessions can give the team confidence in their ability to operate the new system efficiently. Open communication about the benefits—be it reduced workloads or streamlined processes—can significantly ease fears. Providing a platform for feedback during the implementation phase might transform early skeptics into enthusiastic advocates. Consider using incentives for adopting the new system successfully to further motivate employees and mitigate resistance.
Integration Issues
Another significant challenge is integration. Maintenance systems often require compatible hardware and software to operate effectively, and many organizations face difficulties in integrating these solutions with their existing infrastructure. Problems may arise when trying to synchronize the new software with legacy systems that have been in place for years. This lack of compatibility can not only lead to a bumpy rollout but also add unexpected complexities during daily operations.
Understanding that successful adoption hinges on seamless integration will save time and headaches later on. Before rolling out the new system, it’s paramount to conduct a comprehensive audit of existing processes and technologies. Alignement of platforms, ensuring that data flows smoothly between systems, should take precedence. Collaboration with IT professionals during this phase can't be stressed enough, as they can assist in selecting a software solution that matches the existing ecosystem, minimizing disruptions. Additionally, having contingency plans is wise, in case integration encounters unexpected obstacles.
Cost Concerns
Lastly, there’s the elephant in the room—cost concerns. Budget constraints can haunt even the most well thought-out projects. The initial expense might be prohibitive, especially for smaller organizations. Licensing fees, training costs, and the potential need for additional hardware can inflate the overall investment, making stakeholders wary. It’s essential for decision-makers to recognize that, while the upfront costs may seem daunting, the long-term savings can be significant.
To alleviate cost concerns, conducting a thorough cost-benefit analysis is essential. Breaking down potential savings from improved efficiency and reduced downtime can paint a more compelling picture. Moreover, considering phased implementation can help distribute costs over time, making it easier to manage the financial burden.
"An investment in knowledge pays the best interest." - Benjamin Franklin
Understanding these challenges can prepare organizations to face and overcome them effectively, ensuring a more successful adoption of maintenance system software.
Evaluating Maintenance Software Solutions
When it comes to selecting maintenance software, the devil is in the details. Dedicating time to evaluate these solutions can pay off big in terms of efficiency, productivity, and ultimately the bottom line. In a landscape where every minute counts, assessing various software options becomes crucial for decision-makers, IT professionals, and entrepreneurs alike. It’s not just about finding any software; it’s about pinpointing the right fit for specific business needs and workflows.
Key Selection Criteria
Selecting a maintenance software solution can feel like looking for a needle in a haystack. However, focusing on key selection criteria can simplify the process considerably.
- Functionality: Does the software offer the essential features your business requires? Consider functionalities such as work order management, asset tracking, and reporting capabilities.
- Scalability: As your business grows, can the software adapt? You want a solution that can evolve with your needs.
- User Experience: If the software is as easy as pie, your team is more likely to adopt it. A user-friendly interface can spur engagement.
- Integration with Existing Systems: How well will this software mesh with the tools you're already using? Seamless integration is paramount to avoid disruption in operations.
- Cost Efficiency: What’s the total cost of ownership? Look beyond initial expenses to consider maintenance fees, upgrade costs, and potential training needs.
Considering these factors can guide organizations towards making informed decisions.
Vendor Reputation
Evaluating the vendor reputation of the software provider can reveal a lot about what to expect. A solid reputation often points to reliability and quality. To gauge this:
- Research the Vendor: Look for information about the vendor's history in the market. Longevity often indicates stability.
- Industry Recognition: Awards, certifications, and industry partnerships can serve as a stamp of approval.
- Client Portfolio: Review the types of clients the vendor engages with. Partnering with reputable names can be a reassuring sign of capability.
- Customer Service: An attentive support team can make a world of difference. Investigate their customer support options and responsiveness.
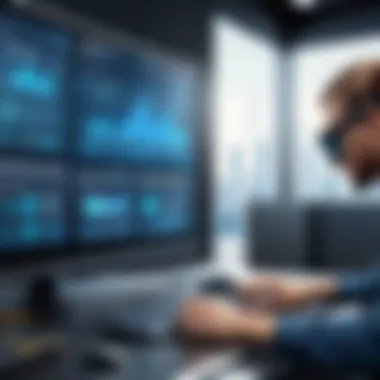
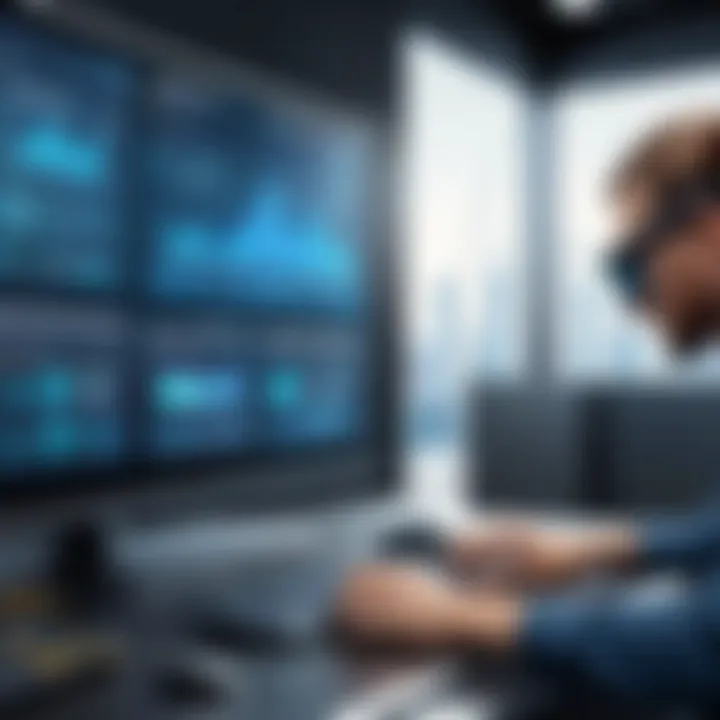
By keeping a keen eye on vendor reputation, organizations can sidestep potential pitfalls.
User Reviews and Feedback
Looking at user reviews and feedback provides an unfiltered glimpse into how the software performs in real-world scenarios. This step shouldn't be overlooked.
- Review Sites: Websites like Reddit or specialized software review platforms can provide diverse perspectives from actual users.
- Social Media: Sometimes, online discussions reveal honest opinions and experiences. Scrolling through forums or Facebook groups related to maintenance software can give insight.
- Case Studies: Many vendors publish success stories, but it's wise to reference independent reviews for a balanced viewpoint.
Listening to the voice of the user is invaluable; it can illuminate both strengths and weaknesses that may not be apparent in polished marketing materials.
By investing the time to evaluate the right maintenance software, you are positioning your organization not just to adapt, but to thrive in a competitive environment.
Integration with Other Systems
To keep pace with the rapid changes in technology, maintenance system software must integrate seamlessly with other systems. The efficiency and effectiveness of maintenance strategies often hinge on how well these systems communicate. When maintenance software can interface with systems like Enterprise Resource Planning (ERP) and the Internet of Things (IoT), it creates a holistic environment for operational excellence. Here’s why this integration is crucial:
- Enhanced Data Flow: Systems that work together lead to smoother data handling. This means real-time access to updated information, which can greatly improve decision-making processes.
- Streamlined Processes: By integrating disparate systems, organizations reduce the need for manual data entry and the risks of errors that come with it. Streamlining workflows improves productivity across the board.
- Unified Reporting: When maintenance software works alongside other business systems, it simplifies reporting. Combining data from multiple sources enables comprehensive analyses that provide insights into operational performance.
Integration shouldn't be viewed merely as a technical requirement. It is a strategic advantage that can provide companies a competitive edge, allowing them to respond quickly to changing conditions in their operational landscape.
ERP Systems
Enterprise Resource Planning (ERP) systems play a pivotal role in managing a company's core business processes. Integrating maintenance software with ERP systems can leverage existing financial, operational, and human resource data. This creates a wealth of benefits:
- Real-Time Inventory Management: When maintenance software taps into ERP functionalities, it can access up-to-the-minute inventory levels. This is vital for ensuring parts are available when needed, so downtime is minimized.
- Cost Tracking: With ERP integration, maintenance teams can combine cost data with operational metrics. This helps in identifying where resources are well allocated or where wastage may be occurring.
- Holistic Decision Making: Decision-makers get a holistic view of operations. For instance, if a piece of equipment frequently breaks down, is there a trend in its failure? Integrating this data helps tackle the root causes.
"The synergy achieved through integrating ERP and maintenance systems yields a more agile, responsive, and informed operational framework."
IoT and Smart Devices
In an era where devices are becoming increasingly smart, IoT integration is critical for modern maintenance systems. Sensors and smart devices can feed valuable data into maintenance software, thus enhancing functionality:
- Predictive Maintenance: Smart devices equipped with sensors help organizations shift from reactive maintenance to predictive maintenance. These devices can forecast potential failures before they happen, allowing teams to address issues proactively.
- Data Analytics: With IoT, maintenance systems can gather vast amounts of data which can be processed for deeper analytics. This can uncover valuable insights about equipment performance, usage patterns, and even user behavior.
- Remote Monitoring: IoT enables the possibility of monitoring equipment and assets remotely. This can cut down on inspection time and allows for immediate responses to potential problems when they arise.
Integrating maintenance systems with IoT and smart devices isn’t just a trend, but rather, it is fast becoming a necessity for businesses striving for operational excellence.
Future Trends in Maintenance System Software
As we scroll through the evolution of maintenance system software, it becomes clear that understanding future trends is essential for staying relevant in this ever-changing landscape. These trends not only promise to enhance operational efficiencies but can also redefine the way businesses approach maintenance processes. For decision-makers and IT professionals, recognizing these developments makes a tangible difference in optimizing performance and ensuring a competitive edge. Adopting innovative tools and technologies can be a game-changer, providing not just better outcomes but also transforming organizational cultures.
Artificial Intelligence and Machine Learning
Incorporating Artificial Intelligence (AI) and Machine Learning (ML) into maintenance systems is no longer a distant fancy; it’s a current reality. These technologies analyze vast amounts of data swiftly, identifying patterns and predicting machinery failures before they occur. This proactive stance helps organizations transition from reactive to predictive maintenance strategies. Imagine a scenario where maintenance managers receive alerts before equipment issues arise—a shift that translates to significant time and cost savings.
- AI algorithms enhance diagnostic accuracy, offering deeper insights into operational inefficiencies.
- Machine Learning models can optimize scheduling and resource allocation, leading to superior workflow management.
Furthermore, the integration of these technologies facilitates data-driven decisions. With machine learning continuously improving from new data inputs, the system learns to adapt and scale according to changing operational demands. This adaptability fosters an environment for ongoing optimization and refinement.
Mobile Technologies
In today’s fast-paced world, mobile technologies have become indispensable tools for maintaining seamless operations. The accessibility of maintenance systems through mobile applications allows technicians and managers to monitor and manage assets directly from their smartphones or tablets. This shift increases responsiveness and ensures that crucial information is always at hand.
- Real-time Data Access: Mobile interfaces allow users to gather and analyze data in real time, ensuring swift decisions based on the most recent information.
- Remote Problem-Solving: With mobile technologies, support can often be provided remotely, reducing the need for on-site visits and expediting problem resolution.
The need for agility in operations is paramount, and mobile technologies deliver just that. Mobile platforms can also integrate easily with existing systems, further providing essential links between technicians in the field and centralized operations. This can significantly enhance communication and collaboration, ensuring that everyone is on the same page.
"The future of maintenance system software lies in leveraging advanced technologies to foster proactive maintenance solutions that drive efficiency and minimize downtime."
End
In a world of increasing complexity and rapid technological advancement, the consideration of maintenance system software transcends mere operational efficiency. The conclusions drawn in this article highlight the crucial role of such systems in ensuring that organizations can not only keep their processes smoothly running but also adapt to the evolving demands of the marketplace. It’s about achieving a delicate balance between maintaining existing infrastructures and unveiling new opportunities for growth by leveraging data-driven insights.
Summary of Insights
The essence of maintenance software lies in its vast benefits. From enhancing efficiency in day-to-day operations to ensuring compliance with industry standards, these systems empower organizations to take control of their assets and resources. The journey through this article has underscored several pivotal points:
- Customization and Flexibility: Various types of maintenance strategies cater to different needs, be it preventive, predictive, or corrective.
- Critical Features: Robust functionalities like work order management, asset tracking, and integration capabilities set a solid foundation for operational excellence.
- Challenges and Considerations: A keen focus on user resistance and integration hurdles shapes the adoption curve of maintenance systems, demanding strategic planning.
- Future Directions: Adaptation to trends like AI and mobile technology is not merely futuristic thinking but a necessity for staying relevant.
In weaving together these insights, one recognizes that maintenance system software does more than streamline processes; it serves as a vital partner that fosters organizational resilience and agility in times of change.
Call to Action for Decision-Makers
For decision-makers, the time to act is now. The proliferation of maintenance systems presents an opportunity that should not be overlooked. As you steer your organization toward selecting the right software, consider the following:
- Assess your current needs. Are your existing processes adequate or are there gaps that need addressing?
- Engage with stakeholders. The input from various teams will provide critical insights into how different functionalities can serve their unique requirements.
- Research different vendor options. Not all solutions are created equal. Look for reputable vendors whose offerings align with your operational goals and engage with their community to hear user experiences.
- Pilot Test. Don’t hesitate to test software solutions on a smaller scale before a full-fledged rollout. This will help you uncover any unforeseen challenges.
By being proactive and informed, decision-makers can harness the full potential of maintenance system software—turning what has traditionally been merely reactive maintenance into a strategic advantage for the organization.