In-Depth Analysis of PLM Systems for Professionals
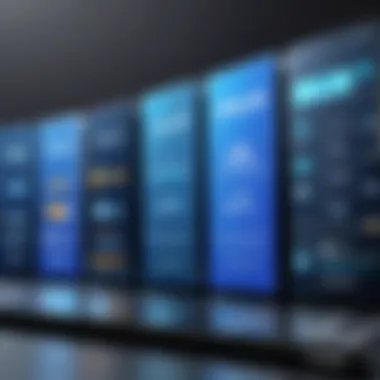
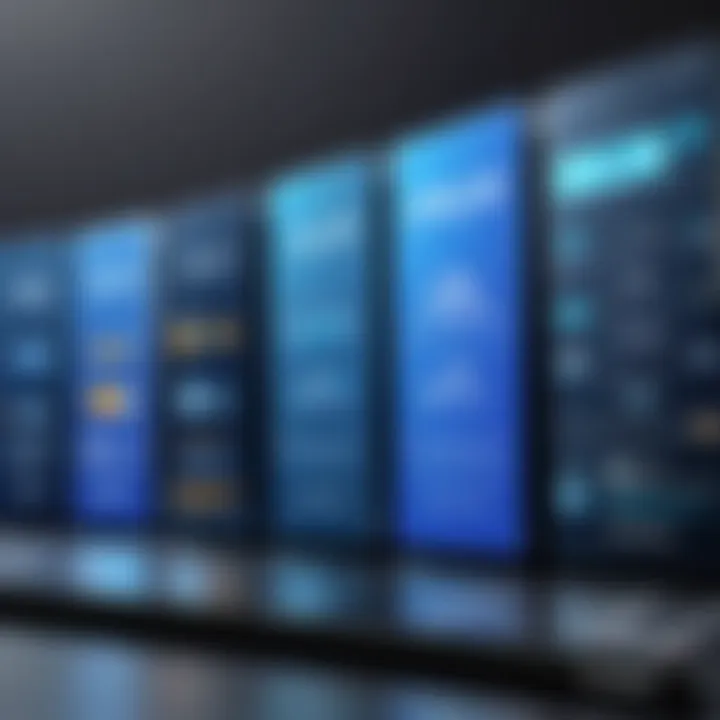
Intro
Product Lifecycle Management (PLM) systems serve as a crucial backbone for organizations aiming to optimize their product development processes. The evolution of these systems has been significant, driven by the need for improved efficiency in managing product data across various stages, from conception to retirement. PLM systems empower companies to enhance collaboration, streamline operations, and ultimately drive innovation. Given the multitude of options available in the market, distinction among these systems becomes vital. This article dissects the core functionalities and characteristics that define contemporary PLM solutions, guiding decision-makers through the complex landscape of options.
Overview of Core Features
To effectively compare PLM systems, one must first understand the core features that these tools offer. Essential functionalities typically include:
- Data Management: The central repository for all product-related information—design files, specifications, and compliance documents.
- Collaboration Tools: Functions that facilitate communication among teams, often integrating with existing communication platforms.
- Change Management: Processes designed to manage modifications to product specifications or designs seamlessly.
- Project Management: Tools to help with scheduling, resource allocation, and tracking progress across different teams.
- Analytics and Reporting: Dashboards and reports that provide insights into key performance indicators and help in decision-making.
Comparison of Features Across Top Software Options
When assessing different PLM systems, it's helpful to compare their features side by side. Some notable systems include:
- Siemens Teamcenter: Known for robust data management capabilities combined with comprehensive analytics tools. Users appreciate the strong integration with CAD systems.
- PTC Windchill: Excels in collaboration tools, especially for geographically dispersed teams. Its built-in change management features stand out.
- Autodesk Fusion Lifecycle: Offers a cloud-based approach, making it more accessible for smaller companies looking for a cost-effective PLM.
- Enovia (Dassault Systèmes): Provides extensive customization options, suitable for organizations with specific needs.
These varying strengths compel organizations to reflect on their particular requirements and existing infrastructure before choosing a PLM system.
User Experience and Interface
A PLM system’s design plays a crucial role in its adoption across an organization. The user interface (UI) and user experience (UX) can dramatically influence productivity and user satisfaction.
Insights into UI/UX Design Aspects
Effective UI/UX design aims for simplicity and ease of navigation. A well-structured layout minimizes training time for new users and enhances overall engagement.
Importance of Usability and Accessibility
Prioritizing usability ensures that all employees, regardless of technical expertise, can efficiently interact with the system. Accessibility features cater to diverse workforce needs, including those with disabilities, thus fostering an inclusive work environment.
A user-friendly design can significantly reduce the learning curve and increase user adoption rates across varied teams.
By taking these elements into account, organizations can make informed choices about which PLM solution aligns best with their operational goals and workforce capabilities.
Prelude to PLM Systems
Product Lifecycle Management (PLM) systems are critical in today’s fast-paced business landscape. They serve as a bridge that connects various departments, products, and processes over the lifespan of a product, from inception to retirement. Implementing a PLM system can lead to improved productivity, reduced time-to-market, and better quality control.
Understanding PLM is essential for decision-makers, IT professionals, and entrepreneurs. These stakeholders need to grasp how PLM systems can optimize processes and ensure collaboration across teams. Additionally, with the continuous evolution of products and markets, a well-designed PLM system provides the framework necessary to adapt swiftly to changes.
Definition of PLM
PLM refers to the process of managing the entire lifecycle of a product from its initial concept and design, through manufacturing and service, to its ultimate disposal. It encompasses various aspects such as data management, workflows, collaboration among teams, and compliance with regulations.
PLM solutions provide a way to consolidate and organize data related to products, making it easier for teams to access and utilize the information effectively. Key components of PLM systems include:
- Data Management: Organizing all product-related data in a central location.
- Collaboration Tools: Enabling teams to work together more efficiently, regardless of location.
- Integration Capabilities: Allowing PLM systems to work seamlessly with other enterprise systems like ERP and CRM.
Importance of PLM in Modern Businesses
In the current corporate climate, organizations face the pressure of meeting high consumer expectations while adhering to compliance standards. A robust PLM system is not just a tool but an essential strategic asset. It aids in:
- Enhancing Collaboration: Different teams can communicate and share data effectively, which promotes innovation and reduces errors.
- Accelerating Time to Market: With streamlined processes, companies can introduce products faster than competitors.
- Ensuring Compliance: A PLM system helps ensure that products meet regulatory requirements throughout their lifecycle.
The advent of digital technologies has amplified the need for effective PLM systems. Companies increasingly recognize that without a solid PLM strategy, they risk falling behind. An integrated approach to managing products can lead to significant operational efficiencies and a competitive advantage.
Key Features of PLM Solutions
The selection of a Product Lifecycle Management (PLM) solution is critical for modern businesses aiming for efficiency and innovation. Understanding key features of PLM systems is crucial for decision-makers to identify which tools can best serve their organization's needs. Key features encompass a range of functionalities that directly influence data management, collaboration, integration, and analytics capabilities. Businesses must scrutinize these elements since they determine how well a PLM system can streamline processes and enhance competitiveness in a saturated market.
Data Management Capabilities
Data management is a cornerstone of any PLM solution. It involves the orderly collection, storage, and dissemination of product data throughout its lifecycle. Effective PLM solutions must be able to handle vast amounts of data from various sources, ensuring consistency and accuracy.
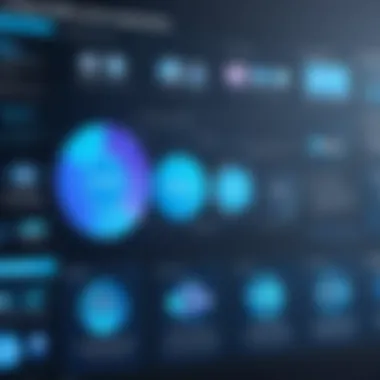
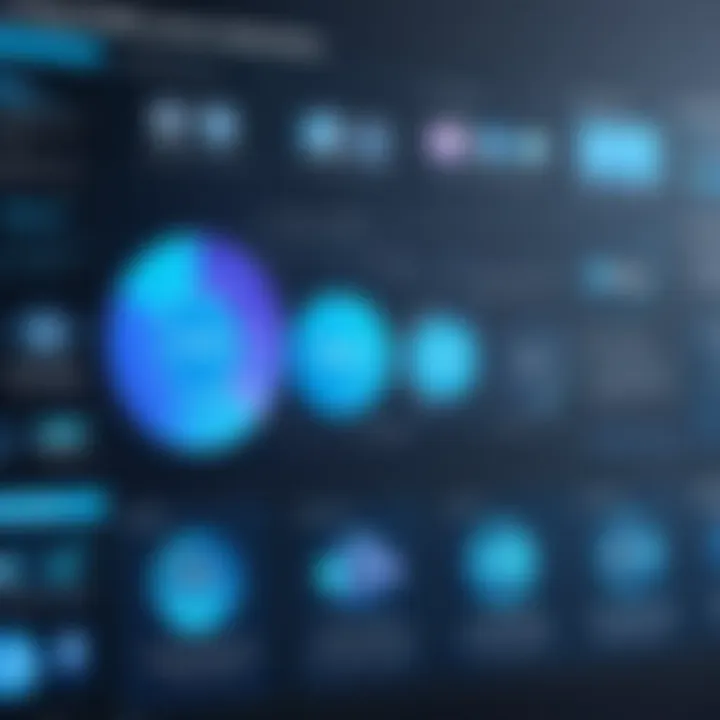
The most effective systems offer process-driven approaches to manage critical data, including product specifications, documentation, and design records. This ensures that all stakeholders, from engineers to marketing teams, have access to the most current information, minimizing errors from outdated data.
Moreover, robust data management tools allow for comprehensive tracking of product changes, ensuring all alterations are documented. This capability supports compliance and facilitates easier audits, two essential aspects for industries like pharmaceuticals and aerospace.
Collaboration Tools
Collaboration is vital in any PLM process. Solutions need to offer tools that enable seamless communication among employees, suppliers, and customers. Effective collaboration tools within PLM systems enable real-time discussions, file sharing, and project management.
Features like integrated chat systems, comment functionalities, and task management capabilities help teams stay aligned and informed. By fostering a collaborative environment, PLM systems can reduce time-to-market and enhance product quality.
Furthermore, some PLM solutions offer social collaboration features, allowing teams to use familiar social media-style interfaces to discuss projects. This user-friendly approach can enhance participation across various departments.
Integration with Other Systems
Integration is critical for a successful PLM deployment. PLM systems should work seamlessly with existing enterprise resource planning (ERP), customer relationship management (CRM), and manufacturing execution systems (MES).
This interoperability is essential for maintaining data consistency across platforms. For instance, integrating a PLM solution with an ERP system can ensure that design changes immediately reflect in inventory and production schedules, contributing to operational efficiency.
Many modern PLM solutions provide APIs that facilitate these integrations, allowing businesses to customize processes and connect software tools that best suit their workflow.
Analytics and Reporting Functions
Analytics capabilities within PLM solutions provide crucial insights into product performance throughout its lifecycle. Comprehensive reporting functions allow organizations to assess everything from supplier performance to manufacturing efficiency.
These tools can help identify trends and potential bottlenecks, enabling proactive decision-making. By utilizing data analytics, companies can enhance product quality while optimizing development costs.
Furthermore, strong reporting features can help stakeholders present findings and results to upper management, ensuring everyone is informed of performance metrics and key performance indicators (KPIs).
"The success of a PLM system lies not just in its features but in how well it integrates into existing workflows and enhances overall productivity."
In essence, comprehending key features of PLM solutions provides valuable insights for decision-makers. Engaging with the right mix of data management, collaboration tools, seamless integration, and analytics can lead to profound improvements in product development and lifecycle management.
Popular PLM Solutions in the Market
Understanding the landscape of Product Lifecycle Management (PLM) systems is crucial for organizations seeking to improve their management processes. The marketplace is populated with various solutions, each tailored to meet specific needs and requirements. The selection of a suitable PLM system can significantly impact productivity, collaboration, and overall product success. Thus, examining popular PLM solutions is essential for decision-makers, IT professionals, and entrepreneurs who need to navigate these options.
Overview of Leading PLM Software
When exploring leading PLM software, it is important to consider products like Siemens Teamcenter, PTC Windchill, and Dassault Systèmes’ ENOVIA. Each of these solutions presents distinct advantages and capabilities that cater to different industry demands.
Siemens Teamcenter emphasizes comprehensive data management, enabling users to centralize and share product information efficiently. It integrates well with existing engineering tools, providing a seamless workflow for design and manufacturing.
PTC Windchill, on the other hand, is known for its strong focus on collaboration, helping cross-functional teams work together more effectively. Its intuitive interface simplifies the management of complex product data.
Dassault Systèmes’ ENOVIA enhances product planning and development with a robust configuration management system. Its customizable dashboards allow users to gain insights into product performance and lifecycle, thus facilitating informed decision-making.
Unique Selling Points of Each Solution
Each PLM system stands out due to specific features that enhance its value proposition.
- Siemens Teamcenter
- PTC Windchill
- Dassault Systèmes’ ENOVIA
- Strength in data management capabilities
- Robust analytics for insights
- Industry-specific solutions, making it versatile across sectors
- Emphasis on collaboration tools
- Easy integration with CAD systems
- Agile configuration management, allowing rapid response to market changes
- Advanced project management features
- Comprehensive regulatory compliance capabilities
- Strong focus on sustainability and product innovation
Each of these solutions has strengths that address specific business challenges. Integrating the right PLM system can result in improved operational efficiency, cost reductions, and better product quality. Understanding these nuances is vital for making an informed choice when selecting a PLM solution.
Evaluating PLM Systems
In today’s fast-paced digital landscape, evaluating Product Lifecycle Management systems is essential for organizations seeking to optimize their operations. The evaluation process involves assessing various elements that play a crucial role in the effectiveness and suitability of PLM solutions. A comprehensive evaluation guides decision-makers in identifying a system that aligns with the specific needs of their business.
When professionals are armed with the right evaluation criteria, they can make informed choices that yield long-term benefits. These criteria often encompass various factors, including costs, user-friendliness, and scalability, among others. Failing to thoroughly evaluate these aspects can lead to poor investment decisions and hinder organizational performance.
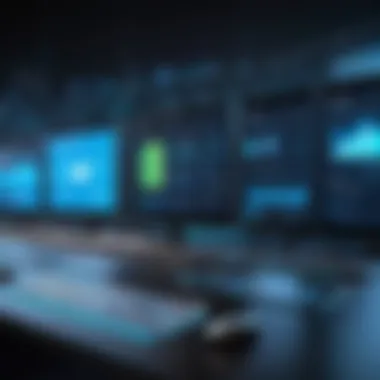
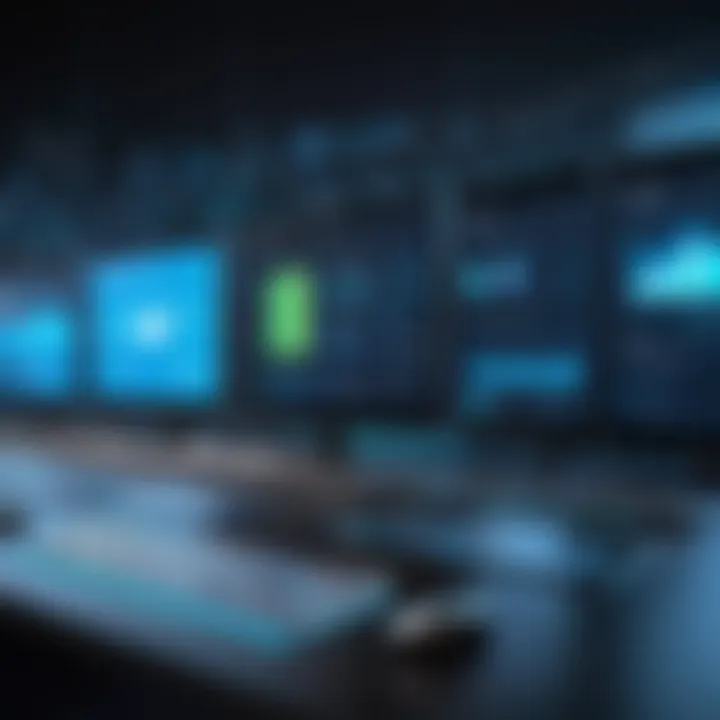
Criteria for Selection
Cost Considerations
Cost is often the first factor evaluated when selecting a PLM system. Organizations must analyze both the initial investment and the ongoing operational costs. A key characteristic of Cost Considerations is that it encompasses not just the purchase price but also licensing, maintenance, and potential upgrades. This multi-faceted view ensures a more accurate assessment of financial implications.
This detailed breakdown allows decision-makers to explore various possibilities and choose the best option that fits within budget constraints. For instance, some PLM solutions offer tiered pricing based on functionality which can be beneficial for less demanding needs. However, organizations must be cautious as low-cost solutions may lack critical features, potentially leading to higher expenses down the line.
Ease of Use
Ease of Use is another significant criterion when choosing a PLM system. A PLM solution that is intuitive and accessible increases user adoption rates, directly affecting productivity. Key here is the availability of streamlined interfaces and straightforward navigation. When users find a system easy to navigate, they can spend less time on training and more on their core responsibilities.
Some solutions may offer extensive customization, but if these customization options are complicated, they can hinder user experience. Balancing simplicity with the capability to cater to specific business needs is crucial.
Scalability
Scalability is a vital aspect for organizations anticipating growth or changes in their operational needs. A PLM system must adapt without extensive modification or added costs as the organization evolves. The key characteristic of Scalability is its ability to seamlessly handle an increased volume of data and users without compromising performance.
An advantage of choosing a scalable PLM solution is the flexibility it offers in accommodating future business changes. This can be particularly important for companies in growth phases or those that frequently adjust product lines. On the other hand, solutions that do not scale well may require additional investments or complete overhauls as demands shift, creating disruptions in operations.
User Experience
User experience is an overarching theme that affects all aspects of PLM systems. Systems designed with user experience in mind often lead to higher satisfaction and better employee engagement. These systems promote a smoother integration into day-to-day processes, resulting in less friction and confusion. Organizations should prioritize PLM solutions that value user feedback and continuously enhance their platforms to meet user needs.
"A suitable PLM system not only fulfills organizational requirements but also promotes user engagement through simplicity and effectiveness."
In summary, evaluating PLM systems with a focus on cost considerations, ease of use, and scalability allows decision-makers to select the right solution for their organizational needs. This thorough approach ultimately contributes to maximizing the effectiveness of PLM systems in optimizing product lifecycle management.
Cost Analysis of PLM Systems
Cost analysis is a fundamental aspect of evaluating Product Lifecycle Management (PLM) systems. Understanding the financial implications not only assists organizations in budgeting but also influences the long-term viability of the chosen solution. In this section, we delve into the critical components of cost analysis, which are the initial investment, ongoing costs, and the return on investment (ROI). These factors are significant in determining the total cost of ownership (TCO) and play a vital role in the overall strategic alignment of PLM initiatives with business goals.
Initial Investment vs Ongoing Costs
The initial investment in a PLM system can encompass software licensing fees, hardware purchases, and consulting or implementation services. For instance, companies might face substantial costs in the first year before they can leverage the system effectively. This upfront cash outlay is crucial for companies to understand as they budget for the new system.
On the other hand, ongoing costs typically include maintenance and support fees, subscription costs for cloud-based systems, training for staff, and possible upgrades.
It’s essential to perform a thorough evaluation of both initial and ongoing costs to understand the overall financial commitment.
To better illustrate this:
- Initial Investment:
- Ongoing Costs:
- Software Licensing: $20,000 - $100,000
- Hardware setup: $15,000 - $30,000
- Consulting Fees: $10,000 - $50,000
- Annual Support and Maintenance: 15-20% of the initial license cost
- Training Costs: $2,000 - $10,000 annually
- Cloud Subscription: $1,000 - $5,000 monthly
This data indicates that organizations must consider more than just the purchase price. Long-term budget considerations can affect the sustainability and success of PLM system adoption.
Return on Investment (ROI)
Calculating return on investment (ROI) for PLM systems can be intricate but is necessary for justifying the expenditure. ROI assesses the financial gains received compared to the investment costs. A positive ROI signifies that a PLM implementation is worth the initial and ongoing investments.
When determining ROI, organizations can quantify benefits such as:
- Enhanced efficiency and productivity
- Reduced time-to-market
- Minimized product development costs
To compute the ROI:
Consider an example where a company experiences a net profit increase of $200,000 after implementation, while the total investment was $100,000. The ROI would be:
[ \textROI = \frac200,000100,000 \times 100 = 200% ]\
This example shows how a well-evaluated PLM system can yield significant benefits over its costs. Hence, stakeholders need to focus on comprehensive ROI analysis to ensure that PLM investments are strategically sound and aligned with overall business objectives.
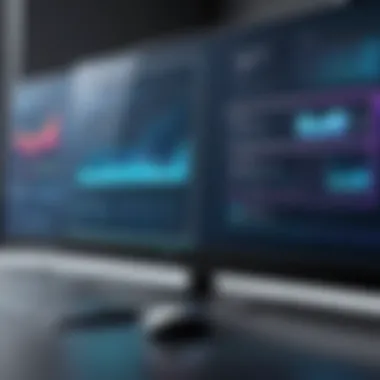
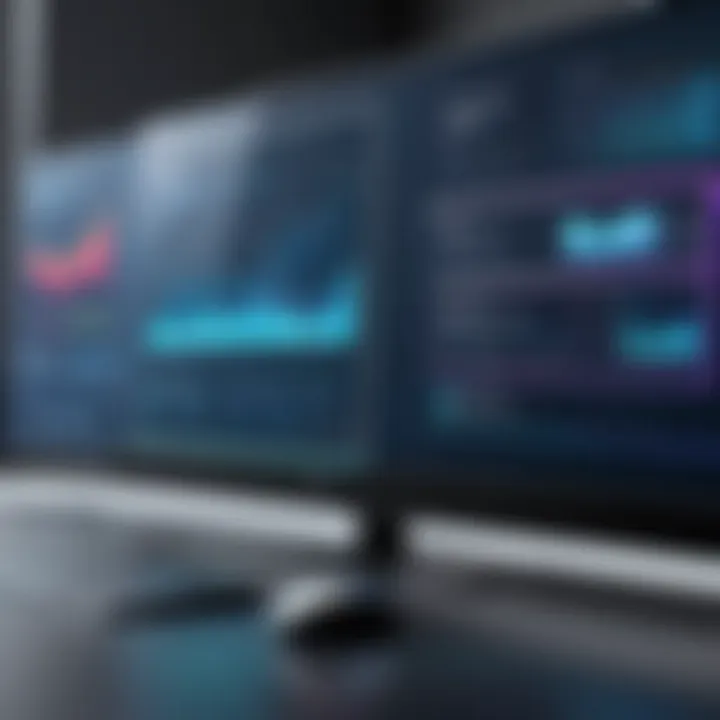
Implementation Challenges of PLM Systems
Implementing a Product Lifecycle Management (PLM) system is a critical step for organizations aiming to streamline their product development processes. However, it is not without its challenges. Understanding these implementation challenges is crucial for decision-makers and IT professionals who seek to maximize the benefits of PLM solutions. By identifying potential obstacles in advance, businesses can devise strategies to mitigate them effectively, ensuring a smoother transition and adoption process.
Common Obstacles During Deployment
The deployment of PLM systems can encounter various common obstacles that may hinder the expected outcomes. Some of the major challenges include:
- Resistance to Change: Employees may resist adopting new processes or technologies. This resistance often stems from a lack of understanding of how PLM systems enhance their workflows.
- Data Migration Issues: Transitioning from legacy systems to a new PLM system often leads to data inconsistencies or loss. Ensuring the integrity and accuracy of data during this phase is essential.
- Integration Difficulties: Many organizations operate with multiple legacy systems. Ensuring seamless integration between these systems and the new PLM solution is vital but can become complex and time-consuming.
- Insufficient Training: Users may struggle to effectively utilize the new PLM tools if they do not receive adequate training. This can lead to underutilization or misuse of the system.
- Unrealistic Expectations: Sometimes, stakeholders may have overly optimistic views regarding the capabilities of a PLM system. Setting realistic goals can help in keeping expectations aligned with actual outcomes.
Understanding these obstacles allows leaders to proactively address them, leading to a more effective deployment.
Strategies for Successful Implementation
To overcome the challenges encountered during PLM system deployment, organizations can adopt several strategies:
- Comprehensive Change Management: Engage employees by communicating the benefits of the new PLM system clearly. Encourage feedback and involve them in the transition process.
- Thorough Data Planning: Develop a robust data migration plan. Test the migration process with sample datasets to identify issues before a full-scale rollout.
- Integration Framework Establishment: Create a detailed integration strategy. This should outline how the PLM system will connect with existing software, ensuring that workflows remain uninterrupted.
- Enhanced User Training Programs: Invest in extensive training sessions tailored to various user roles. This can boost confidence and proficiency in utilizing the new system.
- Setting Realistic Timelines: Develop a phased implementation schedule that allows for gradual adaptation rather than attempting to accomplish everything at once.
"Successful PLM implementation requires not only the right tools but the right approach to change management and user engagement."
By applying these strategies, organizations can enhance their chances of a successful PLM deployment, minimizing disruptions while maximizing overall effectiveness. It is essential to view implementation not as a one-time event but as an ongoing process that requires commitment and adaptation.
Future Trends in PLM
Future trends in Product Lifecycle Management (PLM) signify a crucial area of focus for businesses looking to enhance their operational efficiency and product innovation. As global markets become more competitive, PLM systems evolve, driven by technological advancements and changing consumer expectations. Understanding these trends is essential for organizations aiming to adapt their strategies and leverage new capabilities for sustained success.
The landscape of PLM is undergoing significant transformation. This evolution presents various benefits, such as improved collaboration among teams, increased data accuracy, and enhanced product quality. Companies can gain a strategic advantage by embracing these trends, as they allow for faster reaction to market changes and customer feedback. Additionally, integrating innovative technologies into PLM can enable more efficient processes and drive better decision-making.
Emerging Technologies in PLM
Emerging technologies are reshaping the way businesses approach PLM. One notable development is the increased use of Internet of Things (IoT) devices, which facilitate real-time data collection and monitoring throughout the product lifecycle.
- IoT Integration: IoT helps in tracking product performance and user behavior after deployment. This feedback is valuable for future iterations.
- Blockchain: Implementing blockchain technology enhances transparency in the supply chain. Every transaction and change in the product lifecycle can be securely tracked and verified.
- 3D Printing: This technology allows businesses to create prototypes or even end-user products more efficiently. The implications for design and production processes are profound, leading to reduced lead times and costs.
These technologies offer critical advantages, such as better visibility into operations and the capacity for predictive analytics. Organizations can use these insights to optimize their processes continually.
The Role of AI and Automation
Artificial Intelligence (AI) and automation are central to the future of PLM. Their implementation offers numerous advantages that can significantly impact productivity and innovation.
AI can analyze vast datasets quickly, identify patterns, and provide forecasts that help businesses make informed decisions. By leveraging AI in PLM, companies can:
- Predict Outcomes: Through data analysis, AI can foresee potential issues and suggest improvements.
- Enhance Customization: AI can help tailor products to specific market needs based on consumer behavior analysis.
Automation streamlines repetitive tasks, such as data entry and reporting, allowing teams to focus on higher-value activities. This, in effect, increases efficiency and reduces the likelihood of human error.
In summary, the integration of AI and automation into PLM systems not only simplifies operations but also empowers teams to innovate faster and more effectively.
As the enterprise landscape continues to evolve, keeping abreast of these future trends is vital for businesses looking to not only survive but thrive in a constantly changing market.
Epilogue
The conclusion of this article encapsulates the multifaceted exploration of Product Lifecycle Management (PLM) systems and their significance in contemporary business practices. It is crucial to understand that selecting an appropriate PLM solution can significantly enhance an organization’s efficiency and competitive edge. This section not only synthesizes the insights presented earlier but also reinforces the importance of making well-informed decisions based on the unique requirements of each organization.
Summary of Key Insights
To summarize, several key insights emerged from the comparative analysis of PLM systems throughout this article:
- Importance of Integration: PLM systems should seamlessly integrate with current enterprise software to optimize workflow and reduce friction across departments.
- Feature Diversity: Each PLM solution offers distinct features, from data management to analytics, that cater to various organizational needs.
- Cost-Benefit Analysis: A deep understanding of both initial costs and ongoing expenses is essential for assessing the long-term value of a chosen PLM system.
- User Experience: A user-friendly interface can greatly impact adoption rates and, consequently, the overall effectiveness of the PLM system.
These insights illustrate the complexity involved in choosing the right PLM solution and underline the necessity for careful evaluation.
Final Recommendations for Buyers
For decision-makers contemplating the adoption of a PLM system, the following recommendations can guide the selection process:
- Conduct Comprehensive Research: Assess various PLM software solutions and understand their unique capabilities.
- Engage Stakeholders: Include cross-functional teams in the decision-making process to ensure that the selected system aligns with diverse needs.
- Evaluate Scalability: Choose a system that can grow with the organization and adapt to emerging technologies.
- Test User Experience: Prioritize a solution that has a strong focus on user experience, as this can impact training and support requirements.
By keeping these considerations in mind, buyers can make informed decisions that not only meet current requirements but also position their organization for future growth and innovation.
Employing a strategic approach to understanding and selecting PLM solutions ultimately leads to better alignment with business objectives, paves the way for enhanced collaboration, and delivers significant returns on investment.