Construction Equipment Maintenance Software Guide
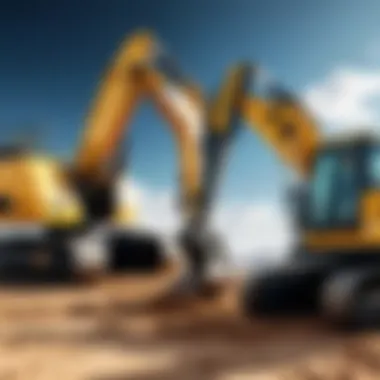
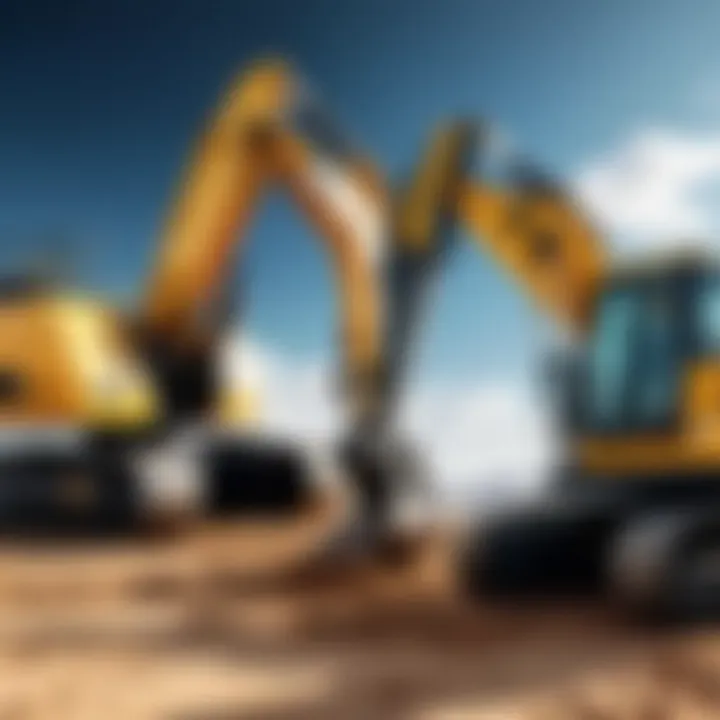
Intro
In the fast-paced world of construction, managing equipment effectively is crucial. Construction equipment maintenance software has emerged as a vital tool in ensuring that machinery is operational, efficient, and compliant with regulations. This type of software addresses several challenges that the industry faces, such as unplanned downtime, equipment failure, and regulatory compliance. With the right maintenance software in place, organizations can significantly enhance their operational efficiency.
The next sections will delve into the core features of these software solutions, assess user experience and interface design, and highlight best practices for implementation. This comprehensive understanding is designed to empower decision-makers, IT professionals, and entrepreneurs in making informed choices that align with their operational goals.
Overview of Core Features
Construction equipment maintenance software offers a variety of features essential for effective management. Key functionalities include:
- Asset Management: Track machinery and its maintenance history.
- Scheduling and Work Orders: Automate maintenance scheduling and generate work orders efficiently.
- Compliance Management: Ensure adherence to industry regulations and standards.
- Reporting and Analytics: Provide insights through data analysis for better decision-making.
- Mobile Access: Facilitate on-site updates and maintenance reporting through mobile applications.
Description of Essential Functionalities
Each of these functionalities plays a critical role in the holistic management of construction equipment. For instance, asset management allows teams to maintain comprehensive records of every piece of machinery. Scheduling and work orders automate routine checks and repairs, reducing human error and maximizing equipment utilization. Compliance management features help prevent legal issues by ensuring all machinery meets required safety and operational standards.
Comparison of Features Across Top Software Options
Understanding how these features compare across different software options is crucial. For example, software like SAM Pro is known for its robust reporting capabilities. In contrast, CMMS offers a user-friendly interface with effective mobile access. Evaluating these features helps organizations choose a system that best meets their needs.
User Experience and Interface
The effectiveness of construction equipment maintenance software is heavily influenced by its user experience (UX) and interface design (UI). A well-designed interface can significantly improve the adoption rate among employees. Features like intuitive navigation, clear visual elements, and easy access to tools are essential.
Insights into UI/UX Design Aspects
Quality UI/UX design is more than aesthetic appeal; it enhances productivity. Software that prioritizes user-friendly design encourages operators to engage fully with its features, leading to more diligent maintenance processes.
Importance of Usability and Accessibility
Usability is crucial, particularly for frontline workers who may not have extensive technical training. Software that caters to varied user skill levels ensures that everyone can utilize its features effectively. Accessibility remains critical, considering diverse work environments within the construction industry.
Prolusion to Construction Equipment Maintenance Software
Construction equipment is the backbone of any large-scale project. This equipment requires regular upkeep to function efficiently and safely. The growing complexity of these machines has led to the necessity of specialized tools to manage their maintenance. Construction equipment maintenance software plays a pivotal role in this environment. It offers a systematic approach to keeping track of maintenance tasks, schedules, and compliance requirements.
This type of software provides significant benefits that extend beyond simple tracking. A well-implemented maintenance system can directly impact productivity and operational costs. It ensures that equipment is available when needed, reduces the risk of unexpected breakdowns, and helps adhere to safety regulations.
Key Elements that Make Maintenance Software Indispensable:
- Centralized Data Management: All equipment data, including maintenance history, service schedules, and compliance reports, can be housed in one platform. This access streamlines workflows and enhances decision-making.
- Automated Alerts and Reminders: Notifications for upcoming maintenance tasks reduce the risk of oversight. This feature encourages proactive care and scheduling, which ultimately prolongs equipment lifespan.
- Regulatory Compliance: Keeping up with safety standards is crucial in the construction industry. Maintenance software provides compliance tracking, ensuring that all required inspections and maintenance are completed on schedule.
By adopting construction equipment maintenance software, companies are not just investing in a tool but are also enhancing their overall operational strategy. The following sections will delve deeper into the importance of maintenance within the construction industry and the critical features that such software should offer to maximize benefits.
The Importance of Maintenance in the Construction Industry
The role of maintenance within the construction industry cannot be overstated. Proactive maintenance of construction equipment directly correlates with operational efficiency and project success. As construction projects often operate under tight deadlines and budget constraints, maintaining equipment is crucial to avoid disruptions. Failure to conduct regular maintenance can lead to extensive downtimes and increased costs, thereby jeopardizing overall project timelines.
When equipment is not properly maintained, the risk of unexpected failures escalates. Downtime means equipment is not working and project work has to pause. This can result in delayed projects and, subsequently, increased labor costs as workers are left waiting. Moreover, postponed timelines can lead to lost opportunities and damage to reputation. For contractors, the implications can extend beyond immediate project implications; they can affect future contracts and partnerships.
Good maintenance practices also ensure equipment operates at optimal levels, enhancing productivity. When machines are functioning properly, they consume less fuel and operate more effectively, thus contributing to an overall decrease in costs. Investment in maintenance software can facilitate efficient scheduling and tracking of maintenance activities, which can significantly reduce the risk of equipment failure.
Furthermore, equipment maintenance has significant implications for safety. Regular inspections and servicing of equipment help ensure that they comply with safety standards and regulations.
In summary, maintenance is not just a task; it is a fundamental component that supports the integrity, profitability, and reliability of the construction industry. Neglecting it not only disrupts workflow but also threatens safety and profitability. Therefore, the implementation of maintenance software becomes essential in reinforcing these practices.
Impact of Equipment Downtime
Equipment downtime presents one of the most critical challenges in construction. The impact is multifaceted. First, it results in direct financial losses due to the inability to undertake work. Each hour the machinery is inactive can equate to significant loss in productivity. For instance, an excavator that is out of service can lead to delays worth thousands of dollars, depending on the scale of the project.
Additionally, projects often have milestones tied to contractual obligations. Missing these milestones due to equipment failures can lead to penalties or loss of future contracts. To put it simply, downtime translates directly to a decrease in project profitability.
Furthermore, the repercussions of downtime extend to labor. When equipment fails, labor resources become ineffective. Workers remain on-site but unable to perform their duties, leading to waste of human resources. This situation not only affects the current project but can also demoralize workers in the long run.
Safety Standards and Regulations
Safety is paramount in construction. Equipment that is improperly maintained can become a hazard. Regulatory bodies enforce strict guidelines regarding the maintenance of equipment to protect workers and ensure safe project environments. Non-compliance can lead to serious legal repercussions, including fines and work stoppages.
Regular maintenance helps to ensure that machinery meets the necessary safety standards required by law. For instance, ensuring that safety features like brakes and alarms are functional can prevent accidents on-site. By using maintenance software, companies can keep meticulous records of inspections and repairs, making it easier to demonstrate compliance during audits or inspections.
Key Features of Maintenance Software
The selection of construction equipment maintenance software hinges significantly on its key features. These features define its capacity to streamline operations, enhance productivity, and foster compliance with industry standards. Understanding these core elements enables organizations to make informed decisions about software that best meets their operational requirements.
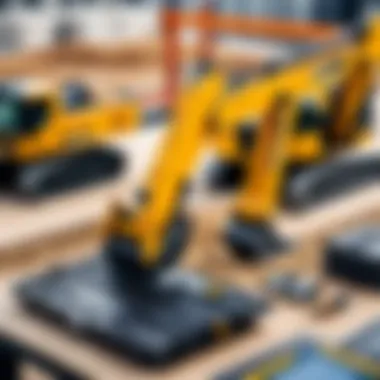
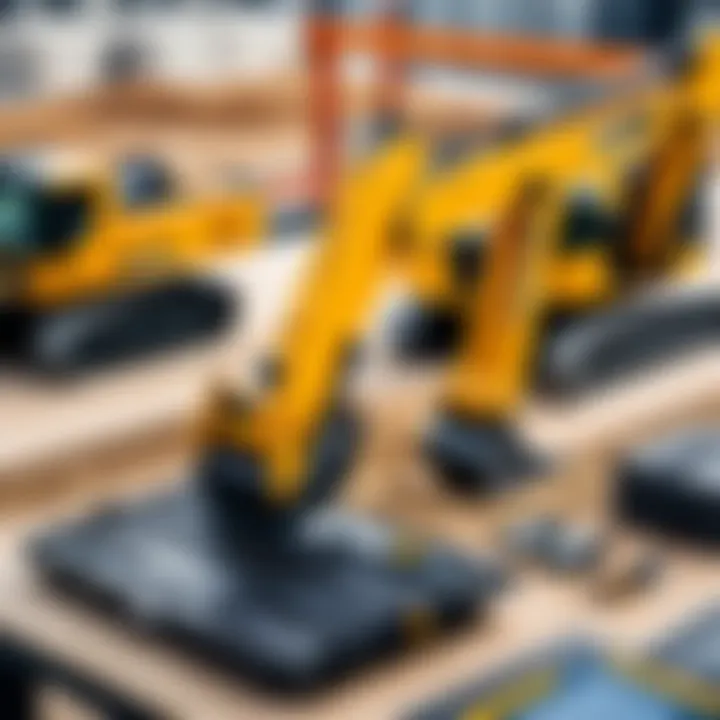
Asset Tracking and Management
Asset tracking is a crucial feature of maintenance software. By maintaining a precise inventory of all construction equipment, businesses can minimize the risks of loss or misplacement. Proper asset management enhances accountability and ensures that resources are utilized efficiently.
Additionally, this feature allows for easier identification of maintenance needs. A detailed log of each tool's usage history can indicate when it is due for servicing. Efficient tracking helps in extending the lifespan of equipment, reducing total costs over time.
Scheduling and Automated Reminders
Scheduling functionalities within maintenance software are vital for proactive maintenance management. Automation of reminder alerts about upcoming inspections or service requirements allows teams to avoid delays caused by equipment failures. This proactive approach can significantly lower the rates of unexpected downtime.
By integrating scheduling features into daily operations, companies enhance their efficiency. Employees can plan their tasks effectively knowing the maintenance timelines, thus optimizing workload distribution and improving overall project outcomes.
Real-Time Monitoring and Reporting
Real-time monitoring offers crucial insights into equipment performance and health. This feature enables supervisors to track the status of assets at any given moment. Devices equipped with sensors can relay operational data instantly, which helps in identifying any issues before they escalate.
Furthermore, robust reporting helps decision-makers understand trends over time. Analytics can highlight frequent problems or successful maintenance practices. Access to integrated data allows for improved forecasting and informed decision-making regarding future equipment investments.
Parts and Inventory Management
An essential aspect of maintenance software is managing parts and inventory. This feature can track part usage and notify when supplies are running low. Effective parts management reduces the likelihood of project delays due to unavailable components.
Additionally, it offers analytical tools for assessing which parts are most frequently used or requiring replacement. This information aids procurement decisions, ensuring that companies maintain an optimal inventory level without overstocking.
Efficient parts management streamlines the entire maintenance process, making it easier for teams to perform repairs or replacements with minimal disruption to operations.
"Integrating these key features not only contributes to smoother operations but also supports a culture of accountability and efficiency in maintenance management."
Understanding the key features of maintenance software is paramount for any organization looking to enhance efficiency and reduce costs. It enables companies to make strategic choices that align with their objectives and operational needs.
Benefits of Using Maintenance Software
The adoption of maintenance software in construction plays a vital role in improving both financial and operational aspects of projects. Such software not only offers advantages in terms of cost savings and efficiency but also helps extend the life of equipment. Additionally, these tools enhance compliance management. Let's break down these key benefits.
Cost Savings and Efficiency
One of the primary reasons companies invest in maintenance software is the potential for significant cost savings. By utilizing such software, organizations can streamline their maintenance processes. Automation of routine tasks like scheduling preventive maintenance reduces the time spent on manual work.
Moreover, tracking equipment performance allows managers to pinpoint inefficiencies or areas that require attention. When issues are detected early, they can be addressed before they escalate, reducing repair costs. This proactive approach translates into lower overall maintenance costs, directly impacting the organization’s bottom line.
A study from the Construction Industry Institute indicates that companies utilizing maintenance software can save between 10-30% on maintenance costs. Savings from enhanced efficiency and reduced downtime are essential for staying competitive in the fast-paced construction environment.
Improved Equipment Lifespan
Another significant advantage of maintenance software is its impact on equipment lifespan. Regular and systematic maintenance schedules can be easily managed through these tools. This consistent upkeep ensures that machinery operates at optimal levels.
When maintenance is neglected, equipment tends to experience more frequent breakdowns. Each unplanned failure not only causes delays but also accelerates asset depreciation. By maximizing uptime and extending the life of equipment, companies can avoid the financial strain of purchasing new machinery sooner than necessary. For example, construction firms using maintenance software report an increase in equipment lifespan by as much as 20%.
Enhanced Compliance Management
Compliance with industry regulations is non-negotiable for construction companies. Maintenance software aids in ensuring adherence to safety standards and legal requirements. This is crucial, especially as regulatory landscapes continue to evolve.
The software provides a centralized system for tracking compliance-related activities and documentation. Features such as automatic alerts for inspections and audits help organizations stay on top of deadlines. This minimizes the risk of penalties and enhances workplace safety.
Additionally, having comprehensive records readily available can be invaluable during audits or when addressing contractor inquiries. By keeping detailed logs, construction companies can quickly demonstrate their compliance efforts.
"Proper maintenance of equipment not only ensures safety but also extends the asset's useful life, making it a sound investment for any construction business."
In summary, the use of maintenance software brings a multitude of benefits to construction companies. From reduced costs and prolonged equipment lifespan to enhanced compliance management, these tools are essential in navigating the complexities of the construction industry.
Choosing the Right Maintenance Software
Selecting the right maintenance software is crucial for optimizing operational efficiencies within the construction industry. This step can significantly influence not only day-to-day operations but also long-term financial health. The software you choose should meet the unique requirements of your organization, considering factors such as size, type of equipment, and specific maintenance needs. By understanding the features available and aligning them with your operational goals, you can make a well-informed decision that will enhance productivity and reduce downtime.
Assessing Company Needs
Before exploring software options, it is essential to conduct a thorough assessment of your company’s needs. This involves evaluating the types of equipment in use, current maintenance practices, and key challenges faced in your operations.
Some questions to consider include:
- What equipment requires frequent maintenance?
- Are there existing pain points in tracking maintenance schedules?
- How does your team currently manage compliance with regulations?
By answering these questions, you can define the scope of your maintenance needs. Additionally, engaging staff may provide insights into their experiences and help identify improvements.
Evaluating Software Options
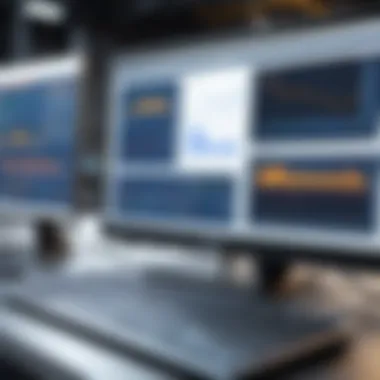
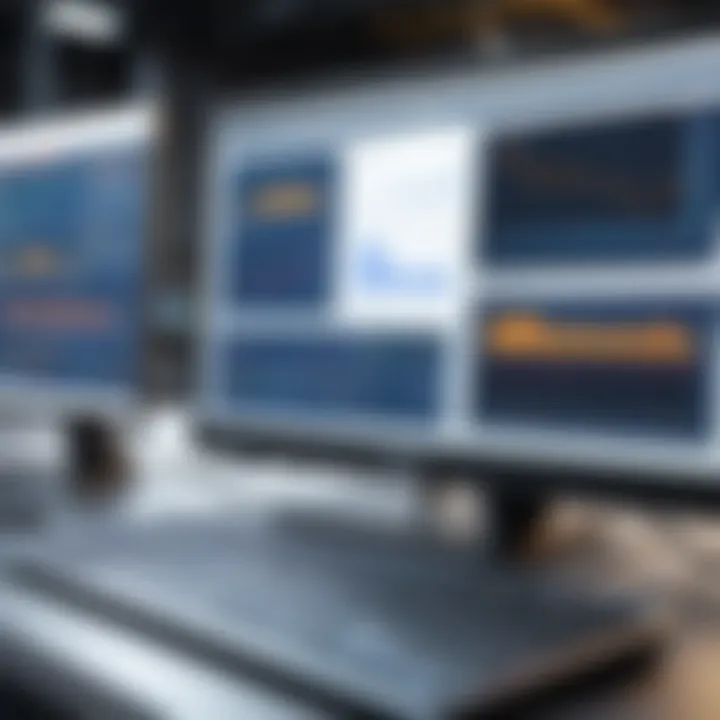
Once company needs have been assessed, the next phase is to evaluate different software options. Various solutions are available in the market, each tailored to different organizational requirements.
When evaluating software, consider the following:
- Features: Does the software include asset tracking, automated reminders, and real-time reporting?
- User Experience: Is the interface intuitive for your team? Poor usability can lead to reluctance to adopt the system.
- Cost: Does the pricing model fit your budget, including potential hidden fees?
Many vendors provide free trials or demo versions of their products, which can be beneficial. Testing multiple software in practice will help ensure it meets your company's operational standards.
Consideration of Integration Capabilities
Integration with existing systems is another critical factor when selecting maintenance software. Having seamless communication among various platforms can enhance data accuracy and improve workflows.
You should ask the following:
- Will the new software integrate with your current project management software?
- How will it connect with accounting and inventory management systems?
- Are APIs available for custom integration?
A successful integration strategy will require:
- Identifying systems that need connectivity.
- Ensuring data consistency across platforms.
- Planning for a phased integration to minimize disruptions.
By carefully considering these elements, you can choose maintenance software that aligns with your operational needs, enhances efficiency, and drives your business forward.
Implementation Strategies for Maintenance Software
The effective implementation of maintenance software is not just a technological upgrade; it is a pivotal element that shapes the operational dynamics within the construction industry. Deploying such software demands a strategic approach to ensure that the transition is seamless and that the benefits are fully realized. A well-planned implementation strategy helps mitigate potential disruptions, aligns the software with organizational goals, and maximizes user adoption.
A successful implementation begins with understanding the specific needs of the organization. Assessing current processes, identifying challenges, and setting clear objectives are essential steps. This preliminary analysis allows for tailored solutions that enhance the software's effectiveness in addressing unique operational hurdles.
Training and Development
Training and development are crucial components of any successful implementation strategy. Equipping staff with the necessary knowledge and skills to utilize the software effectively ensures a smoother transition. This involves not only initial training sessions but also ongoing educational resources and support.
- Identify key personnel who will be using the software and customize training to their roles.
- Use hands-on workshops, user manuals, and online tutorials to facilitate learning.
- Encourage the formation of user groups to share best practices and challenges.
Investing time and resources into training can significantly enhance user confidence and competency with the new software, reducing errors and improving efficiency from the outset.
Change Management Practices
Change management practices are essential to address any resistance from employees when adapting to new software. A sophisticated maintenance software system may alter established routines and processes, which can lead to apprehension among staff.
- Communicate the benefits of the new software clearly, emphasizing how it can ease workloads and enhance productivity.
- Solicit feedback from users throughout the implementation process to identify concerns and areas for improvement.
- Establish a continuous dialogue to reassure staff that their input is valued.
An effective change management approach not only facilitates smoother adoption but also fosters a positive attitude toward subsequent changes in technology and processes.
Continuous Improvement Methods
Once the software is implemented, continuous improvement methods should be in place to ensure that the system remains effective and evolves with the needs of the organization. Regular assessments, updates, and user feedback loops contribute to the ongoing efficacy of the software.
- Schedule periodic reviews of system performance and user satisfaction.
- Implement updates and enhancements based on user feedback and technological advancements.
- Foster a culture of innovation where employees feel empowered to suggest improvements and modifications.
Establishing a framework for continuous improvement ensures that the software adapts not merely to current needs but anticipates future challenges and opportunities as well.
Effective implementation strategies are crucial for maximizing the benefits of maintenance software in the construction industry. They ensure that organizations not only adopt the technology but also utilize it to its full potential, driving efficiencies and compliance in their operations.
Case Studies of Successful Software Integration
When it comes to construction equipment maintenance software, real-world examples can illuminate the value and effectivness of such systems. Case studies provide significant insights on how various organizations have implemented maintenance software. They also shed light on the specific benefits achieved, thus enabling decision-makers to make informed choices.
This section will review the application of maintenance software in different projects, focusing on improved metrics and compliance rates. The learnings from these scenarios can guide future implementations.
Project One: Improved Downtime Metrics
In a notable case, a mid-sized construction firm adopted maintenance software to address persistent equipment downtime. Prior to integration, the company experienced frequent delays in projects caused by unexpected machinery failures. The implementation of software allowed for better tracking of equipment conditions and maintenance schedules.
Key elements of this software included:
- Real-time monitoring of equipment health
- Automated alerts for upcoming maintenance tasks
- Data analytics to forecast potential failures based on historical patterns
As a result, the company noted a 30% reduction in equipment downtime within the first year. Project managers could proactively manage repairs and allocate resources efficiently. This success story emphasizes how tailored software solutions can lead to increased productivity and efficiency.
Project Two: Enhanced Compliance Rates
Another compelling example comes from a large construction organization that faced challenges with compliance to safety standards. This firm implemented a comprehensive maintenance software system that not only tracked equipment maintenance but also integrated compliance checks and audits.
The software featured:
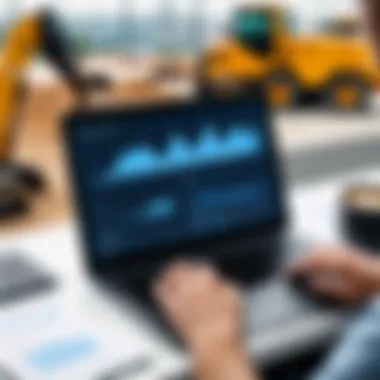
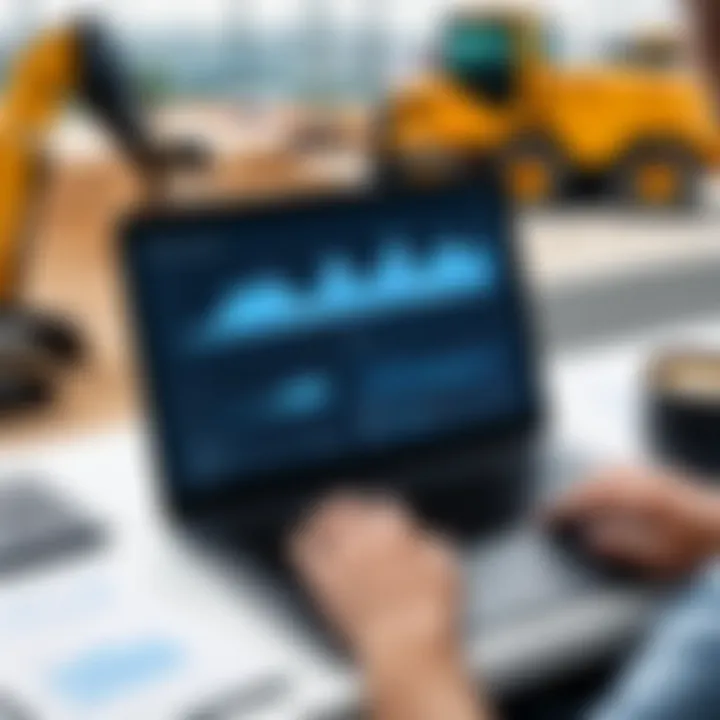
- Checklists for safety standards ensuring that all equipment met regulatory requirements
- Documentation storage for maintenance records, facilitating easy audits
- Reporting tools that could generate compliance reports quickly
Following the implementation, the organization saw their compliance rates improve by 40%. Auditors noted that the software’s ability to maintain detailed records simplified the compliance process. This case highlights the essential role of maintenance software in promoting regulatory adherence and safety in construction operations.
"Effective use of maintenance software can lead to both operational and compliance benefits, fostering a safer and more reliable working environment."
These two projects illustrate the significant impact construction equipment maintenance software can have. Improved metrics in downtime and compliance not only enhance operational efficiency but also contribute to long-term cost savings.
Challenges in Adopting Maintenance Software
Adopting maintenance software in the construction industry presents several challenges. These challenges can impede the successful implementation of software solutions, ultimately affecting overall operational efficiency. Understanding these obstacles is critical for decision-makers and IT professionals to navigate the adoption process effectively. Addressing these challenges can lead to smoother transitions and improved outcomes, making it crucial to examine them closely.
Resistance to Change
Resistance to change is one of the main barriers organizations face when implementing maintenance software. Employees may be hesitant due to fear of the unknown or discomfort with new technologies. This hesitation can stem from several sources such as job security concerns, loss of familiarity with existing processes, or simply the lack of understanding about the software's benefits.
To counteract resistance, organizations should focus on clear communication about the advantages of the new system. Training sessions can be instrumental in making staff feel comfortable with the software. Engaging employees early in the process can also foster a sense of ownership, easing transition anxieties.
Some strategies to consider include:
- Open Dialogues: Create forums for employees to express their concerns and suggestions.
- Involvement in Decisions: Include key personnel in the selection and implementation process.
- Routine Feedback: Seek employee feedback post-implementation to adjust training and usage strategies continually.
Data Loss and Migration Issues
Data loss during migration is another significant concern when adopting maintenance software. This process involves transferring substantial amounts of data from older systems to new platforms. If not managed well, it can result in lost records, corrupted files, or incomplete data sets.
To mitigate these risks, thorough planning and execution during the migration process are essential. Here are some recommended practices:
- Data Backup: Always create a complete data backup before initiating migration.
- Testing Phases: Implement a phased approach to migration, testing data integrity at each stage before full deployment.
- Professional Assistance: Engage IT professionals or consultants with experience in data migration to oversee the process, ensuring no detail is overlooked.
By addressing resistance to change and carefully managing data migration, organizations can better navigate the challenges of adopting maintenance software. This proactive approach lays the foundation for maximizing the software's benefits, ensuring long-term success.
Future Trends in Construction Equipment Maintenance Software
The construction industry is evolving, and so is the technology that supports it. Future trends in construction equipment maintenance software will significantly impact how businesses operate, enhance efficiency, and improve compliance. Understanding these trends allows industry professionals to stay ahead and make informed decisions.
As we look into the future, two prominent trends are emerging: Artificial Intelligence and Predictive Maintenance and Integration with IoT Devices. Both trends hold the potential to transform maintenance practices and elevate operational standards.
Artificial Intelligence and Predictive Maintenance
Artificial Intelligence (AI) is advancing quickly, becoming a pivotal part of construction equipment maintenance. The integration of AI algorithms allows for analyzing vast amounts of data generated by equipment. This technology is instrumental in identifying patterns that signify potential equipment failures before they occur.
Predictive maintenance utilizes data analytics to forecast maintenance needs based on actual usage patterns and wear. This proactive approach reduces unplanned downtimes and saves costs associated with emergency repairs.
Benefits of AI in Predictive Maintenance:
- Reduced Downtime: By anticipating failures, companies can schedule maintenance when it least impacts operations.
- Cost-effectiveness: Avoiding costly repairs leads to overall savings. Companies can allocate resources more effectively.
- Enhanced Operational Efficiency: Continuous monitoring provides insight into equipment health, allowing for better decision-making.
Considering these advantages, decision-makers should keep abreast of AI developments. Intelligent systems ensure that the right maintenance is conducted at the right time, ultimately improving productivity.
Integration with IoT Devices
The Internet of Things (IoT) represents a significant shift in how equipment is monitored and managed. IoT devices can be deployed on construction machinery to gather real-time data regarding operational performance and condition. This connectivity facilitates an unparalleled level of oversight.
Key aspects of IoT integration:
- Real-Time Data Collection: Continuous data streams offer real-time insights into performance issues, empowering timely responses.
- Remote Monitoring: Stakeholders can monitor equipment health from remote locations, enhancing decision-making efficiency.
- Data-Driven Decisions: Accumulated data allows for analysis and strategic planning, driving improvements across operations.
As IoT continues to develop, the construction sector must embrace this technology. The right integration can lead to substantial improvements in equipment reliability and operational transparency.
"The future of construction maintenance lies in proactive, data-driven decision making supported by advances in AI and IoT technologies."
The End: The Path Forward for Construction Maintenance
The future of construction equipment maintenance lies in the effective use of software solutions. The importance of maintenance software cannot be overstated. As the construction industry evolves, so too must the methods by which equipment is managed and maintained. Companies that leverage technology to streamline processes will significantly improve efficiency and productivity.
Specific Elements to Consider
Key components in the next steps of maintenance software adoption include:
- Data Analytics: Utilizing data analytics allows for better insights into equipment performance. This can help in predicting failures before they occur, thus reducing unexpected downtimes.
- Customization: Every construction operation has unique needs. Therefore, selecting a software solution that offers customization options can better fit specific operational workflows.
- User Training: Ongoing education and training for staff are crucial. Without sufficient training, the effectiveness of the software can diminish, leading to underutilization or misapplication of the tools available.
Benefits of Embracing Future Developments
Investing in maintenance software can provide numerous advantages. For instance, it enhances accountability and oversight by allowing real-time tracking of equipment status across different projects. Furthermore, it elevates compliance with industry standards, reinforcing safety protocols that minimize risks on site.
Considerations for Decision-Makers
When making decisions about future investments in maintenance software, consider the following:
- Integration Capabilities: Ensure compatibility with current systems to avoid data silos and streamline operations.
- Scalability: As your company grows, the software should also be able to scale and adapt to increasing demands.
- Vendor Support: Evaluate the support services offered by software vendors. Solid support can ease the transition and enhance the user experience.