Exploring Creo Solid Modeling: Insights and Applications
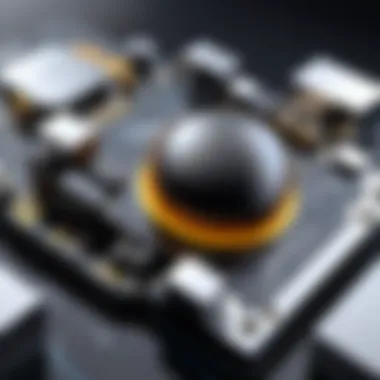
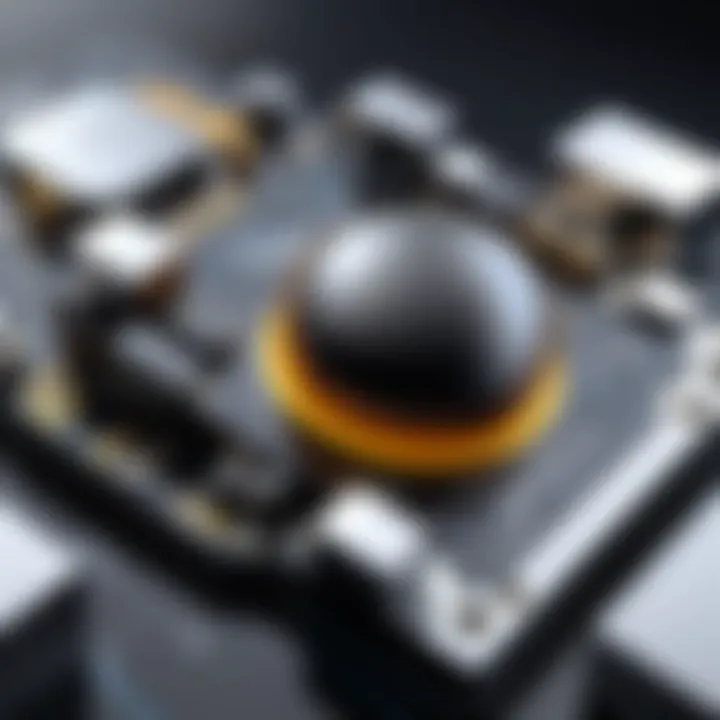
Intro
Creo Solid Modeling emerges as an essential tool in today’s engineering landscape. This powerful CAD software integrates a wide range of functionalities tailored for product design, making it a preferred choice in multiple industries. The current competitive environment demands tools that do more than just basic design tasks. Understanding the underlying features and applications of Creo helps professionals not only in optimizing workflows but also in driving innovation.
Its robust capabilities enable users to model intricately and efficiently, responding to dynamic market needs. As we delve into the various aspects of Creo Solid Modeling, the focus will remain on functionalities, user experience, and specific use cases across sectors.
Overview of Core Features
Creo Solid Modeling is known for its extensive suite of tools designed to streamline product design processes. Here are some essential functionalities:
- Parametric Modeling: Enables the creation of models driven by parameters, allowing for easy alterations and adjustments.
- Flexible Modeling: Allows users to manipulate complex geometries without the need for complete rebuilding of the model, enhancing productivity.
- Simulation and Analysis Tools: Integrates simulation for validating designs against physical constraints earlier in the workflow.
- Assembly Modeling: Supports intricate assembly creation, with tools dedicated to manage and visualize complex assemblies effectively.
- Streamlined Collaboration: Facilitates collaborative work environments, where teams can share models and workflows seamlessly.
When comparing Creo with other top software options like SolidWorks and Autodesk Inventor, it’s clear that each has its strengths. However, users often note that Creo’s parametric capabilities offer a level of flexibility that can surpass other solutions in complex design scenarios.
Moreover, the simulation tools offered by Creo allow for more robust testing phases, ultimately reducing errors in the final product. While SolidWorks may excel in user-friendliness, the depth of Creo’s features appeals to seasoned engineers who prioritize functionality over simplicity.
User Experience and Interface
The user interface of Creo Solid Modeling is crucial for optimizing the design workflow. The layout provides users with easy access to tools while maintaining focus on the design task.
Insights into UI/UX design show that Creo balances function and simplicity. Key aspects contributing to a positive user experience include:
- Customizable Toolbars: Users can arrange tools that suit their workflows, improving efficiency.
- Quick Access to Commands: The search functionality makes it easy to find tools without navigating through multiple menus.
- Clear Visual Displays: High-quality rendering of designs helps in visualizing the final product effectively.
Usability stands as a critical factor in software adoption. Engineers often prioritize tools that minimize the learning curve while maximizing output capabilities. Accessibility is another concern, as firms look for solutions that are intuitive and can be learned quickly, allowing teams to stay agile and responsive.
"In the competitive landscape of CAD tools, user experience plays a pivotal role in determining the software's overall efficiency."
Understanding how to navigate Creo’s interface and effectively utilize its core features ultimately drives better design outcomes. As companies adopt advanced software like Creo, it is crucial for decision-makers to invest time in training and familiarization to harness its full potential.
Prolusion to Creo Solid Modeling
Creo Solid Modeling represents a significant advancement in Computer-Aided Design (CAD) technologies, incorporating powerful tools to enhance product development processes across various industries. Understanding the fundamentals of Creo is crucial for professionals seeking to maximize design efficiency and improve collaboration in engineering teams. This section provides a comprehensive introduction to solid modeling, its historical development, and its importance in design engineering today.
Historical Context
The origins of solid modeling date back to the 1960s, a period when CAD systems began to shift from 2D drafting to 3D modeling techniques. Early systems were limited, focusing on simple wireframe representations. However, advancements in computing power and algorithms enabled the creation of more sophisticated solid modeling techniques. Creo emerged in the late 1980s, developed by PTC (Parametric Technology Corporation). It was one of the first systems to use parametric and associative modeling, allowing designers to work with defined parameters that automatically update when changes are made. This historical evolution underscores the importance of continuous innovation in CAD tools, as manufacturers increasingly seek to streamline operations.
Overview of Solid Modeling
Solid modeling is a mathematical representation of three-dimensional objects, encapsulating their properties and allowing for more detailed designs. It provides a comprehensive view of an object's geometry, including volume, mass, and surface area calculations. Creo offers various modeling techniques, including feature-based, parametric, and direct modeling approaches. Each method caters to different user needs and design requirements, ensuring flexibility in the design process.
Key features of solid modeling in Creo include:
- Parametric Design: Allows users to define specific constraints and relationships between modeling elements, leading to adaptable designs.
- 3D Visualization: Facilitates accurate representation of designs in a visual format, aiding in better understanding and presentation.
- Detailed Analysis: Provides tools for simulation and analysis, which are integral for testing functionality before physical prototyping.
Significance in Design Engineering
The relevance of solid modeling in design engineering cannot be overstated. It enhances the overall design process, promoting efficiency, accuracy, and innovation. By utilizing solid modeling through Creo, engineers and designers can easily visualize complex geometries, conduct virtual testing, and collaborate effectively across teams. The impact is evident in several ways:
- Efficiency: The ability to make and track changes quickly reduces time to market.
- Collaboration: Solid models can be easily shared among teams, fostering teamwork and communication.
- Cost Reduction: Virtual prototyping minimizes the need for physical models, significantly lowering development costs.
- Enhanced Innovation: Designers can experiment with new ideas and iterations efficiently, promoting a culture of creativity in product development.
Core Features of Creo
The core features of Creo are fundamental to understanding its effectiveness in the realm of computer-aided design (CAD). Creo provides robust tools that enhance design precision and efficiency. These features play a critical role in boosting productivity across various projects in industries such as aerospace, automotive, and consumer products. This section will delve into the significant aspects of parametric modeling, 3D design capabilities, sheet metal design, and assembly modeling.
Parametric Modeling
Parametric modeling is one of the most pivotal features of Creo. It allows designers to create models that are directly driven by parameters. Modifications made to one aspect of the design automatically update related components. This interconnectedness not only saves time but also minimizes errors during the redesign process.
Knowing how to effectively utilize the parametric approach is essential. It enables users to create complex models quickly, adapting designs in response to changing requirements efficiently. This flexibility is indispensable in competitive markets where adaptability is crucial for staying relevant.
3D Design Capabilities
Creo stands out for its advanced 3D design capabilities. These include features like solid modeling, surface modeling, and sheet metal capabilities. Users can generate detailed 3D representations of their designs with relative ease.
The 3D design environment in Creo also allows for interactive visualization. This means designers can see how their models adjust in real time, providing immediate feedback and enhancing the overall design experience. A unique feature is that it supports both direct and parametric modeling. Hence, it accommodates various workflows, suiting individual user preferences and project needs.
Sheet Metal Design
Sheet metal design in Creo is particularly useful for industries that require precision in fabrication and engineering. Creo simplifies the design process for sheet metal components. Users can create flat patterns directly from 3D models, optimizing material usage.
That capability is critical in environments where costs are a consideration. Furthermore, sheet metal design tools in Creo allow for rapid adjustments, ensuring that specifications are met without excessive rework. This expedites the manufacturing process while maintaining quality standards.
Assembly Modeling
Assembly modeling is another cornerstone of Creo's functionality. It helps in managing complex assemblies by allowing users to organize components systematically. The assembly process is pivotal in industries such as automotive or aerospace, where intricate systems must work seamlessly together.
In Creo, assembly modeling tools allow for the integration of various parts into a cohesive unit. This contributes to not only visualization but also to part interference checks, ensuring accuracy in fit and function. Therefore, these tools are vital in validating design integrity before moving into production.
Overall, the core features of Creo empower users with tools that enhance their design capabilities. The importance of understanding these features cannot be overstated as they are key to navigating the complexities of modern product design.
Understanding Creo Interface
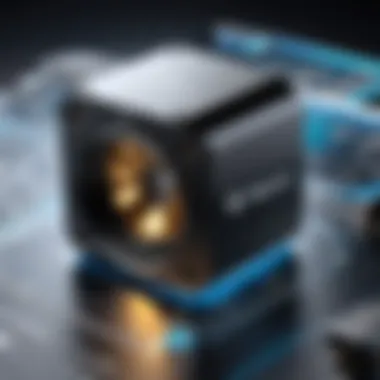

The interface of Creo Solid Modeling plays a crucial role in how users interact with the software. A well-designed interface simplifies workflows, enhances user productivity, and improves the overall experience in product design and engineering. Understanding the Creo interface is important for anyone aiming to utilize its full potential.
User Interface Layout
The user interface layout of Creo consists of several key components that are critical for efficient navigation and operation. The main elements include the ribbon, toolbars, and display windows. The ribbon houses the various commands related to design features, while toolbars offer quick access to frequently used tools. The display windows present 3D models, allowing users to rotate, zoom, and pan to examine their designs from various angles.
The layout can be initially overwhelming for new users due to the multitude of options available. However, acclimating to the layout can lead to improved efficiency. Familiarization with the layout can significantly reduce the time required to locate specific functions, which enhances overall workflow.
Navigating the Workspace
Navigating the workspace in Creo is essential for executing design tasks smoothly. Tools such as the navigation bar and view controls facilitate movement around the 3D model. Users can easily switch between different views, such as isometric or orthographic projections. Understanding hotkeys and shortcuts can further expedite navigation.
An important aspect of navigation is the use of context menus. These menus appear when a user right-clicks on an object or workspace area, providing relevant commands based on the selected item. Leveraging these context menus is crucial as they help optimize the speed of operation, allowing designers to focus on the task rather than the mechanics of using the software.
Customization Options
Customization options in Creo enable users to tailor the interface to their specific needs, which can lead to enhanced productivity. Users can rearrange toolbars, create custom shortcuts, and define workspace layouts that suit their workflows. This adaptability can be especially beneficial for teams working on complex projects, where individual preferences may vary.
To customize the interface, users can access the configuration settings within Creo. From there, they can modify various elements such as the color scheme, display dimensions, and command placements, aligning the software with personal or organizational standards.
"The ability to customize your workspace in Creo enhances not only individual productivity but also team collaboration, fostering a more efficient design environment."
Advanced Techniques in Creo
Advanced techniques in Creo Solid Modeling play a crucial role in enhancing the design and engineering process. These techniques not only extend the basic capabilities of the software but also empower users to create more complex models with optimal efficiency. In this section, we will examine three key advanced techniques: surface modeling, generative design, and collaboration tools. Each of these techniques provides unique benefits, addressing various challenges faced by design professionals today.
Surface Modeling
Surface modeling is an essential technique in Creo that allows users to create intricate shapes and complex geometries. Unlike solid modeling, which constructs objects through volume, surface modeling focuses on the exterior shell. This method is particularly useful when designing aesthetically appealing products or parts with non-uniform shapes, such as automotive bodies or consumer electronics.
Surface modeling provides several advantages:
- Precision: Designers can achieve a high degree of accuracy in their models, crucial for industries requiring strict tolerances.
- Flexibility: It enables frequent adjustments and edits, responding swiftly to changes in design requirements.
- Integration: Surfaces can be combined with solid elements, allowing for hybrid designs that leverage the strengths of both modeling methods.
However, working with surface modeling requires a solid understanding of mathematical principles and an eye for detailed work. Given its complexity, mastering surface modeling can significantly elevate a designer's skill set.
Generative Design
Generative design represents a transformative shift in how products are developed. This technique uses algorithms and cloud computing to explore a wide range of design alternatives based on specific input parameters. Engineers can define their goals - whether optimizing for weight, material usage, or strength - and the software generates numerous design options that meet those criteria.
The benefits of generative design include:
- Efficiency: It reduces the time spent on manual iterations, speeding up the design process.
- Innovation: By allowing the software to produce unforeseen designs, it encourages creative solutions.
- Sustainability: Generative design often leads to more material-efficient structures, contributing to environmental goals.
As industries increasingly adopt automation and AI-driven processes, adopting generative design in Creo may become more crucial for staying competitive.
Collaboration Tools
In today’s interconnected world, effective collaboration among teams is vital. Creo offers various collaboration tools that facilitate real-time communication and coordination among stakeholders. These tools allow design teams to share models, gather feedback, and make decisions collaboratively, regardless of their physical locations.
Key features of Creo's collaboration tools include:
- Model Sharing: Users can easily share their designs with colleagues or clients, ensuring everyone is on the same page.
- Real-Time Feedback: Immediate feedback can be integrated directly into the design process, leading to quicker iterations.
- Version Control: Teams can track changes made to models over time, preventing confusion and loss of data.
Effective collaboration tools are essential for modern project management. They foster a more inclusive environment where multiple perspectives can contribute to the final product, aligning with the ever-demanding expectations of the market.
"The integration of advanced techniques in Creo is not merely about adopting new tools; it is about rethinking how design practices are performed, paving a path for innovation and efficiency."
In summary, mastering advanced techniques such as surface modeling, generative design, and collaboration tools enhances proficiency in Creo Solid Modeling. Such skills not only improve individual capabilities but also contribute to a more agile and innovative design process across industries.
Applications of Creo in Various Industries
Creo Solid Modeling is an essential tool across several industries due to its versatility and advanced features. Its ability to facilitate complex design processes and integrate various engineering functions makes it invaluable. Organizations utilize Creo not only to improve the quality of their products but also to enhance efficiency and reduce time-to-market.
The applications of Creo are diverse, ranging from the aerospace sector to medical devices. Each sector has unique challenges and requirements, and Creo addresses these through its robust capabilities. Below is a detailed analysis of how Creo finds its application in four key industries.
Aerospace Sector
In the aerospace sector, precision and reliability are paramount. Creo solid modeling provides engineers with tools to create intricate designs for aircraft components, ensuring they meet strict safety standards. The software supports complex surface modeling, essential for aerodynamic components.
Furthermore, companies in this field benefit from Creo’s ability to manage large assemblies.
- Key elements for aerospace applications include:
- Advanced simulation capabilities that predict performance and stress factors.
- Lifecycle management tools to track component revisions.
- Integration with PLM systems for better collaboration.
Overall, Creo enhances not only the design process but also the validation and verification phases in aerospace engineering.
Automotive Industry
The automotive sector leverages Creo for its comprehensive design features, particularly for creating detailed 3D models of vehicles. With the push towards electric and autonomous vehicles, designers rely on Creo to innovate while ensuring compliance with safety regulations.
- Some important benefits for automotive applications are:

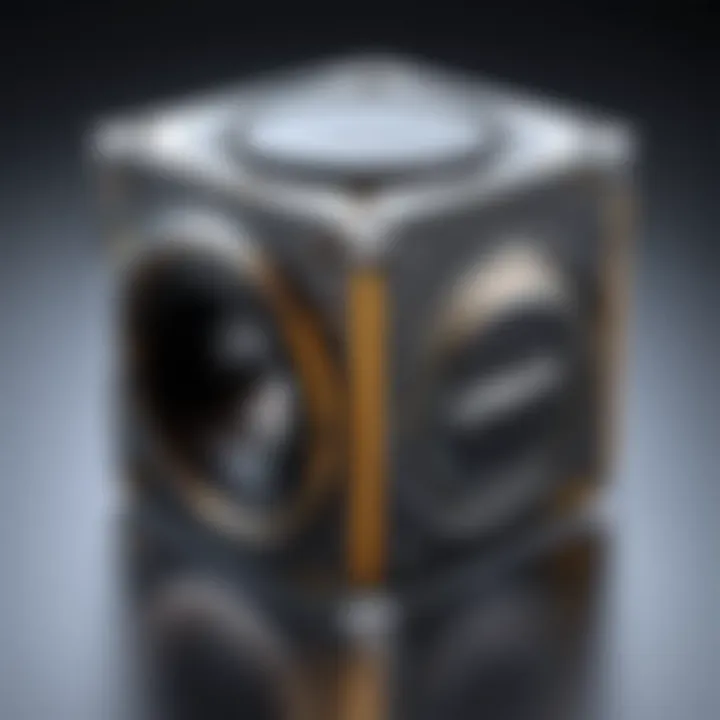
- Streamlined design workflows that facilitate collaboration among teams.
- Extensive tools for simulating motion and stress in moving parts.
- The ability to integrate with other simulation tools for enhanced testing.
Automotive manufacturers can quickly iterate designs and adapt to new technology trends thanks to Creo’s flexible modeling capabilities.
Consumer Products
In the consumer products industry, time-to-market is critical. Creo aids product designers in creating appealing, functional designs quickly. Whether it ’s electronics, furniture, or household goods, the software helps in rendering prototypes that can be easily modified based on feedback.
- Considerations for consumer product applications include:
- User-focused design tools that allow customization.
- Prototyping features that expedite the development process.
- Sustainability considerations, supporting designs that reduce material waste.
Thus, Creo not only supports the design phase but also retains flexibility in product adjustments post-consumer testing.
Medical Devices
The medical device industry demands precision and compliance with regulatory standards. Creo Solid Modeling plays a crucial role in developing complex medical devices such as implants and surgical instruments. The software accommodates the intricate details required for these devices, ensuring accuracy in every aspect of the design.
- Benefits of using Creo in this sector involve:
- Comprehensive analysis tools to examine device performance under various conditions.
- Models that can be tailored to specific patient needs, enhancing personalized medicine.
- Efficient documentation processes which assist in regulatory approvals.
In summary, Creo acts as a foundational tool in addressing both the design and regulatory challenges present in the development of medical devices.
Integration with Other Tools
Integration with other tools plays a crucial role in maximizing the effectiveness of Creo Solid Modeling. In a landscape where efficiency and collaboration are key, the ability to seamlessly connect Creo with various software solutions enhances the overall productivity of design teams. Such integrations allow for a more streamlined workflow, enabling teams to share data across platforms, thus eliminating silos that traditionally hinder communication.
Effective integration can lead to significant improvements in collaboration between departments. For instance, when Creo is connected to Product Lifecycle Management (PLM) software, it enhances the management of product data and maintains the integrity of design updates. This synergy ensures that all stakeholders have access to the most current design iterations and specifications, reducing the risks associated with version discrepancies. Archiving historical data becomes easier, enabling teams to track design evolution over time.
Moreover, integrating Creo with simulation and analysis tools allows designers to validate their concepts in real time, significantly shortening the product development cycle. Product designs can be tested and optimized virtually before any physical prototypes are created. This not only conserves resources but also provides critical insights into performance and manufacturability earlier in the process, enabling more informed decision-making.
PLM Software Integration
Integrating Creo with PLM software offers numerous advantages. PLM systems manage the entire lifecycle of a product, from inception through engineering design and manufacturing to service and disposal. By connecting Creo with PLM systems, companies can enhance data consistency and collaboration within their teams, leading to improved product innovation.
- Version Management: PLM integration allows for rigorous version control, reducing the risk of working on outdated files.
- Centralized Data Access: Teams can access product data from a central repository, facilitating faster decision-making and reduced project delays.
- Compliance and Reporting: Enhanced reporting capabilities ensure compliance with industry standards and regulations, simplifying audit processes.
"When Creo is linked to PLM systems, teams can achieve greater coherence in their design projects, reducing time to market by as much as 20% in some sectors."
Simulation and Analysis Tools
Simulation and analysis tools are essential in modern product design, and their integration with Creo brings a host of benefits. These tools enable engineers to assess how designs will behave under real-world conditions. By embedding simulation capabilities within the Creo environment, users can conduct tests on how their models perform while simultaneously creating and modifying designs.
The integration provides:
- Real-time Feedback: Designers receive immediate validation of their concepts, allowing for quick adjustments based on simulation results, which is vital for reducing errors downstream.
- Optimized Designs: With capabilities such as finite element analysis and computational fluid dynamics, engineers can fine-tune elements of their designs to enhance performance and reduce material wastage.
- Cost-effective Solutions: Early detection of potential flaws can save companies from incurring extensive costs tied to later-stage revisions or manufacturing defects.
In summary, the integration of Creo with various tools—be it PLM systems or simulation applications—creates an interconnected design environment that fosters innovation and efficiency. For decision-makers and IT professionals, recognizing these integration opportunities is key to unlocking the full potential of Creo Solid Modeling in their organizations.
Creo in the Context of Industry Trends
The evolution of design technologies significantly influences how products are developed and brought to market. Creo Solid Modeling is no exception. Its capabilities align closely with current industry trends, especially in the areas of digital transformation and sustainability. Understanding these trends is essential for decision-makers aiming to leverage Creo effectively within their organizations.
Impact of Digital Transformation
Digital transformation fundamentally changes the landscape of product design. Companies increasingly adopt advanced technologies such as artificial intelligence, cloud computing, and the Internet of Things to enhance their processes. Creo Solid Modeling embraces these changes by offering robust tools that facilitate efficient design workflows.
- Cloud collaboration: Creo allows teams to work remotely, ensuring that all members can access the latest design updates in real time. This is crucial in a world where remote work has become a norm.
- Integration with AI: The incorporation of artificial intelligence features helps automate repetitive tasks in design, freeing up engineers to focus on more complex challenges.
"Companies that embrace digital transformation can create more streamlined processes, leading to faster time-to-market for products."
Sustainability Considerations
As organizations strive to minimize their environmental impact, sustainability increasingly informs design decisions. Creo Solid Modeling assists companies in meeting these challenges.
- Material efficiency: Creo's advanced simulation tools enable designers to assess materials thoroughly before production. Optimizing material use not only reduces waste but also lowers costs.
- Lifecycle analysis: The software supports lifecycle assessments that consider a product's environmental impact from inception to disposal. This encourages designs that contribute to sustainable practices.
- Regulatory compliance: With rising awareness of environmental regulations, Creo helps firms ensure their products adhere to these laws during the design phase.
Challenges in Implementing Creo
Implementing Creo Solid Modeling presents specific challenges that users should be well aware of. Recognizing these challenges is essential for maximizing the efficiency of this powerful CAD tool. The difficulties encountered during the implementation phase can significantly impact productivity, project timelines, and overall design quality. Therefore, it is crucial to thoroughly understand these challenges to implement Creo effectively.
Learning Curve for New Users
Many new users often struggle with the learning curve associated with Creo. Although the software offers advanced features, its complexity can be overwhelming at first. Users may find the user interface unintuitive.
Here are several aspects related to the learning curve:
- Diverse Tools: Creo includes a wide array of tools, each designed for various applications. New users may spend considerable time learning where to find these tools and how to use them effectively.
- Tutorials and Training: It's vital to engage with official training programs to ease this transition. Tutorials provided by PTC and third-party resources can help new users to gain confidence.
- User Community: Joining forums and communities, like those on Reddit, can be beneficial. Experienced users share valuable tips and solutions to common problems.
In sum, organizations need to be aware of this learning hurdle and prepare their teams accordingly through adequate training and resources.
System Requirements and Performance
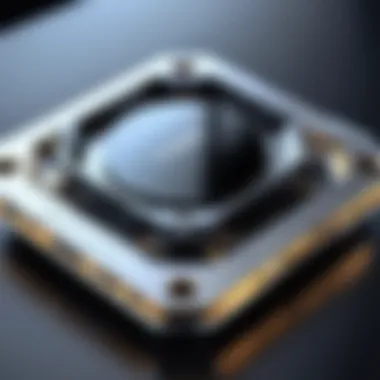
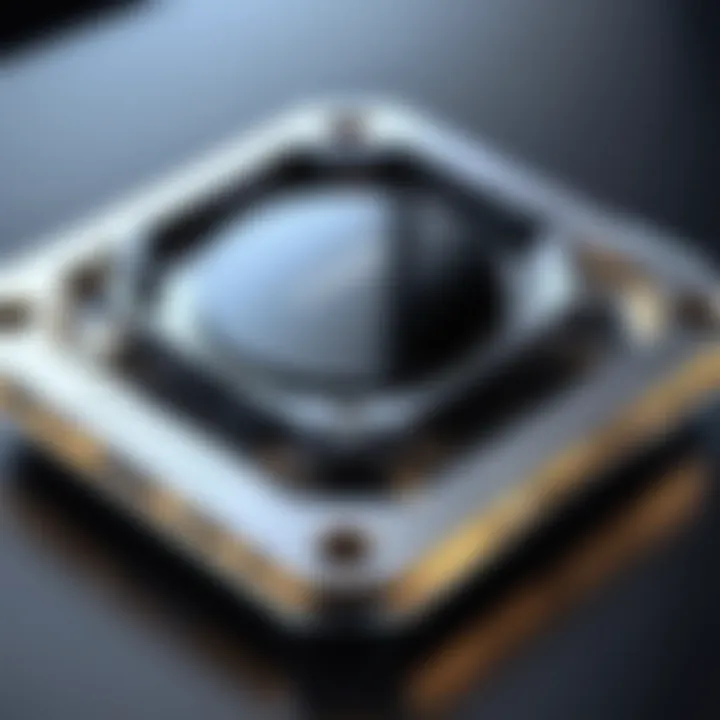
The performance of Creo is significantly influenced by system requirements, which can pose a challenge for users, particularly in resource-limited settings. To run Creo smoothly, it's important to have a computer that meets or exceeds the recommended specifications.
Factors to consider include:
- Minimum Specifications: Failing to meet even the minimum system requirements can lead to slow performance and even crashes.
- Hardware Upgrades: Organizations may need to invest in hardware upgrades such as faster processors, more RAM, and better graphics cards. Ignoring these specifications could impact the software's effectiveness in handling large models or complex assemblies.
- Software Compatibility: It is also essential for users to ensure compatibility with existing software tools used alongside Creo.
In summary, careful consideration of system requirements will ensure that users can leverage Creo's capabilities fully while minimizing potential frustrations.
Best Practices for Using Creo
Using Creo effectively requires a clear understanding of its capabilities and certain best practices that can enhance workflow and productivity. Precise organization and a robust approach to version control are crucial elements that can lead to a successful experience with this software. By following specific methods and recommendations, users can maximize their efficiency and improve collaborative efforts.
Organizing Projects Efficiently
Effective project organization is foundational in Creo. This not only facilitates better management of design files but also streamlines collaboration among team members. Key practices to consider include:
- Creating a Logical Directory Structure: Designate folders for specific projects, components, or phases of design. This minimizes the time spent searching for files.
- Naming Conventions: Develop and follow consistent naming conventions for files and folders. This helps in quickly identifying content without opening each file. For instance, include project names, version numbers, or modification dates in the file names.
- Using Templates: Establish templates for common components or assemblies. This can save time and ensure consistency in design elements across projects.
- Documentation: Maintain comprehensive documentation regarding each project’s objectives, processes, and decisions. This can be invaluable for both current users and future reference.
Structured organization contributes to a smoother workflow and enhances communication. When all members understand where to find files and how the project is structured, it reduces uncertainty and boosts productivity.
Version Control Management
Version control in Creo is essential for sustaining the integrity of design data. Keeping track of changes, maintaining historical records, and preventing data loss or conflicts among multiple users are key advantages of a systematic version control process. Consider the following:
- Use of Creo's Built-in Version Control: Leverage Creo’s inherent version control features to track changes automatically. This means that every save can capture a snapshot of your work, allowing easy rollback if necessary.
- Regular Check-ins and Check-outs: When collaborating, always check in designs after modifications. This allows others to see the most updated version, reducing the chances of discrepancies.
- Keep Logs of Changes: Document what changes were made in each version. This log should include details such as who made the change, why, and what exactly was modified. This provides clarity and can prevent confusion in team dynamics.
- Integration with PLM Systems: If available, incorporate Product Lifecycle Management (PLM) solutions that can enhance version control and overall project management. Such tools offer advanced features for automation and collaboration.
The implementation of proper version control strategies can significantly reduce errors and miscommunication in multi-user environments.
Training and Resources for Creo Users
Understanding how to effectively utilize Creo Solid Modeling is crucial for professionals in engineering and design fields. Proper training and access to quality resources can significantly enhance the efficiency and effectiveness of this software in real-world applications. Organizations that invest in these elements set themselves up for success.
Official Training Programs
Official training programs for Creo Solid Modeling are essential for new users to build a solid foundation in the software. Programs typically offer structured learning pathways, covering everything from basic functionalities to advanced features. These trainings help in understanding parametric modeling, assembly creation, and specialized design functions.
Several options exist for official training.
- PTC University offers various courses tailored to different experience levels. Users can engage in instructor-led sessions, which often include hands-on projects that simulate real scenarios.
- Online Learning platforms can also provide self-paced courses, making it easier for users to fit training into their schedules.
These programs often include certification opportunities, which serve as a benchmark of competence in Creo Solid Modeling. Certificates can enhance job prospects and career advancement in a competitive job market.
Community Forums and Support
Community forums and support channels are invaluable supplements to formal training. These platforms allow users to connect with others who have similar questions or challenges. The collective wisdom found in such spaces can lead to innovative problem-solving.
For instance, the Creo Community on Reddit offers a space for users to ask questions and share tips. Additionally, professional forums facilitate discussions about best practices and troubleshooting.
Benefits of engaging in community forums include:
- Learning from the experiences of other users.
- Accessing a wider range of solutions beyond official documentation.
- Networking with professionals in similar fields.
Future Directions for Creo Development
The future of Creo Solid Modeling hinges on its ability to adapt and innovate within an increasingly dynamic technological landscape. Emerging trends in digital design, automation, and artificial intelligence are shaping the possibilities for Creo. Each advancement not only enhances its usability but also widens its applicability across various sectors. Understanding these future directions is crucial for businesses looking to maintain competitiveness in design and engineering.
Emerging Technologies
As technology evolves, Creo must keep pace with several key innovations that impact modeling and design processes.
- Cloud Computing: The shift to cloud-based platforms allows for real-time collaboration among design teams, irrespective of geographical boundaries. This fosters enhanced teamwork and accelerates decision-making processes.
- Artificial Intelligence: Incorporating AI tools within Creo can lead to smarter design suggestions and automated error detection. This enhances efficiency and reduces the number of revisions required in the design phase.
- 3D Printing Integration: As additive manufacturing continues to gain traction, Creo's compatibility with 3D printing technologies is essential. This integration allows designers to directly translate digital models into physical products, streamlining the production process.
These technologies do not only improve workflows but also empower users to push the boundaries of creativity in product design.
User Feedback Integration
The importance of integrating user feedback cannot be overstated. Creo’s development must be guided by actual user experience and needs.
- User-Centric Design: Adopting a user-centered approach means prioritizing interface simplicity and functionality based on the feedback from designers and engineers who use Creo daily.
- Iterative Development: Regularly updating the software in response to user insights ensures that the tool remains relevant. This could include improved features, streamlined processes, and user-requested functionalities.
- Community Engagement: Engaging with the user community through forums and feedback systems enables Creo to stay attuned to market demands and innovations.
Collectively, integrating user feedback into future plans not only helps in refining features but also builds a loyal user base that feels heard and valued.
"Future development should not merely reflect technological trends but should also consider the voices of those who utilize the tools daily."
The End
In evaluating the significance of Creo Solid Modeling, it is essential to synthesize the various discussions presented throughout this article. Creo serves as a fundamental tool in product design and engineering, addressing the needs of diverse industries with its robust features and flexible applications. The ability to create, analyze, and modify designs in a cohesive environment greatly enhances productivity. Decision-makers and IT professionals benefit from its advanced functionalities that facilitate collaboration and efficiency in the design process.
Recap of Core Points
This article provided a thorough exploration of Creo Solid Modeling, emphasizing key aspects such as:
- Historical context: Understanding how Creo evolved and its current place in CAD tools.
- Core features: Detailed insights into parametric modeling, 3D design capabilities, and other essential tools.
- Applications in various industries: Insights into sectors like aerospace, automotive, consumer products, and medical devices, illustrating its versatility.
- Integration and collaboration: Importance of integrating Creo with other tools, enhancing its usability in digital workflows.
- Training resources: Encouraging professionals to utilize training and community support for better utilization.
This recap serves as a reference point to reinforce the importance of Creo in achieving innovative product designs and supporting efficient engineering practices.
Final Thoughts
Solid modeling is no longer a mere design function; it is a crucial element in modern engineering workflows. Creo Solid Modeling is at the forefront of this evolution, positioning itself as a necessary tool for organizations aiming to stay competitive. As industries continue to navigate challenges such as digital transformation and sustainability, the role of Creo in fostering efficient design processes cannot be overstated.