Building an Efficient Inventory Management System
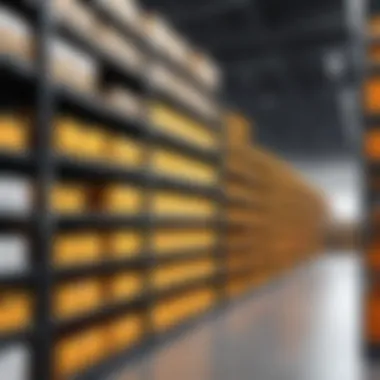
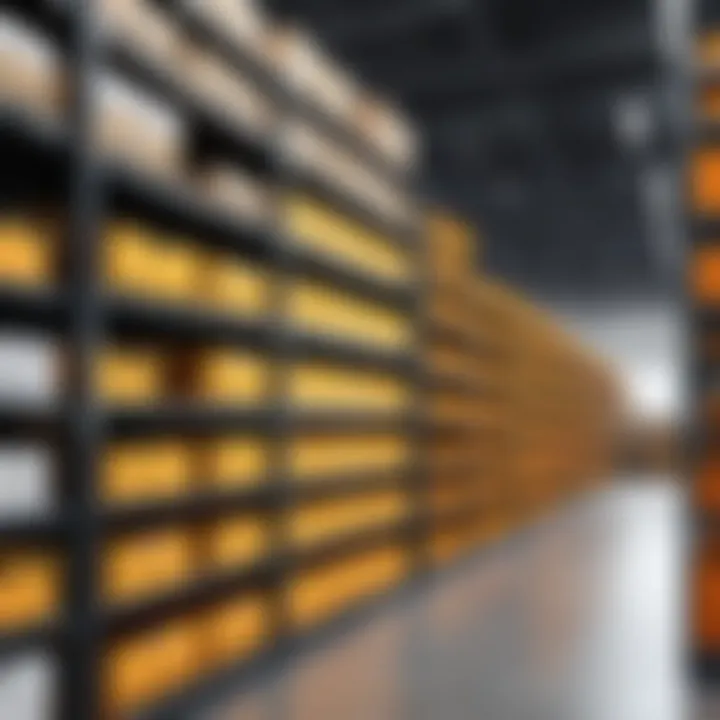
Intro
Inventory management might just seem like another part of the supply chain puzzle, but in reality, itâs like the backbone of a business. An efficient inventory management system gets everything running smoothly, ensuring that products are available when customers want them while also keeping costs down. Without it, a business can easily find itself lost in the weeds, bogged down by excess stock or running out of key items.
Why is inventory management so critical? When a company knows precisely what it has, it can make informed decisions that lead to greater customer satisfaction and improved profitability. Having real-time insights gives a business a competitive edge; itâs about making the right decisions at the right time. Tracking inventory can reveal trends, highlight discrepancies, and facilitate a strategic approach to stock replenishment that keeps a business agile in a dynamic market.
This article dives deep into the various features that help build a robust inventory system, aligns software choices with business needs, and provides solid strategies to enhance operational efficiency. We will cover everything from user experience to the essential functionalities required to sustain an efficient inventory management system. Letâs take a closer look at the elements that make up an effective approach towards inventory oversight.
Overview of Core Features
An effective inventory management system must encompass a range of functionalities that speak directly to the unique needs of a business. Here are some essential features to consider:
- Real-Time Tracking: The ability to know inventory levels and product locations at all times is paramount. Having real-time data helps businesses avoid stockouts and overstocking situations, effectively improving service levels.
- Automated Reordering: A robust system not only tracks levels but also automates the ordering process when stock falls below a certain threshold.
- Multi-Location Management: For businesses operating in several locations, the ability to manage inventory across stores or warehouses is vital. This feature allows for better resource allocation and reduces the risk of stock discrepancies.
- Reporting and Analytics: Being able to generate reports and analyze inventory trends plays a significant role in strategic decision-making. It allows businesses to understand sales patterns and optimize their stock accordingly.
Description of essential functionalities
Essential functionalities include:
- Barcode Scanning: This streamlines the tracking of inventory items through mobile devices. Scanning barcodes reduces human error and speeds up the check-in and check-out process.
- User Permissions and Access Control: Tailoring access to inventory levels according to roles ensures data integrity and prevents unauthorized changes.
- Integration with Other Systems: The capability to integrate with accounting, sales, or supply chain management software creates a seamless information flow, minimizing data silos and improving accuracy.
Comparison of features across top software options
When it comes to selecting the right software, taking a look at several it can make a difference. For instance:
- TradeGecko (now QuickBooks Commerce) is user-friendly with strong integration capabilities, ideal for small to medium enterprises.
- Fishbowl Inventory offers robust features like multi-location tracking, appealing to larger companies with complex inventory needs.
- Cin7 integrates inventory management directly with eCommerce and point-of-sale systems, ideal for businesses wanting to synchronize various sales channels.
User Experience and Interface
A system is only as efficient as it is easy to use. User experience (UX) and interface play a massive role in how well employees can adopt the software. An interface that is user-friendly reduces the learning curve, allowing employees to get up to speed quickly. Key considerations include:
- Intuitive Navigation: Users should be able to navigate the software without excess training. Clear visual hierarchies and simple layouts enhance usability.
- Responsive Design: As more businesses operate on the go, having a system that operates well on mobile devices is essential. This ensures that team members can access necessary information when and where they need it.
Insights into UI/UX design aspects
Good design encompasses not only aesthetics but also functional aspects. A clean, uncluttered interface can greatly improve efficiency. Color coding inventory levels, for instance, allows users to gauge stock status at a glance, enabling quicker responses.
Importance of usability and accessibility
Every team member should feel comfortable navigating the system, regardless of their tech skills. A well-designed inventory system reduces the barriers to learning, allowing employees of all backgrounds to manage stock efficiently. Facilities that consider global implications, such as different languages and cultural contexts in software design, can further enhance accessibility.
"An inventory system is like the ship, and the user experience is the sails; without good sails, the ship won't get far."
By focusing on these core features and user experience considerations, businesses can build a solid foundation for an effective inventory management system that supports long-term growth and operational efficiency.
Understanding Inventory Management
Inventory management is not just a back-end operation; it's the heartbeat of many businesses, making sure that goods flow smoothly from procurement to the customer. If done right, it can help a company run like a well-oiled machine, optimizing costs, improving customer satisfaction, and increasing efficiency. Understanding this topic is crucial before diving into the nitty-gritty of creating an effective inventory management system. It encompasses a comprehensive grasp of how inventory works, its critical components, and how managing stock can directly impact your bottom line.
Definition and Importance
At its core, inventory management refers to the overseeing of supplies and materials that a business holds for the purpose of resale or production. This includes raw materials, finished products, and work-in-progress items. Proper inventory management is like the glue that binds everything in a supply chain together. When inventory is not managed correctly, a company can face stock shortages, excess stock, and cash flow problems. This can lead to unhappy customers, missed sales opportunities, or wasted resources. Therefore, itâs not simply about keeping tabs on what you have; itâs about making strategic decisions to enhance efficiency and profitability.
Key Components of Inventory Management
Several vital components make up an effective inventory management strategy. Understanding these components is paramount for any business aiming to enhance its inventory oversight.
Stock Levels
Stock levels are about knowing exactly how much of each product you have at any given time. Maintaining appropriate stock levels is crucial to ensuring that a business can meet customer demand without overstocking items that may lead to increased carrying costs. Striking the right balance between too little and too much inventory can be challenging, but itâs a necessary hurdle to leap over. A unique feature of stock levels is just-in-time (JIT) management, which minimizes the amount of inventory kept on hand. This method benefits businesses by reducing costs associated with storage and spoilage. However, the downside is being vulnerable to sudden demand increases or supply chain disruptions.
Product Location
Knowing where every product is stored can save time and money. Proper product location management enhances efficiency in retrieval, minimizing lead-times and maximizing throughput. A business may implement a systematic arrangement or zoning, thereby categorizing products based on their sales velocity or type. The key characteristic is to minimize the distance between the picking area and the storage area. However, issues arise when over-relying on just one area or layout without adapting to changing business dynamics. Adaptability is crucial for maintaining balance in product locations.
Inventory Valuation
This aspect refers to determining the monetary value of inventory. Valuing inventory accurately is crucial for reporting and financial planning. Methods vary, such as FIFO (First In, First Out) and LIFO (Last In, First Out), each impacting the final value differenty during financial assessments. Inventory valuation sets the baseline for assessing profitability, cash flow, and stock levels. Not managing inventory valuation correctly can lead to distorted financial results, impacting decision-making abilities. While this aspect possesses its complexities, a clear understanding models better outcomes for businesses in their forecasting and troubleshooting.
The interplay of these components reveals how understanding inventory management provides businesses actionable insights. By grasping the definition, importance, and key components, companies can streamline operations and make informed decisions, ultimately steering towards sustainable profitability.
Establishing Objectives
Setting objectives in inventory management isnât just a step; it's a cornerstone. Without clear objectives, your efforts can feel like a boat without a paddle: aimless and stuck in murky waters. When you take the time to establish what your business needs from its inventory system, you unlock a path to improved efficiency and cost-effectiveness.
Assessing Business Needs
The first step in establishing objectives is to assess your specific business needs. Think of it as discovering your treasure mapâknowing where you stand indicates how to get where you want to go. Examine your products, your market, and the challenges your organization faces. For example, if you manage a clothing store, you may need to track seasons closely to prevent excess stock that could get buried under the next year's styles.
Critical questions to consider:
- What are your peak selling seasons?
- Are there specific products that often run low?
- How fast do your products move through the supply chain?
By answering these questions, you can develop tailored objectives that align with your operations.
Setting Measurable Goals
Once you've assessed your needs, the next step is turning those insights into measurable goals. This isnât just about waving a wand and hoping for the best. It involves defining outcomes that allow you to track progress and validate the effectiveness of your strategies. Here are three measurable goals that can lead to a robust inventory management strategy:
Reducing Stockouts
One of the primary objectives in inventory management is reducing stockouts. When a product runs out, itâs not just an inconvenience; itâs an opportunity lost. Think about your favorite cafĂ© running out of your preferred coffee right before peak hours. Not only does it frustrate customers, but it also eats into profits.
Key characteristic: Reducing stockouts keeps shelves stocked, ensuring customers leave satisfied rather than empty-handed.
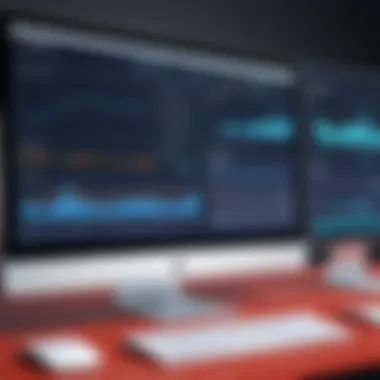
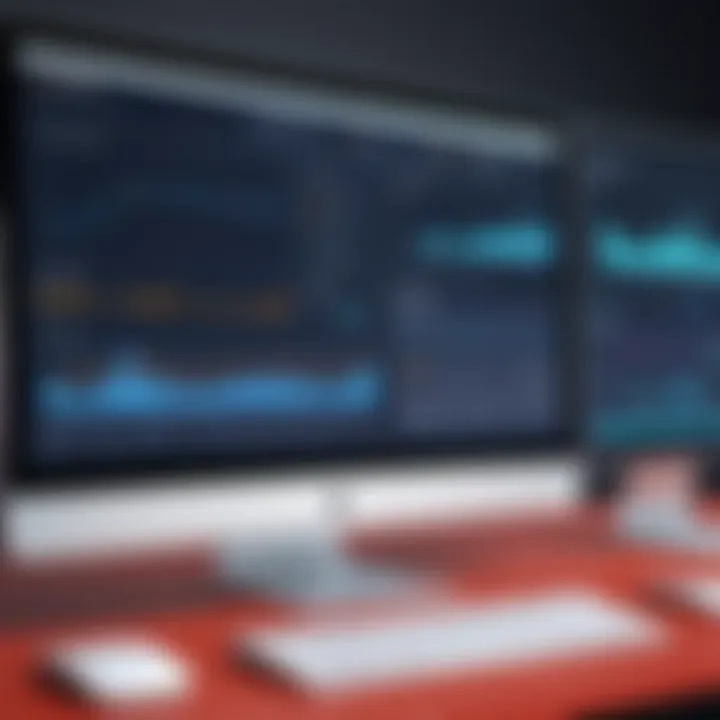
Unique feature: This goal often involves analyzing sales trends and maintaining a buffer stock to cover demand peaks. A precise balance can minimize carrying costs and enhance overall customer satisfaction, though it might mean investing in better tracking methods and perhaps software solutions.
Minimizing Carrying Costs
Carrying costs might sound mundane, but they stack up quickly, impacting your bottom line. These costs include all expenses associated with holding inventoryâstorage fees, insurance, depreciation, and opportunity costs.
Key characteristic: A strong focus on minimizing carrying costs ensures that your cash flow isnât tied up in excess stock that you canât move.
Unique feature: Implementing strategies like Just-In-Time (JIT) inventory can drastically reduce these costs by only ordering what you need when you need it, minimizing clutter. However, JIT comes with its own risks, particularly with supplier reliability, so it's essential to weigh these dangers.
Enhancing Fulfillment Speed
In todayâs fast-paced world, consumers expect speedy deliveries. Enhancing fulfillment speed can give your business a leg up on the competition. Consider a retailer that promises two-day shipping: If inventory processes are lagging, this promise can quickly crumble.
Key characteristic: Streamlining processes, from warehousing to order picking, can significantly boost your ability to meet customer demand.
Unique feature: Efficient systems can leverage various technologiesâlike automated tracking systemsâthat allow businesses to move goods faster. However, relying too heavily on technology can sometimes lead to information overload and confusion if not managed correctly.
Setting clear, meaningful objectives is not just a task but a transformative opportunity to elevate your entire inventory management process.
Choosing Inventory Management Software
Selecting the right inventory management software can make or break your operational efficiency and profitability. In an age where agility is key, the capability to respond swiftly to changes in stock levels and demand can be the fine line between success and failure. An effective software solution helps streamline workflows, reduce human errors, and provide visibility that ultimately enhances decision-making processes.
Critical Features to Consider
When embarking on the journey to find inventory management software, several key features can significantly impact the outcome. Understanding these options can save time, money, and headaches down the line.
Real-Time Tracking
Real-Time Tracking is a cornerstone of modern inventory management systems. This feature enables businesses to monitor stock levels as they change, providing up-to-the-minute information on what is available. With this functionality, businesses can reduce the dreaded stockouts that frequently disrupt operations and create customer dissatisfaction.
One particularly advantageous characteristic of real-time tracking is its ability to integrate with various sales channels. Imagine a scenario where an online store and a physical retail location share inventory data seamlessly. This reduces confusion and ensures that your inventory reflects what is genuinely on hand. A unique aspect of this feature is the use of technology such as barcoding or RFID tags to improve accuracy. While the setup might be time-consuming or cost-intensive, the long-term benefits often outweigh the initial hurdles.
Reporting Tools
Reporting Tools act like a compass in the chaotic world of inventory. They provide insightful analytics that inform business decisions. Itâs not just about knowing how much stock you have; itâs understanding trends over time. Say you notice a drop in sales for a specific item over several months. This information allows you to pivot your strategy accordingly.
These tools often come with customizable dashboards that allow you to visualize data without needing a PhD in statistics. However, they can become overwhelming if too many metrics clutter your view. So, while their depth can be a blessing, clarity should be the priority.
Integration Capabilities
Integration Capabilities refer to how well the inventory software melds with other systems, such as your accounting software or e-commerce platforms. Imagine a world where sales data flows automatically into your inventory management software, eliminating manual entry and the mistakes that inevitably come along with it. A robust integration feature can save time and improve accuracy by ensuring that everything works in harmony.
This characteristic makes it easier to implement updates across systems, providing a clearer financial picture for decision-makers to utilize. However, itâs crucial to thoroughly evaluate how well these integration capabilities work with your existing tools. If they lack compatibility, you could be setting yourself up for more frustration than ease.
Evaluating Software Options
Choosing the right software doesn't just happen overnight; it necessitates careful consideration and evaluation of multiple options available in the market. Being methodical during this phase can significantly boost your confidence in your final choice.
Comparative Analysis
Comparative Analysis allows businesses to stack various programs against each other to gauge which aligns best with their needs. This process helps highlight each software's strengths and weaknesses and can uncover unexpected features that may prove beneficial.
When conducting a comparative analysis, look for aspects such as user-friendliness, scalability, and support options. Desirable features might highlight unique selling points of some software solutions, but also note potential pitfalls that can be hidden behind flashy promotions. By creating a side-by-side assessment, you're much likelier to make a choice that serves your long-term strategy.
User Reviews
User Reviews are essential to getting a grounded perspective on any software solution. This feedback offers real-world insights into how well a program performs daily. Consider how current users describe their experienceâare they singing praises or lamenting technical glitches?
One key feature of user reviews is the opportunity to understand how software responds to problems and its customer service quality. A responsive support system is often just as crucial as the software's features. However, stay skeptical. A handful of glowing reviews may not disclose ongoing issues that a company is facing.
Cost Considerations
Cost Considerations remain one of the leading factors influencing software selection. It's tempting to lean toward the cheapest option available, but this may lead to cutting corners that can cost you later. The right question isn't just, "What's the price?" Instead, ask about the total cost of ownershipâthis includes training, subscriptions, maintenance, and upgrades.
Balancing price with features is essential to ensure you receive value for your investment. Many solutions offer a tiered pricing structure that aligns costs with the features provided. This way, you can find a solution with adequate functionality without breaking the bank.
"Properly managing your inventory isnât just about a piece of software; itâs about understanding the needs of your business and finding tools that help you meet those needs efficiently."
Inventory Tracking Methods
In the realm of inventory management, having robust tracking methods is vital. This allows businesses to maintain precise control over their stock, enhance operational efficiency, and reduce costs. By choosing the right inventory tracking method, organizations can respond swiftly to market demands, minimize waste, and optimize overall performance. In this section, we delve deeper into the two prevalent inventory tracking systems: Barcode and RFID systems, and the contrasting approaches of manual versus automated tracking.
Barcode and RFID Systems
Barcode systems have been staples in inventory management for decades. Using simple barcodes that can be scanned with handheld devices, businesses can quickly access product information. The efficiency here is crystallized in the speed of data entry, where a mere scan can update inventory levels almost instantaneously. Beyond mere convenience, barcodes help reduce human error, which often plagues manual entries.
On the other hand, RFID (Radio Frequency Identification) systems go a step further to enhance automation. With RFID tags, products can be tracked without direct line of sight, significantly speeding up inventory counts and checks. These systems can scan multiple items at once. This is particularly useful in larger warehouses where time is of the essence. However, setting up RFID can be costly, which might limit its appeal for smaller businesses.
Both systems can integrate with modern inventory management software, creating a cohesive operation that's both accurate and efficient.
Manual vs. Automated Tracking
Pros and Cons of Manual Tracking
Manual tracking is often viewed as a double-edged sword. On the one hand, it tends to be more intuitive, especially for smaller operations with limited stock. Businesses can maintain direct oversight over each item, fostering a hands-on approach to inventory management. This method requires minimal upfront investment, as it generally relies on basic tools such as spreadsheets and paper logs.
However, the drawbacks cannot be ignored. Human error is a significant concernâmistakes can arise from simple miscounts or incorrect entries. Other issues include time consumption; as a business grows, the manual processes can become a bottleneck, leading to delayed responses to stock needs.
This approach can work in certain contexts; however, as inventory demands scale up, so too do the potential for mistakes.
Advantages of Automation
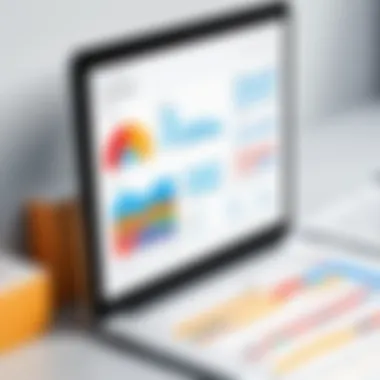
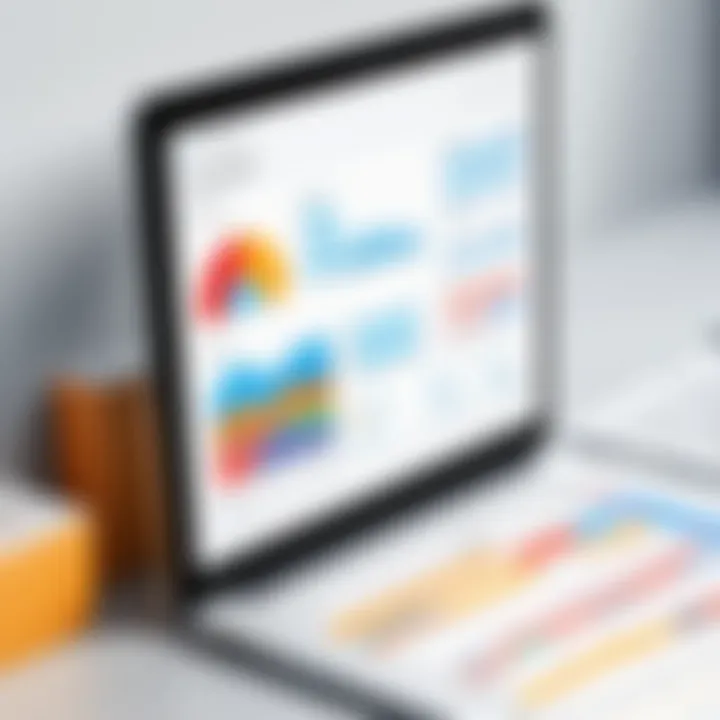
Automation, in contrast, showcases a myriad of benefits that serve the overarching goal of effective inventory management. The foremost characteristic is speed; automated systems drastically reduce the time spent on data entry and inventory checks. Software solutions can analyze stock levels in real-time, providing businesses with accurate insights into product availability and demand spikes.
Another significant advantage lies in data accuracy. Automated systems minimize human error by syncing inventory counts directly with sales channels and supply orders. This reliability is crucial for maintaining strong customer satisfaction, as stock discrepancies can lead to stockouts or overstocking.
While the initial investment in automation may be higher, the long-term returns often justify it. Businesses experience enhanced productivity and often realize savings in labor costs and reduced inventory holding costs over time.
In today's fast-paced market, choosing between manual and automated inventory tracking can make or break a businessâs efficiency.
Understanding these methods and weighing their pros and cons will empower decision-makers to choose a strategy that aligns well with their operational goals. Each approach offers distinct advantages, and the most effective inventory management system may require a tailored blend of methods.
Implementation Process
Implementing an effective inventory management system is like laying down the tracks for a train that's destined for success. Without proper implementation, even the best strategies can derail into chaos. This process is essential because it not only determines how smoothly the system will function but also directly impacts the efficiency, accuracy, and overall success of inventory operations. A well-thought-out implementation can result in minimized stock discrepancies, better fulfillment rates, and ultimately, enhanced customer satisfaction. Itâs about connecting all dots: from understanding technical requirements to rallying the staff behind the new processes. A structured rollout can mitigate teething issues that often come with adopting new systems, setting the stage for robust management.
Planning the Rollout
The backbone of any successful inventory system is a meticulous rollout plan. Itâs crucial to dedicate time to this aspect, as it encompasses everything from establishing a timeline to allocating resources effectively. Having an organized plan is not just about checking boxes; itâs about aligning the inventory management goals with the operational capabilities of the business.
To kick things off, managers should begin with a comprehensive assessment of the current inventory processes. What works well? What doesn't? This analysis will serve as the foundation upon which the new system is built. Once the purpose and goals are clear, the next step involves drafting a timeline. This timeline should include key milestones and deadlines to ensure the project stays on track. Being proactive in setting these benchmarks fosters accountability among team members and keeps spirits high throughout the roll-out.
Additionally, involving stakeholders early in the process is invaluable. Getting feedback from various departments provides a holistic picture and can elevate the outcomes. This democratic approach helps to address concerns before they can escalate and fosters a collaborative atmosphere. It's worth noting that patience is key; rollouts often face hiccups and adjustments may be necessary to fine-tune the approach.
Training Staff Effectively
Training is the spine of any successful implementation. If your team doesn't know how to utilize the new system effectively, it could render all the previous efforts useless. Staff training isn't just about teaching the use of new tools, itâs about fostering a culture of adaptability and continuous improvement.
Training Needs Assessment
Before diving into the training, it's paramount to conduct a training needs assessment. This step identifies the specific skills gaps and knowledge deficiencies within the team. By doing so, organizations can tailor their training sessions to address the precise needs of their staff rather than engaging in a one-size-fits-all solution.
The key characteristic of a training needs assessment lies in its focus on individual and group competencies. Itâs a beneficial choice for organizations aiming for a meaningful transformation rather than a superficial fix. Moreover, a unique feature of this assessment is its potential to highlight specific software functionalities that employees may find challenging. Understanding where the stumbling blocks are allows for targeted training sessions, which can lead to improved efficiency down the line.
However, one disadvantage might arise from miscommunication about what the assessment aims to achieve. Sometimes it can lead to anxiety among staff, as they might fear being judged based on their current skill level. It's crucial to frame these assessments positively, focusing on growth and development rather than criticism.
Developing Training Materials
Creating proper training materials is integral to the success of any training program. These materials should not just be instructional; they must be engaging, user-friendly, and tailored to implement the new inventory management system effectively. When designed thoughtfully, training materials act as continuous resources for the staff, rather than just one-off guides.
The key characteristic of developing training materials is that they should reflect the specific processes and tools relevant to the organization. This specificity makes the training much more relatable and practical. Organizations often find it beneficial to involve employees in the material development stage. They can provide insights regarding missing topics or unclear functionalities, which leads to a comprehensive training experience.
A unique feature of these training materials is their adaptability. They can come in various forms: videos, manuals, FAQs, and even interactive simulations. This variety helps cater to different learning styles within the team, promoting better retention of information.
While the advantages are clear, a potential disadvantage is the time investment needed to create high-quality materials. It can drain resources if not managed properly. To manage this, it's wise to start with essential topics, then gradually expand the materials as needed.
"An ounce of prevention is worth a pound of cure." This quote rings especially true in the context of inventory management implementation. By being thorough and thoughtful in the rollout and training phases, businesses can prevent countless issues down the line.
Establishing Inventory Policies
Establishing inventory policies is a crucial step in developing an effective inventory management system. These policies define how inventory is handled, tracked, and replenished, ensuring smooth operations and minimizing losses. When a business has clear inventory policies in place, it can significantly improve efficiency, reduce waste, and enhance customer satisfaction. Moreover, strong policies help a company adapt to changes in market demands, thereby optimizing its overall supply chain management.
Stock Replenishment Strategies
Stock replenishment is the methodical approach to restocking inventory to meet customer demands without delay. Two predominant strategies are often discussed: minimum order levels and just-in-time inventory.
Minimum Order Levels
Minimum order levels represent a safety net for inventory. They ensure that a business never runs too low on essential stock. Establishing minimum order levels involves determining the threshold at which new orders should be placed to avoid stockouts. This approach is particularly beneficial for businesses that deal with high-demand products, as it helps maintain customer satisfaction without incurring excessive carrying costs.
The key characteristic of minimum order levels is simple yet effective; it provides a buffer. This unique feature means that companies can adjust their purchasing patterns based on historical sales data and seasonal trends. For example, a grocery store may have a higher minimum order level for dairy products during the winter holidays, when families buy more milk for baking and gatherings.
However, one must consider the disadvantages of minimum order levels. Sticking strictly to these limits may lead to overstocking and, eventually, wasteâespecially in industries dealing with perishable goods. It's crucial to balance the levels to ensure they align with actual sales patterns.
Just-In-Time Inventory
Just-in-time (JIT) inventory management hinges on the concept of receiving goods only as they're needed in the production process. This strategy aims to reduce holding costs and increase efficiency. Businesses implementing JIT require precise coordination with suppliers to ensure that items arrive just when theyâre needed, thus avoiding excess inventory.
The critical trait of just-in-time inventory lies in its responsiveness. This strategy allows for a leaner inventory system, optimizing storage space and reducing overhead costs. The unique feature here is its l flexibility; companies can swiftly adapt to changes in consumer demand, such as launching a new product with minimal risk of unsold stock.
Nonetheless, JIT has its challenges. Reliance on timely deliveries may backfire if there are disruptions in the supply chain. If a supplier falters, businesses may face stock shortages, directly impacting sales. Therefore, while JIT offers a modern solution to inventory management, careful evaluation against potential risks is necessary.
Handling Returns and Damaged Goods
Handling returns and damaged goods is an often underestimated aspect of inventory management. Returns can stem from various reasons, such as customer dissatisfaction, damaged items, or wrong orders. Establishing policies to manage these returns efficiently is essential, not only to recover potential losses but also to maintain relationships with customers.
Another crucial element in this area is the inspection of goods returned. Damaged items might need to be disposed of, repaired, or even returned to the supplier, depending on the situation. Effective systems are needed to categorize these returned goods and decide the next best steps clearly.
Involving staff in the creation of these policies can foster ownership and ensure comprehensive procedures. Training sessions focused on handling returns and understanding the implications of damaged goods can lead to a more proficient workforce.
"An ounce of prevention is worth a pound of cure. When it comes to inventory," suggests a veteran in the retail industry.
By carefully establishing policies for handling returns and damaged goods, businesses not only secure their operational integrity but also maintain their reputation in the marketplace. Every step taken to mitigate potential losses from returns strengthens the overall inventory management strategy.
Compliance and Regulatory Considerations
In the realm of inventory management, understanding and adhering to compliance and regulatory considerations is not just a check-box task; itâs a critical pillar that can affect the very foundation of a business. Operating within the bounds of legal guidelines ensures that the business can function smoothly without the interruptions or penalties that can arise from non-compliance. The significance of these considerations canât be overstated, especially in industries where stringent regulations are part and parcel of day-to-day operations.
Compliance protects businesses from potential legal pitfalls, and fines can be hefty. The regulatory landscape is akin to a labyrinth; one wrong turn could lead to immense setbacks and loss of credibility. Moreover, possessing a thorough grasp of these regulations aids in optimizing inventory processes, reducing waste, and improving overall efficiency. Hereâs a closer look at some of the specific elements involved in compliance and the benefits that come along with a sharp focus on this area.
Understanding Industry Regulations
Every industry has its unique set of regulations that govern how inventory should be tracked, reported, and managed. For instance, the pharmaceutical industry must comply with FDA guidelines, which demand strict documentation and temperature control. Similarly, in the food sector, adhering to FDA and HACCP standards is a must to avoid food safety issues.
Organizations must stay informed regarding the specific regulations that apply to their sector. This might mean:
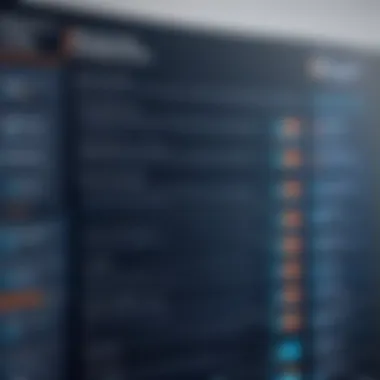
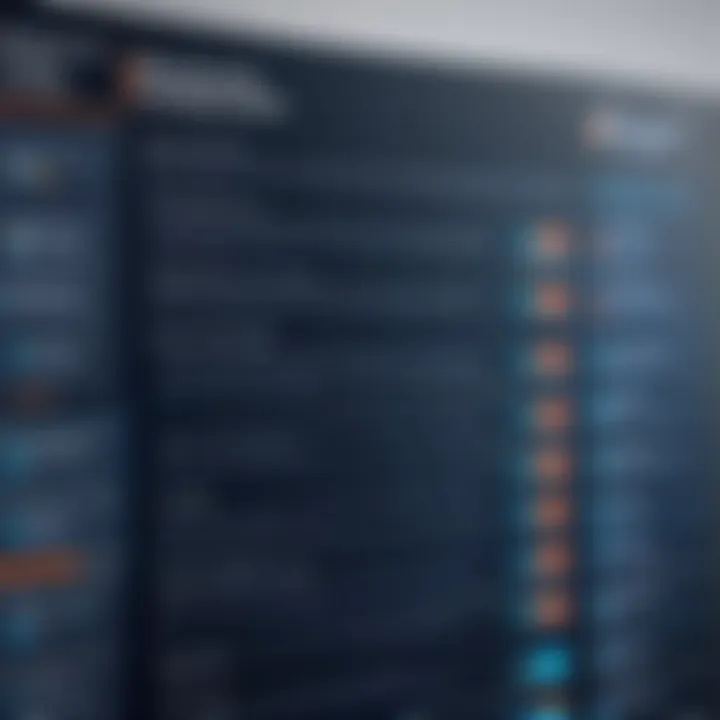
- Regularly reviewing government publications that outline relevant regulations.
- Attending industry conferences and workshops where changes to the law are discussed.
- Consulting legal experts specializing in regulatory compliance.
Ensuring adherence not just guards against financial penalties, but also enhances the brand's trustworthiness. Customers tend to favor companies that are transparent and liable in their operations. More often than not, compliance policies should not be seen as mere hurdles but viewed as opportunities for strengthening operational excellence.
Ensuring Documentation Accuracy
Documenting inventory accurately is essential for compliance. A single error in documentation can spiral into a series of issuesâoverstocking, stockouts, or even regulatory infractions. Accurate documentation serves several purposes: it helps in audits, provides insights on inventory turnover, and ensures that the company is prepared in case of regulatory scrutiny.
To bolster documentation accuracy, businesses might consider:
- Implementing robust tracking systems, such as serialized barcodes or RFID tags, which minimize human error.
- Conducting regular audits to ensure all inventory counts match with what has been documented.
- Training staff thoroughly in documentation practices to create a company-wide culture centered around accuracy.
A consistent and precise assortment of records not only fortifies compliance but also propels a company toward better decision-making based on reliable data.
"In the business world, the rear view mirror is always clearer than the windshield." - Warren Buffett.
This highlights that understanding past mistakes in documentation can inform future practices and prevent potential issues from arising.
In summary, compliance and regulatory considerations play an integral role in inventory management. By fully understanding the regulations specific to their industry and ensuring documentation accuracy, businesses can not only avoid legal repercussions but also optimize their inventory processes, enhance trust with customers, and pave the way towards sustainable growth.
Continuous Improvement
Continuous improvement plays a pivotal role in any effective inventory management system. It's not just a buzzword; itâs a mindset that organizations adopt to refine processes, increase efficiency, and adapt to changes over time. In todayâs fast-paced business landscape, standing still is akin to moving backward. Thus, organizations must constantly seek ways to enhance their inventory processes to stay relevant and competitive.
This approach can lead to numerous benefits, such as reducing waste and increasing responsiveness to market changes. By always evaluating and tweaking systems, businesses can uncover hidden issues that might hinder performance. For example, if your inventory turnover rate isn't up to snuff, it might signal problems with purchasing practices or storage inefficiencies. Regularly assessing and improving these key performance indicators can result in more informed inventory decisions.
Evaluating Performance Metrics
Inventory Turnover Rate
The inventory turnover rate is a critical metric that measures how quickly inventory is sold and replaced within a given period. It reflects the efficiency of inventory management and can inform business owners about sales performance and inventory levels. A company with a high turnover rate typically indicates that products are moving quickly off the shelves, leading to fresh inventory and reduced holding costs. Additionally, maintaining a high turnover rate signifies good inventory practices, showing that the business is aligning its supply with customer demand effectively.
However, a very high turnover rate might also raise flags regarding stock shortages or stockout situations; thus, itâs a balancing act. Businesses need to find that sweet spot where their turnover is satisfactory without risking inventory depletion. The unique advantage of focusing on this metric is that it provides a tangible way to gauge overall business performance.
Carrying Costs Analysis
Carrying costs analysis refers to the total cost of holding inventory, encompassing warehousing, insurance, shrinkage, and opportunity costs. Understanding these figures helps businesses assess whether their inventory levels are optimal. High carrying costs can reduce profit margins, making it crucial for organizations to keep these expenses in check.
A key characteristic of this analysis is that it often leads to deeper insights about cash flow and resource allocation. Companies can identify overstock situations and narrow down excessive storage costs through a diligent carrying cost evaluation.
On the downside, focusing too much on reducing carrying costs might prompt a company to cut too drastically, resulting in shortages or missed sales opportunities. Thus, a nuanced approach is essential for any inventory strategy, ensuring the balance between cost-saving and meeting customer needs is maintained.
Adapting to Changes in Demand
Adapting to changes in demand is no small feat in the world of inventory management. Market dynamics, seasonal trends, and unforeseen events can rapidly shift customer needs. Thus, companies must be responsive, employing techniques such as demand forecasting and stock level adjustments to accommodate fluctuations in consumer behavior.
Keeping an eye on market trends and customer feedback can equip businesses to make data-driven decisions. Moreover, automation and sophisticated software solutions are a game changer, allowing quick adjustments to inventory levels without cumbersome manual processes. Organizations that succeed in this area not only improve efficiency but also enhance customer satisfaction by avoiding stockouts or excessive lead times in fulfilling orders.
"In the game of inventory management, flexibility is as important as efficiency. Being able to pivot based on demand trends is crucial."
In summary, embracing continuous improvement entails an ongoing cycle of evaluating performance metrics such as inventory turnover rates and carrying cost analysis while being nimble in adapting to market changes. This holistic approach positions businesses to maintain a strong competitive edge as they navigate the complexities of inventory management.
Case Studies and Real-World Applications
Successful Implementations
Several businesses have successfully tailored their inventory systems, enabling them to thrive in their respective industries. For instance, Zara exemplifies how agile supply chain management can enhance inventory control. With a powerful insight into consumer trends, Zara maintains minimal stock levels and employs a rapid turnaround process for new collections. This approach not only reduces holding costs but also keeps their product offerings fresh and aligned with current market demands. Their success hinges on a robust tracking mechanism that integrates sales data with inventory levels, ensuring supplies are optimized while meeting ongoing customer needs.
Likewise, Amazon stands out for its sophisticated use of technology in inventory management. Leveraging AI-driven algorithms, Amazon forecasts demand, allowing for precise stocking levels. It has set up a network of fulfillment centers that elegantly manage inventory distribution. This not only reduces delivery times but also minimizes excess inventory, optimizing their overall carrying costs.
These case studies showcase a couple of different industries where thought-provoking strategies emphasize the importance of adapting inventory practices to align with business objectives and consumer behavior.
Lessons Learned from Failures
On the other side of the coin, there are also notable failures that provide equally essential lessons. Take Target's hiccup with its expansion into Canada. The company faced massive inventory problems right from the onset. Stocking issues, along with poor understanding of consumer preferences, led to empty shelves and excess inventory. Their failure to adapt to local market needs resulted in a substantial loss that forced them to retreat. This experience underscores the significance of localized knowledge in shaping inventory strategies.
Another instructive example comes from Toys "R" Us, which mismanaged its inventory during the rise of e-commerce. The company neglected to invest adequately in its online capabilities, resulting in an inability to compete with competitors like Amazon. A stretched inventory, coupled with inflexible policies, ultimately led to bankruptcy. The lesson here is clear: retailers must continuously adapt their inventory management systems to embrace digital innovations and consumer expectations.
"A wise man learns more from his enemies than a fool from his friends." - Aristotle
These lessons from failures highlight the necessity for businesses to be resilient and proactive in evaluating and modifying their inventory management systems. Such adaptability is vital for long-term success in a rapidly changing marketplace.
By closely studying both successes and shortcomings, companies can tailor their inventory strategies more effectively. The balance lies in adopting the strengths of successful implementations while learning from the drawbacks of failures. This reflexive approach can lead to a more grounded understanding of inventory management principles and their diverse applications.
The End and Future Directions
A well-structured inventory management system does not merely serve as a repository for goods; it acts as the backbone of a businessâs operational efficiency. As organizations increasingly look to optimize their processes, embracing the conclusions derived from effective inventory management becomes paramount. The future holds an array of opportunities, particularly when businesses adapt to evolving consumer behaviors and technological advancements.
Summarizing the key takeaways helps ensure that the core principles of managing inventory are not lost in the shuffle. Each element discussed within this article has laid out a clear path toward making informed decisions on objectives, software selection, tracking methods, and compliance, ultimately driving profitability. The focus should always remain on aligning inventory practices with broader business goals.
Looking ahead, organizations must remain vigilant about emerging trends in inventory management. These trends not only reflect the changing landscape but also influence how businesses can fine-tune their operations moving forward. Letâs delve into some of these emerging trends.
Summarizing Key Takeaways
- Clear Objectives â Define what inventory management means for your organization and how it aligns with overall business strategies.
- Technology Utilization â Invest in the right software tools that can enhance your tracking capabilities while providing insightful reporting features.
- Regulatory Compliance â Ensure that all management practices meet regulatory standards to avoid potential legal conflicts.
- Continuous Improvement â Establish metrics for performance evaluation and adapt to changing market conditions as necessary.
Emerging Trends in Inventory Management
Technology Integration
The area of technology integration is becoming a significant driving force behind effective inventory management. Systems are now capable of linking real-time data from various sources, leading to faster decision-making processes. A crucial characteristic of technology integration is its ability to bring together information from different operational channels. With this consolidated view, businesses can anticipate stock needs, thereby dramatically reducing the likelihood of stockouts or excess inventory.
A notable feature is how predictive analytics works with past consumption dataâguiding businesses to adjust stock levels based on historical trends. However, while the advantages of accuracy and efficiency in inventory management through technology are evident, the initial learning curve and potential costs associated with implementation are considerations that should not be ignored.
Sustainability Considerations
In recent years, sustainability has carved a niche in inventory management strategies, emphasizing the importance of eco-friendly practices. Companies are increasingly recognizing the significance of sustainable stocking processes and examining their entire supply chain for environmental impact. As a key characteristic, sustainability leads to a more responsible inventory approach that not only meets market demand but also addresses the company's social responsibility.
A unique aspect of sustainability in this context involves waste reduction in both materials and processes. For instance, implementing just-in-time inventory methods minimizes excess stock, significantly cutting down on waste. While the initial investment in sustainable practices may appear daunting, the long-term benefits often outweigh these costs, especially as consumers lean more towards brands with eco-conscious reputations.
Quotes like the following resonate deeply with the ongoing shift:
"The concept of sustainable inventory management is not merely a trend; it's a fundamental shift towards responsible business practices that guarantee future success."