Enhancing Efficiency in Inventory Location Systems

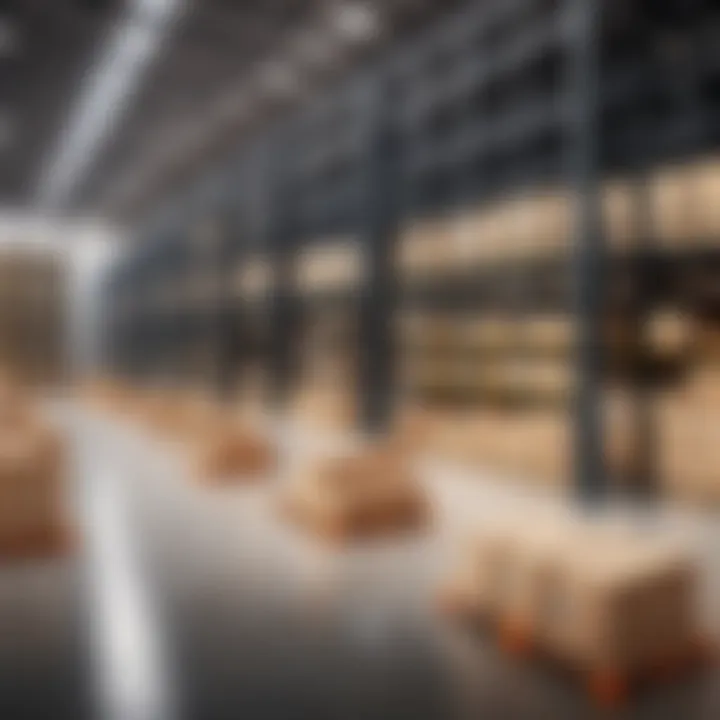
Intro
The dynamics of modern logistics depend heavily on how inventory is organized and retrieved. With the complexities rising as e-commerce grows at an impressive rate, having a savvy strategy for inventory location is no longer just a preference, but a necessity. Businesses that can seamlessly blend technology and methodology stand to gain a significant edge, minimizing errors and maximizing efficiency.
Effective inventory management is essentially the backbone of supply chain operations. A well-optimized inventory location system can drastically cut down on lead times and enhance overall productivity. This not only involves understanding the nitty-gritty of inventory but also leveraging the right technologies to keep things streamlined.
The following sections will unravel the core elements that constitute a robust inventory location system. We will further explore features that are indispensable, how technology intertwines with these systems, and the user experience factors that ensure everyone can easily navigate through the complexities of inventory management.
Understanding Inventory Location Systems
Inventory location systems are the backbone of any effective supply chain management strategy. They orchestrate the journey of products from supplier to customer, ensuring that items are stored in optimal positions for easy access and retrieval. A well-understood inventory location system can significantly enhance operational efficacy, reduce costs, and improve service levels.
Definition and Purpose
At its core, an inventory location system defines where goods are stored within a warehouse or storage facility. These systems are not just about physical placement but also involve methods and technologies that facilitate optimal inventory flow. The primary purpose is to streamline operations, accommodating swift order fulfillment while minimizing excess storage costs. By ensuring that fast-moving items are closer to the shipping areas, companies can cut down on time spent retrieving products, fostering agility in response to market demands.
Additionally, having a robust inventory location system provides clear visibility into stock levels and locations. This is crucial for businesses that aim to make data-driven decisions regarding purchasing and restocking. Efficient systems also mitigate human error, which can be a costly pitfall in manual processes.
Key Components
Understanding the components of an inventory location system brings clarity to its effectiveness. Here are some pivotal elements:
- Storage Methodology: This includes methods like pallet racking, shelving, or bins, which need to be aligned with the product types.
- Technology Integration: Modern systems integrate software solutions such as Warehouse Management Systems (WMS) that allow for real-time tracking of inventory.
- Categorization Strategies: Utilizing classification techniques such as FIFO (First In First Out) ensures that older stock is sold before newer items, reducing waste and expiration risks.
- Location Mapping: This involves creating a visual layout of the warehouse that easily identifies where items are stored, reducing the time spent locating products.
Understanding these components enables organizations to tailor their inventory management processes, enhancing responsiveness and efficacy in meeting customer demands. The collective integration of these elements cultivates a harmonized system that supports strategic goals.
Significance of Efficient Inventory Management
Efficient inventory management is more than just a buzzword thrown around in boardrooms. It’s the backbone of any organization that wants to thrive amidst competition and fluctuating market demands. When businesses take a serious approach to how they manage their inventory, they see not just immediate benefits but long-term sustainability and growth.
Optimizing inventory management is all about aligning the intricacies of stock management with the broader business objectives. It involves understanding how to balance supply and demand effectively, ensuring that products are available when customers need them, without tying up capital in excess stock. This delicate dance can mean the difference between thriving and merely surviving.
Cost Reduction Strategies
Adopting effective cost reduction strategies is one of the paramount benefits of efficient inventory management. Here are some key strategies:
- Just-In-Time (JIT) Inventory: This approach focuses on receiving goods only as they are needed in the production process, which minimizes waste and holding costs.
- Consolidation of Orders: Combining multiple smaller orders into one larger one can significantly reduce shipping costs, not to mention save time.
- Inventory Optimization Software: Utilizing software to predict demand and optimize stock levels can help in minimizing overstock and stockouts.
- Supplier Negotiations: Sourcing materials from suppliers offering discounts for larger orders can also assist in controlling costs.
- Inventory Audits: Regular audits allow for the detection of slow-moving or obsolete stock, making space for more profitable inventory.
Impact on Customer Satisfaction
The correlation between inventory management and customer satisfaction can hardly be overstated. A well-managed inventory ensures that customers can find what they need when they need it. Here are some ways it impacts satisfaction:
- Availability of Products: Customers appreciate having products available at their fingertips. Efficient management avoids frustrating situations where items are out of stock.
- Faster Delivery Times: When inventory is organized effectively, shipping and handling processes improve, leading to quicker turnaround times on orders.
- Responsive to Market Trends: With a system that keeps track of demand patterns, businesses can adjust their inventory levels in real time, capturing sales before competitors do.
- Enhanced Reputation: A company known for its reliability is more likely to secure repeat customers.
“Inventory management is not just about stock levels. It’s a strategic component that drives the overall customer experience.”
The continuous improvement of inventory systems directly affects how an organization interacts with its customers. It's not only about servicing the current clientele but also creating a positive impression that attracts new customers.
In summary, efficient inventory management is indispensable for reducing costs and enhancing customer satisfaction. By prioritizing these aspects, businesses pave the way for increased competitiveness and sustainable growth in a complicated market environment.
Types of Inventory Location Systems
Understanding the various types of inventory location systems is crucial to achieving a balanced and efficient inventory management practice. Each type caters to distinct operational needs, thereby impacting overall productivity and effectiveness. By tailoring the approach to the specifics of their operation, companies can enhance their material flow and reduce waste. Below, we delve into the three major types of inventory location systems, shedding light on their unique characteristics, advantages, and potential limitations.
Static Inventory Systems
Static inventory systems are akin to an immovable wall; items are kept in fixed locations within the warehouse irrespective of changes in demand or stock levels. This method can be particularly advantageous when dealing with products that have a consistent sales pattern, like office supplies or bulk raw materials. The systematic arrangement allows for improved inventory accuracy, since the items are always in the same place.
Benefits of static systems include:
- Simplicity: Easy to set up and manage.
- Accuracy: Inventory counts can be quite straightforward, reducing discrepancies.
- Reduced Training: New staff can be brought up to speed quickly, as the layout should remain unchanged.
However, there are considerations. If demand fluctuates greatly, one could end up with a crowded area filled with slow-moving products while fast-sellers are tucked away out of reach. This inefficiency can lead to delays and reduced customer satisfaction. In essence, while static systems provide order, flexibility is a price paid for that stability.
Dynamic Inventory Systems
Dynamic inventory systems thrive on flexibility, adapting the placement of goods in response to changing demand and sales patterns. These systems can rearrange items based on factors like sales frequency, seasonality, and product life cycles. For example, a retailer during the holiday season might place toys closer to shipping areas as demand spikes.
Advantages of dynamic systems encompass:
- Optimized Space Utilization: Warehouse space maximizes by placing fast-moving items in accessible locations.
- Better Responsiveness: The system can quickly adjust to changes in demand, improving customer service levels.
- Enhanced Picking Efficiency: With fast-sellers close at hand, order picking times shorten significantly, leading to quicker fulfillment.
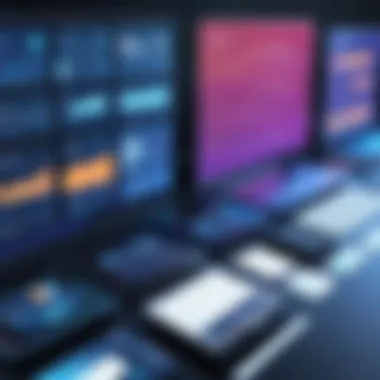
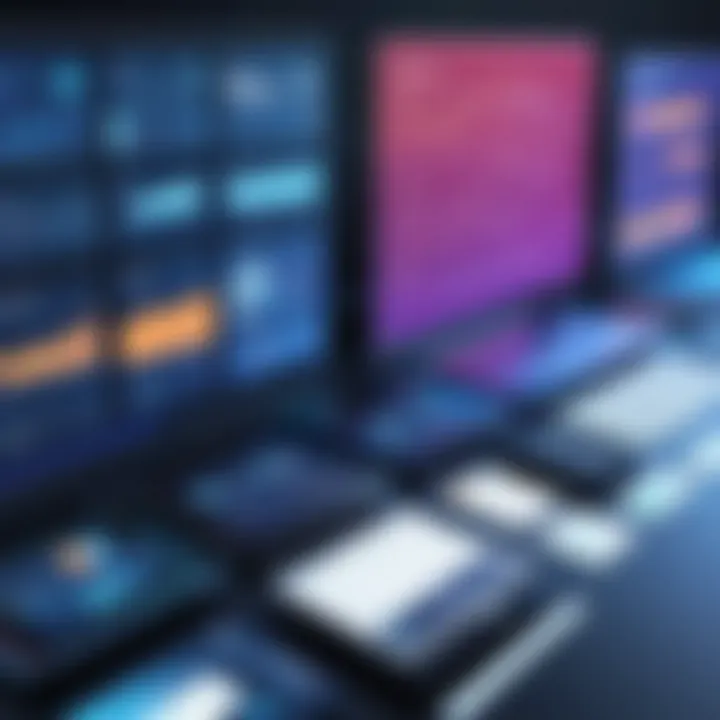
However, these systems often require sophisticated software and a more trained workforce to manage operations. The potential for error increases with complexity, particularly if staff aren't adequately trained. Nevertheless, the upsides often far outweigh these points, especially in industries subject to quick market changes.
ABC Inventory Analysis
ABC Inventory Analysis, named akin to the way one learns the alphabet, categorizes inventory into three distinct groups (A, B, and C) based on their importance. Group A includes high-value items with low frequency of sales, while Group C consists of low-value items with high frequency. Items in Group B fall in between both categories. This methodology allows teams to allocate resources efficiently by focusing the most attention on the items that truly impact the bottom line.
Key advantages of ABC analysis include:
- Resource Allocation: Enables businesses to prioritize time and effort on critical inventory.
- Cost Control: Helps in identifying opportunities for savings, as unnecessary stock can be minimized.
- Informed Decisions: Facilitates more educated purchasing and stocking strategies.
Despite its strengths, businesses must diligently monitor inventory. If not managed properly, the method could lead to overstocking Group A items and underestimating the demand for Group C. However, with proper analysis and regular audits, ABC can lead to sharper business decisions and profitability.
In summary, the choice of inventory location systems—be it static, dynamic, or through ABC analysis—offers distinct benefits while also presenting certain challenges. Successful inventory management doesn’t hinge on just picking one but on aligning the system’s characteristics with the needs of the business, all the while being adaptable in response to market shifts.
Factors Influencing Inventory Location Decisions
The decisions around where to store inventory are not just routine choices; they play a pivotal role in the throughput and overall efficiency of an organization. Often, the success of inventory management hinges on several key factors that must be evaluated diligently. These decisions impact costs, service levels, and even customer satisfaction. Not a trivial matter by any means. Let's delve into the specific components that shape these decisions.
Product Characteristics
Understanding product characteristics is essential in determining optimal storage locations. Each product has its own unique attributes – size, weight, shelf life, and demand variability. For instance, bulky items often necessitate different handling than small parts. Perishables like dairy or produce require fast-moving locations closer to dispatch areas to minimize spoilage, whereas non-perishables can be stored away from shipping points.
Moreover, products with high inventory turnover should ideally be stored near packing or loading areas to streamline the picking process. In contrast, seasonal items might find more cost-effective storage at a distance until they're needed.
When making these choices, businesses can consider:
- Size and Shape: Are they large and unwieldy, or small and stackable?
- Weight: Heavy items might need reinforced shelves or dedicated pallet spaces.
- Demand Discrepancies: Understanding if certain items sell like hotcakes compared to the ones that are hardly touched.
This assessment aids not only in optimizing space but also in ensuring safety and efficiency in warehouse operations.
Demand Forecasting
Getting a grip on demand forecasting is like having your crystal ball. Accurate demand predictions help logistics managers to allocate inventory in ways that meet customer needs without tying up capital in overstock. Implementing analytical models and historical data assessments helps in predicting which items will sell and which ones won’t.
For example, if a retailer knows that winter gear is going to be in high demand during the fall months, they can preemptively stock that section of the warehouse and ensure it’s front and center, ready to go when the chill sets in. On the flip side, inaccurate forecasts can lead to either over-stocking or under-stocking, which can cause significant financial strain and can ultimately frustrate customers when they can’t find what they need.
Key techniques to enhance prediction accuracy include:
- Seasonal Adjustments: Modifying predictions based on trends from previous years.
- Market Research: Staying attuned to market trends and consumer behavior.
- Collaboration with Sales Teams: Insights from those on the front lines can inform stock allocations more effectively.
Warehouse Layout
A warehouse's layout isn't just about arranging shelves and bins. It's a comprehensive strategic approach that directly affects picking efficiency, order fulfillment times, and overall labor costs. The layout should allow for swift access to high-demand products while enabling low-traffic items to be shelved in less accessible areas.
Designing an optimal layout includes:
- Zoning: Devise zones for different product types or temperatures, separating fast-moving from slow-moving stock.
- Flow: Consider designing a logical flow that allows easy movement through the warehouse, minimizing travel time for staff.
- Accessibility: Items that require more frequent picking should be placed at easy-to-reach locations.
"A well-thought-out layout can reduce wasted movements and streamline the logistics chain, impacting everything from labor costs to customer satisfaction."
Technological Integration in Inventory Location Systems
In today’s fast-paced market, technological integration has emerged as a cornerstone for effective inventory location systems. Integrating advanced technologies not only enhances productivity but also paves the way for more agile operations. This segment will take a closer look at various technological components that are essential in enhancing inventory management efficiency, touching on their respective benefits and the need for thoughtful implementation.
Warehouse Management Systems (WMS)
A Warehouse Management System serves as the nerve center for managing inventory housed in warehouses. By leveraging WMS software, businesses can streamline the process of receiving, storing, and shipping products. This means fewer mistakes and faster turnaround times.
The functionalities of a WMS may include:
- Inventory Tracking: Keeps tabs on stock levels in real-time, ensuring that supplies align with demand.
- Order Fulfillment: Automates the picking and packing process, reducing labor costs and enhancing speed.
Moreover, a WMS reduces human error significantly. By automating repetitive tasks, employees can focus on more strategic aspects of the operation. A small retailer might discover that their selection of a robust WMS can elevate their service levels and cut operational costs, thereby competing more effectively with larger rivals.
Barcode and RFID Technologies
Another game-changer in the realm of inventory management is the adoption of barcode and RFID technologies. Both tools help track items efficiently.
- Barcodes are still widely used because they are cost-effective and easy to implement. Scanning a barcode can provide instant access to essential product information, making inventory counts quicker and more precise.
- Radio Frequency Identification (RFID) takes it a notch higher. With RFID, goods can be scanned from a distance and multiple items can be tracked simultaneously.
"Employing RFID is like having an air traffic controller for your inventory—everything can be monitored without the need for physical checks."
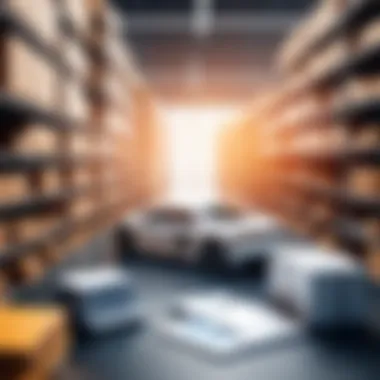
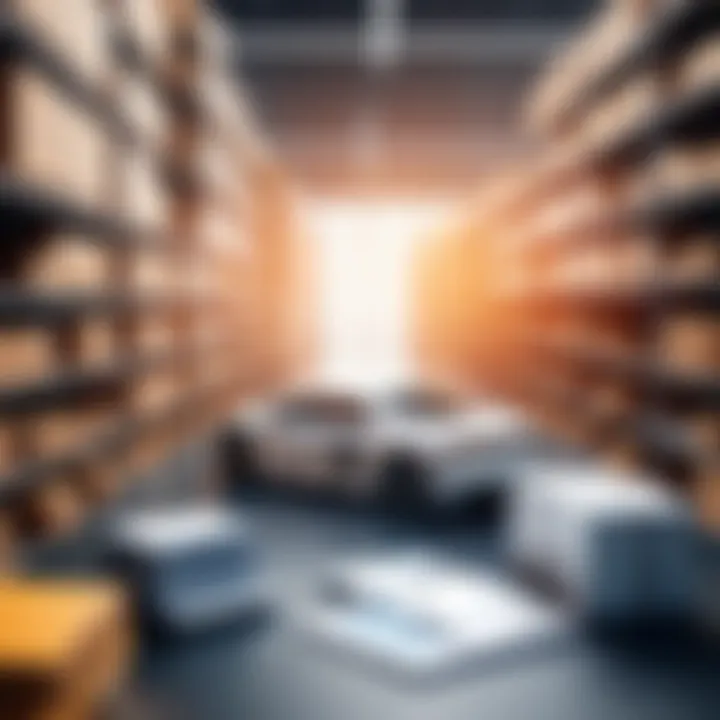
The incorporation of these technologies not only speeds up inventory management tasks but also provides better visibility into the stock, important for making informed decisions.
Artificial Intelligence and Machine Learning
The frontier of inventory location systems is truly being reshaped by Artificial Intelligence (AI) and Machine Learning (ML). Both tools enable businesses to analyze vast amounts of data effectively and recognize patterns that a human eye might miss.
The advantages of leveraging AI and ML include:
- Predictive Analytics: Anticipate inventory needs based on historical data and trends, thus optimizing stock levels.
- Automated Replenishment: Systems can automatically reorder stock when levels dip below a predetermined threshold, preventing stockouts or overstocking.
- Enhanced Decision-Making: Real-time data analysis allows decision-makers to stay ahead of demand fluctuations, thereby boosting customer satisfaction by ensuring product availability.
AI can also categorize products into different clusters based on various factors such as turnover rates. This allows businesses to position fast-moving goods closer to shipping areas while slower-moving items can be stored further away, optimizing the entire warehouse layout effectively.
In summary, as technology rapidly evolves, the savvy integration of these various tools can significantly transform how businesses manage inventory. By adopting a proactive approach to technological integration, organizations not only enhance operational efficiency but also prepare themselves for future challenges in inventory management.
Strategic Approaches to Optimize Inventory Locations
In the realm of logistics, the effectiveness of inventory location systems cannot be underestimated. Strategic approaches to optimizing these systems can lead to significant advantages such as minimizing operational costs and enhancing customer service. Companies, both large and small, should actively pursue methods to refine their inventory strategies. This will not only streamline their operations but also align more closely with industry best practices.
The implementation of these strategic approaches is essential for a few key reasons. First off, regularly auditing and assessing inventory locations ensures that the system adapts to changing demands and patterns. Additionally, fostering a culture of continuous improvement encourages teams to remain vigilant against inefficiencies and waste. Finally, investing in employee training and involvement cultivates a knowledgeable workforce that is engaged and motivated to drive performance metrics forward.
Regular Audits and Assessments
Conducting regular audits and assessments is pivotal in realizing the full benefits of any inventory location system. Picture this: a grocery store keeps a detailed log on which items frequently fly off the shelves but neglects to update its storage layout accordingly. Over time, this will cause delays in restocking popular products and, ultimately, customer dissatisfaction.
A systematic audit schedule allows decision-makers to identify discrepancies in the inventory management process, evaluate storage capacities, and even forecast demand more accurately. By deploying analytical tools and metrics during these audits, businesses can uncover trends pointing to areas needing improvement. Here are some common practices to consider:
- Assess turnover rates of different items.
- Check the accuracy of inventory records against physical counts.
- Evaluate the effectiveness of storage solutions and layout.
Regular assessments help in making informed decisions, ensuring resources are used efficiently, and laying a robust foundation for strategic shifts if needed.
Continuous Improvement Methodologies
Implementing a continuous improvement methodology can revolutionize inventory location systems. It's akin to adopting a philosophy of never settling for “good enough.” Lean management and Six Sigma are two popular strategies that stress on scrutinizing every aspect of the inventory process.
For instance, organizations utilizing lean techniques may find ways to eliminate waste by optimizing the pathways to retrieve items. Conversely, Six Sigma focuses on minimizing errors in each step of inventory management. Continuous improvement isn’t just about finding fixes; it's about creating a culture where every team member feels accountable and empowered to suggest enhancements.
Benefits of integrating continuous improvement methodologies include:
- Enhanced accuracy in inventory tracking.
- Increased operational efficiency across warehouse activities.
- Better alignment of supply chain processes with demand.
Giving employees the tools to continuously pursue improvements instills a sense of shared purpose, driving engagement and performance cohesively.
Employee Training and Involvement
No strategy is complete without the human element. Investing in regular employee training is essential for ensuring that everyone is on the same page regarding inventory procedures and technologies. Imagine a warehouse filled with state-of-the-art technology where workers aren’t trained properly; those fancy systems become little more than expensive paperweights.
Training programs should focus on:
- Familiarizing staff with technologies like WMS and RFID systems.
- Providing practical scenarios for managing workflow during busy periods.
- Encouraging teamwork and collaboration across departments.
Moreover, involving employees in inventory management discussions can be a game-changer. Their firsthand experiences often provide unique insights into existing pain points. It’s not just about filling a training log; it’s about giving team members a voice in how their workspace operates. When employees are engaged, the enthusiasm shows in their work, resulting in better handling of inventory systems and ultimately, more satisfied customers.
In summary, optimizing inventory locations requires a comprehensive approach that encompasses regular audits, continuous improvement, and a focus on employee training. Together, these strategies foster an environment where efficiency thrives, setting the stage for operational excellence.
Challenges in Implementing Inventory Location Systems
Implementing inventory location systems is akin to walking a tightrope. It requires a delicate balance between operational efficiency and technological integration. As companies strive to optimize their warehousing processes, they face a multitude of challenges that can hinder these initiatives. Understanding these challenges is not just essential for aligning with best practices but also crucial for securing a competitive edge in the market. An effective inventory program can only be as strong as its weakest link. Let’s delve into specific issues that organizations must consider.
Data Quality and Accuracy Issues
In the age of information, data is undoubtedly king. However, when it comes to inventory location systems, the quality and accuracy of this data often fall short. Systems rely heavily on data inputs to function properly—be it item descriptions, quantities, or location codes. If this data is flawed, the entire inventory operation could spiral out of control.
For instance, incorrect SKU numbers can lead to misplaced items, causing inefficiencies and dissatisfaction among customers. Moreover, businesses may experience excess inventory or stockouts, impacting cash flow and operational costs. The old adage "garbage in, garbage out" rings true here—investing in robust data management processes is vital.
A few key considerations for tackling data quality include:
- Implementing automatic data capture technologies.
- Conducting regular data audits to validate information accuracy.
- Providing training programs to employees on accurate data entry practices.
System Integration Challenges
Integrating inventory location systems with existing warehouse management systems (WMS) poses yet another significant hurdle. Compatibility issues may arise among various software applications that need to work seamlessly. Organizations can often find themselves in a tangled mess where systems refuse to communicate effectively.
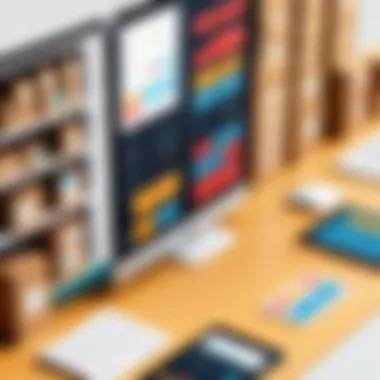
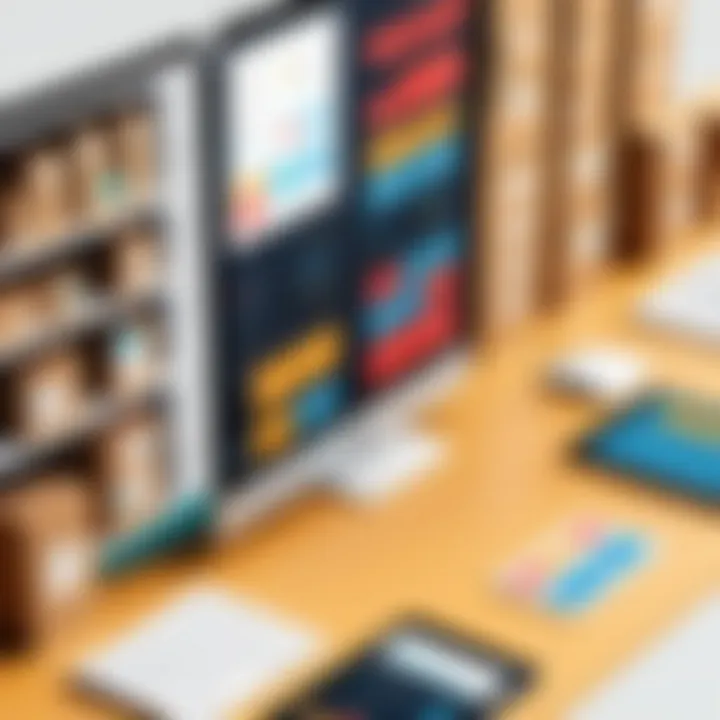
The challenge is twofold: on one side, you have the technology—software updates, integration APIs, and legacy systems that could throw a wrench in the works. On the flip side, there’s the matter of people—stakeholders must embrace new tools and processes. Without proper integration, the potential benefits of an optimized inventory location systems cannot be fully realized.
To mitigate these roadblocks, businesses can:
- Invest in modular solutions that allow for easier integration.
- Foster strong collaboration among IT teams and operational staff.
- Conduct testing phases before full-scale implementation.
Change Management Resistance
When it comes to change, resistance is common; it’s human nature. Change management plays a crucial role in the successful implementation of inventory location systems. Employees may feel threatened by new processes and worry about job security, which can lead to pushback. Successful inventory management isn't just a tech issue—it’s about people.
Effective change management involves clear communication and strategic planning. Companies must ensure that stakeholders understand the benefits of a new inventory system, not just for the organization but also for their daily operations. Transparency builds trust, and trust fosters acceptance.
Some beneficial strategies include:
- Creating communication channels for feedback during the implementation phase.
- Offering training sessions to increase familiarity and comfort.
- Highlighting success stories from other companies that thrived after such changes.
"An organization’s workforce is its most valuable asset; ignoring their behavioral responses can lead to failure."
Case Studies: Successful Inventory Location Implementations
Analyzing real-world examples of effective inventory location implementations provides invaluable insights into best practices and the tangible benefits businesses can achieve. Case studies serve as a roadmap, showcasing how certain strategies can be effectively adopted and tailored to specific industry needs. Not only do they highlight successes, but they also delve into the trials and lessons learned in the pursuit of optimizing inventory systems. This section aims to present case studies from both the retail and manufacturing sectors, illustrating the diverse approaches of inventory location optimization.
Retail Industry Examples
In the retail world, having the right product at the right place at the right time is paramount. Let’s look at Walmart, one of the most recognized names in retail. Walmart implemented a system focusing heavily on real-time inventory tracking. Utilizing advanced Warehouse Management Systems (WMS) integrated with their supply chain operations, Walmart can streamline inventory flows. They employ a centralized database that updates stock levels instantly as customers make purchases online and in stores.
This agile inventory system allows Walmart to reduce excess stock in warehouses while ensuring popular items are readily available to meet consumer demand. Consequently, this has not only improved stock turnover rates but has also enhanced customer satisfaction.
A notable insight from Walmart’s case is the importance of data-driven decision-making. Data analytics enabled Walmart to predict trends and seasonal demands more effectively, helping to hinder stockouts or overstock scenarios.
Manufacturing Sector Insights
In the realm of manufacturing, consider the case of Toyota. Renowned for its Lean Manufacturing principles, Toyota applies stringent inventory location strategies to maintain efficiency. They adopted the Just-in-Time (JIT) inventory approach, which minimizes waste by keeping only the necessary stock on hand. By mapping inventory locations directly related to production flow, Toyota ensures that parts are precisely where needed, when they’re needed.
An essential aspect of Toyota’s success in this area is the Kanban system, which facilitates real-time ordering and stock management. This visual system enhances communication between teams, ensuring that suppliers are notified when components need replenishing. As a result, Toyota has been able to maintain production without excess inventory, thus reducing carrying costs significantly.
Finale
These case studies illuminate how tailored inventory location systems lead to substantial efficiency gains in both retail and manufacturing sectors. They spotlight critical strategies such as data-driven decision-making and real-time tracking, showcasing the profound impact of technology and methodology on inventory management effectiveness. By learning from these examples, businesses can forge a path toward enhanced operational efficiency and greater customer satisfaction.
Future Trends in Inventory Location Systems
The landscape of inventory management is constantly evolving, shaped by notable advancements in technology and shifting consumer demands. As businesses seek to cut costs and maximize efficiency, understanding future trends in inventory location systems proves essential. These developments are not merely fads but transformative forces meant to streamline operations while ensuring responsiveness to market fluctuations. Companies that adapt to these trends are better positioned to enhance their competitive advantage.
Increased Automation
Automation is fundamentally reshaping inventory management. When we talk about increased automation, we're referring to systems that minimize human intervention, thereby improving speed and accuracy. Automated solutions, like robotic pickers and conveyor belts, allow for faster processing in warehouses, reducing the time it takes to fulfill orders. Consider a scenario where a large online retailer implements robotic arms that can sort and package products with minimal human interaction. This leads to a significant decline in errors, ultimately improving customer satisfaction.
Key benefits of embracing automation in inventory locations include:
- Reduced Labor Costs: Automation potentially lowers labor expenses as fewer employees are needed for manual tasks.
- Enhanced Accuracy: Machines operate with precision, significantly lowering the risk of picking errors; hence inventory discrepancies decrease.
- Scalability: Automated systems can be adjusted more easily to accommodate changes in demand or inventory size, providing greater flexibility for businesses.
Furthermore, the use of software with advanced algorithms allows companies to optimize inventory layout based on real-time data. This responsiveness helps in minimizing the time resources spend in warehouses and streamlining logistical processes.
"The choice to automate is not just about cost-cutting; it's about future-proofing your operational efficiency."
Sustainability and Green Practices
Another significant trend we see is the drive towards sustainability within inventory management. As businesses become more aware of their environmental impact, the focus shifts to implementing green practices in operations. Sustainable practices not only help to mitigate environmental impacts but also appeal to a growing segment of eco-conscious consumers.
Adopting green initiatives in inventory location systems can take several forms:
- Energy-efficient Warehousing: Utilizing renewable energy sources or optimizing energy use in warehouses can reduce operational costs while lowering carbon footprints.
- Eco-friendly Packaging: Many companies are now sourcing sustainable packaging materials that reduce waste, aligning business practices with environmental responsibility.
- Waste Reduction Programs: Initiatives aimed at minimizing waste at every stage of the supply chain can enhance efficiency and build a positive corporate image.
For example, one notable fashion retailer has overhauled its supply chain by minimizing excess production and focusing on products with sustainable materials. This strategic shift has not only reduced waste but has also aligned the brand with modern consumer values.
Epilogue
In the maze of modern logistics, the role of optimized inventory location systems cannot be overstated. This article sheds light on various aspects that contribute to the overall effectiveness of such systems. The critical takeaway is that organizations must not only focus on efficiency but also on integrating technological advancements that simplify these processes. Understanding the significance of mapping inventory accurately leads to lower operational costs and faster turnaround times, which directly enhances customer satisfaction.
Summarizing Key Points
- Understanding the Systems: Clear definitions of inventory location systems and their inherent components help frame the discussion. It builds a foundation where readers can relate practical applications to theoretical principles.
- Impact on Customer Relationships: Efficient inventory management reduces costs while improving service levels. A well-optimized location system translates to better stock availability, which keeps customers happy and returning.
- Technology's Role: The thrust on technological integration lays out how tools like Warehouse Management Systems, Barcode, and RFID technologies elevate operational capabilities.
- Challenges and Strategic Responses: Acknowledging obstacles like system integration issues and data inaccuracies prepares businesses for realistic improvements. The article transitions smoothly into suggesting regular assessments and employee involvement as key strategies to overcome these hurdles.
Final Thoughts on Optimization
Optimizing inventory location systems is not a one-size-fits-all approach; it's a tailored process that requires ongoing attention. Businesses must stay attuned to shifting consumer demand and the evolving landscape of technology. The continuous refinement of inventory systems through data analysis and performance audits ensures they remain aligned with strategic business goals. Moreover, fostering an agile mindset within teams helps in swiftly adapting to changes without hesitation. Investing time and effort in optimizing inventory locations today lays a crucial stepping stone toward sustaining success in an increasingly competitive market.