Comprehensive Guide to Equipment Maintenance Apps
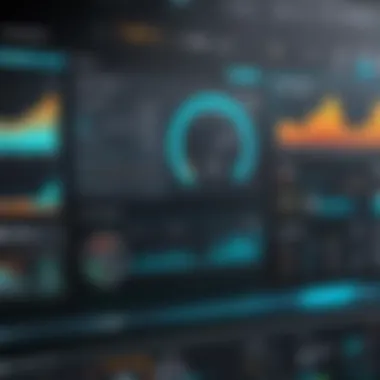
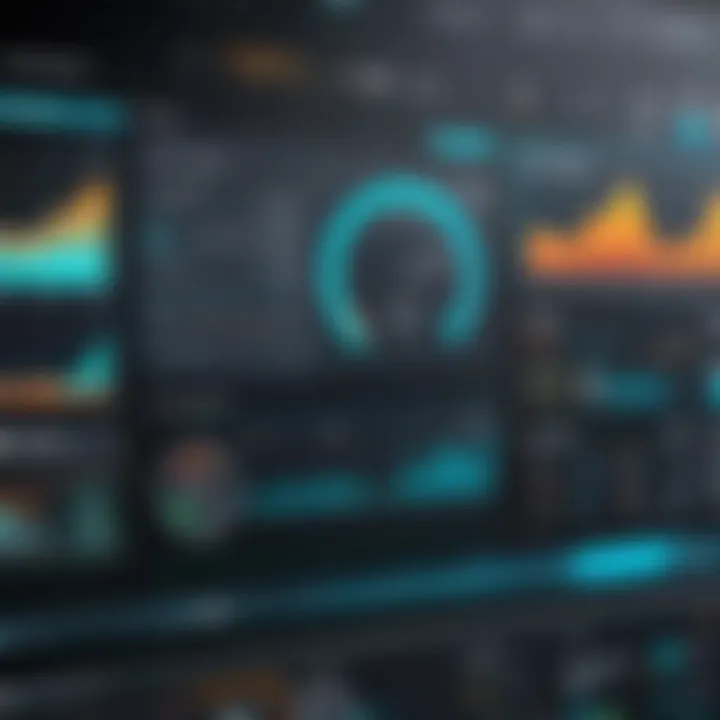
Intro
In the fast-paced world of machinery management, the need for an organized approach to equipment upkeep cannot be overstated. Equipment maintenance tracking apps have emerged as crucial tools that empower businesses, ranging from small startups to large industrial operations, to streamline their maintenance processes effectively. These apps provide a structured way to monitor the health of equipment, ensuring longevity and enhancing productivity.
In this article, we will delve into an in-depth analysis of these applications, highlighting essential functionalities, exploring key features, and discussing the overall benefits they bring to organizations. Furthermore, we will evaluate the user experience as a critical element in adopting and utilizing these technologies. Let’s not waste any more time and get straight to it.
Understanding Equipment Maintenance
In the realm of business and industry, understanding equipment maintenance is a cornerstone of operational success. Without effective maintenance practices, organizations can quickly find themselves knee-deep in unplanned downtime, sudden repair costs, and a slew of inefficiencies that ripple through production lines. This section aims to unpack the significance of maintaining equipment in a methodical way, allowing businesses to see not just the why but the how of maintenance strategies.
The Importance of Equipment Maintenance
Equipment maintenance is crucial for any organization that relies on machinery or technical systems to function effectively. One of the primary reasons to prioritize maintenance is to ensure the longevity of equipment. Regular maintenance checks can catch small problems before they morph into significant issues that may require extensive repairs or replacements. Essentially, it’s like an insurance policy for your machines.
Consider this: a manufacturing facility that does not invest in maintenance could see its machinery break down unexpectedly. This leads to costly outages and lost production time. Therefore, maintaining equipment keeps operational processes smooth, reduces waste, and safeguards profit margins.
"An ounce of prevention is worth a pound of cure."
This age-old proverb highlights that taking proactive steps is always better than reactive measures. From a safety perspective, poorly maintained equipment can pose significant dangers. If machinery fails, it can lead to hazardous working conditions, putting employees at risk. Thus, a robust maintenance strategy not only aids efficiency but also enhances workplace safety.
Types of Equipment Maintenance
Diving deeper into equipment maintenance, it's important to differentiate between various types of maintenance strategies that organizations can employ. Each type has distinct characteristics, advantages, and possible drawbacks, but when utilized correctly, they significantly contribute to an overarching maintenance plan. Here are the three main types:
Preventive Maintenance
Preventive maintenance focuses on regular, planned maintenance tasks performed while equipment is still functioning well. This type of maintenance aims to prevent unexpected failures. By conducting routine inspections and replacements — like changing filters or lubricating parts — businesses can ensure their machinery operates smoothly and does not suffer from premature breakdowns.
The key characteristic of preventive maintenance is its scheduled nature, which allows companies to plan for maintenance activities during less productive periods, minimizing operational disruptions. This predictability makes it a popular choice for many industries, especially manufacturing, where maintaining production flow is critical.
However, while preventive maintenance is often cost-effective, it does require a commitment to regular intervals of upkeep and can sometimes lead to unneeded service if not tailored correctly to the specific equipment.
Corrective Maintenance
Corrective maintenance, on the other hand, is conducted after a piece of equipment fails. Essentially, it involves identifying and fixing a problem once it occurs. This type of maintenance is reactive by nature and often comes as a response to the equipment breakdown.
The primary characteristic of corrective maintenance is its timing; it's not scheduled but rather executed as needed. This may appeal to organizations looking to cut costs on maintenance and repair, as it allows resources to be allocated only when failures happen.
However, relying solely on corrective maintenance can be a slippery slope. It often leads to increased equipment downtime, which translates to loss of revenue and productivity. Furthermore, repeated failures can escalate into larger issues, creating a vicious cycle of reactive repairs.
Predictive Maintenance
Predictive maintenance employs data analysis tools to predict when equipment failures might occur. By leveraging metrics and sensor data, organizations can determine the optimal time for maintenance before issues arise.
This type of maintenance stands out due to its ability to reduce unnecessary maintenance actions, focusing only on the items that genuinely need attention at that specific time. Predictive maintenance is efficient; it relies on real-time monitoring which ultimately can lead to lower long-term costs and fewer unexpected breakdowns in machinery.
However, implementing predictive maintenance often necessitates a shift in mindset and operational procedures. Companies must invest in technology and training, making it a more significant commitment than its counterparts.
Understanding these maintenance types sets the groundwork for developing a complete maintenance tracking strategy. By recognizing the unique aspects of preventive, corrective, and predictive maintenance, decision-makers can better align their maintenance tracking applications to their specific needs and operational goals.
What is an Equipment Maintenance Tracking App?
Equipment Maintenance Tracking Apps, often referred to as maintenance management software, are digital solutions designed to streamline the process of tracking maintenance activities for various types of equipment. Their significance cannot be overstated. A strong maintenance tracking app is like a lifebuoy for organizations navigating the often turbulent waters of equipment upkeep and management.
Definition and Functionality
At its core, an Equipment Maintenance Tracking App serves a clear purpose: to monitor, manage, and optimize the maintenance of equipment. This includes systematically recording maintenance schedules, repairs, and operational details. These applications provide a unified platform where teams can access crucial information about machinery status at any given moment. The functionalities vary, but generally, they encompass:
- Recording maintenance history
- Scheduling preventive maintenance
- Tracking equipment usage
- Tracking compliance with safety regulations
A well-designed tracking app can significantly alleviate tedious manual processes, saving time and reducing human error. This immediacy allows organizations to respond swiftly to potential equipment failures, ensuring operational continuity.
Key Features of Maintenance Tracking Apps
Understanding the key features that define a robust maintenance tracking app is paramount to making an informed choice. Each feature serves a distinct purpose, contributing to the overall efficacy of maintenance operations.
Real-time Tracking
Real-time tracking distinguishes premium maintenance tracking apps from their lesser counterparts. It offers users the capability to monitor equipment conditions as they occur, which is vital for effective decision-making. With real-time updates, organizations can foresee equipment failures before they escalate, thereby minimizing downtime. A noteworthy characteristic of this feature is its role in fostering proactive maintenance strategies.
- Advantages: Provides immediate communication about equipment status, which leads to swifter action and fewer disruptions.
- Disadvantages: Depending on internet connectivity and app reliability, some users might encounter delays or inaccuracies.
Automated Alerts and Notifications
Incorporating automated alerts and notifications can serve as a game-changer in equipment maintenance. This feature ensures that critical maintenance activities, such as inspections or repairs due, are flagged. Highlighting this reliability, organizations can avoid the pitfalls of missed deadlines, enhancing the reliability of their operations. A unique attribute is the ability to customize notification settings, allowing users to control the frequency and type of alerts received.
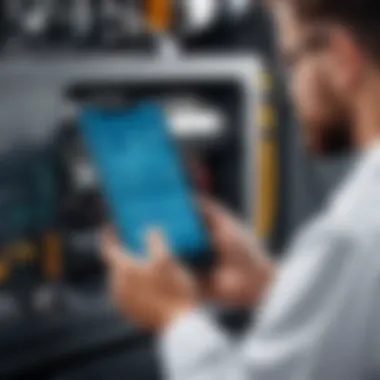
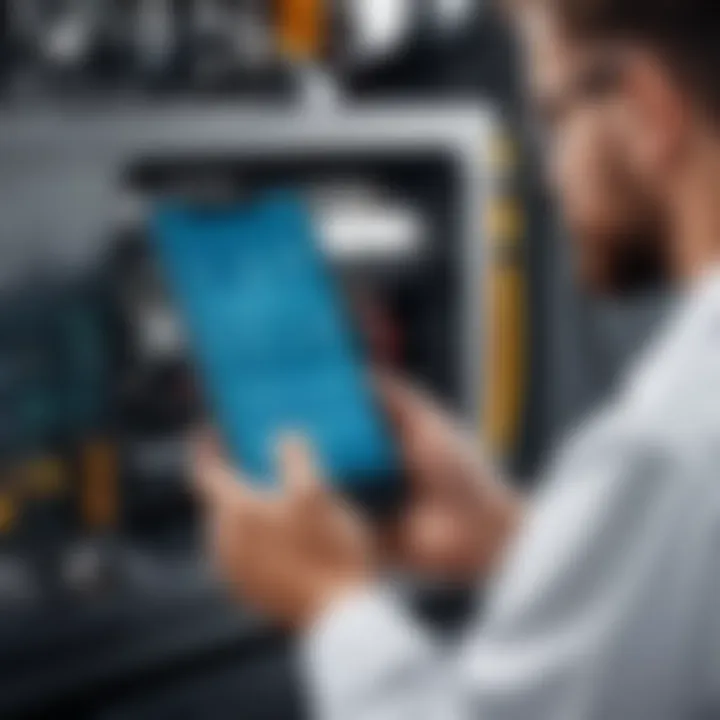
- Advantages: Reduces the risk of human error and helps maintain compliance with safety regulations.
- Disadvantages: If not managed properly, too many alerts can lead to notification fatigue among staff.
Reporting and Analytics
Reporting and analytics provide valuable insights into maintenance activities and equipment performance. This feature typically includes dashboards and analytical tools that help identify patterns and measure KPIs effectively. By focusing on this area, organizations can assess the effectiveness of their maintenance strategies, driving continuous improvement. A standout aspect is its ability to transform large amounts of data into actionable recommendations.
- Advantages: Empowers data-driven decision-making, ensuring resources are allocated efficiently.
- Disadvantages: Users must understand how to interpret analytics effectively, or they may overlook critical insights.
"In the fast-paced world of equipment management, the right tracking app can be the difference between seamless operation and costly downtime."
In summary, Equipment Maintenance Tracking Apps are indispensable tools in contemporary asset management. Their effective deployment not only optimizes workflows but also contributes to the longevity and reliability of equipment. Understanding their core functionalities and key features enables organizations to make informed choices that ultimately enhance their operational capacity.
Benefits of Using Equipment Maintenance Tracking Apps
In today’s fast-paced environment, businesses cannot afford to let their equipment go unattended. This is where equipment maintenance tracking apps become invaluable. These tools provide a structured approach, enabling organizations to manage their assets effectively. The benefits extend beyond just keeping machinery running well; they also encompass financial savings, safety improvements, and regulatory compliance. Understanding these benefits helps decision-makers embrace technology to optimize operational landscapes.
Operational Efficiency
Operational efficiency is one of the primary advantages of using equipment maintenance tracking apps. With these applications, organizations can streamline workflows and reduce downtime. Businesses often operate on tight schedules, and a failure or malfunction can bring operations to a screeching halt. By utilizing tracking apps, teams can set up automated reminders for maintenance checks. This proactive approach ensures all equipment is monitored regularly, thus preventing unexpected breakdowns.
Moreover, these apps analyze equipment performance data, aiding in informed decision-making. For instance, data analytics can reveal patterns in equipment failure. If machines in certain conditions frequently go haywire, management can evaluate those processes for potential redesigns. Factoring in the historical performance enables organizations to enhance productivity, as maintenance tasks can be scheduled during off-peak hours.
Cost Reduction
Cost reduction is another significant benefit that comes with using maintenance tracking apps. In many organizations, maintenance costs can spiral out of control when equipment isn’t properly monitored. By keeping track of service history, the apps can help identify equipment that often requires service, leading to preventive actions rather than reactive ones.
Maintenance apps allow companies to shift from costly corrective maintenance to a more manageable preventive maintenance model.
Additionally, avoiding unscheduled downtimes saves substantial sums collecting labor costs and parts replacements. With these tools in effect, businesses can forecast maintenance budgets more accurately, thus avoiding sudden financial shocks.
That said, implementing these apps requires an initial investment; however, they tend to pay for themselves over time through operational savings. It's akin to the old adage—"an ounce of prevention is worth a pound of cure." Emphasizing a proactive maintenance approach drastically mitigates future expenditures.
Improved Safety and Compliance
Safety is paramount in any operational setting, particularly when it comes to heavy or hazardous equipment. Equipment failures can lead to accidents, resulting in injuries or even fatalities. Maintenance tracking apps increase safety compliance by helping organizations adhere to industry regulations.
For example, many apps provide documentation trails for maintenance activities. If an inspector comes calling, organizations can present records that demonstrate compliance with safety standards. This not only keeps teams safe but also protects organizations from hefty fines associated with violations.
Furthermore, many tracking solutions feature tools that can flag when equipment exceeds operational limits. For instance, suppose a crane's load capacity has nearly been reached multiple times. The app can trigger alerts to help operators avoid risky maneuvers. This integration fosters a culture of safety that is essential in workplaces.
In summary, the benefits of equipment maintenance tracking apps are not just limited to operational gains but extend into significant cost savings and enhanced safety protocols. When organizations leverage these tools effectively, they set the foundation for smooth operations, decreased accident ratios, and long-term financial viability.
Selecting the Right Maintenance Tracking App
Choosing the correct equipment maintenance tracking app is pivotal. Organizations have unique needs, and the right app can streamline processes, reduce costs, and increase efficiency. It can also offer insights that help in the proactive management of assets. Skipping this step or picking an app that doesn’t match specific requirements could lead to wasted resources and inefficiencies.
Assessing Organizational Needs
Inventory Size
When we talk about Inventory Size, we're referring to the number of assets that an organization has. This can be anything from a handful of tools to hundreds of pieces of machinery. Understanding how many items need tracking is crucial. A small outfit may get by with a simple spreadsheet, but larger enterprises need more robust systems.
A key characteristic is scope. For companies with a large inventory, a system that automates tracking and maintenance scheduling is a no-brainer. It helps reduce human error and ensures that no equipment is overlooked. However, if the system is too complex for smaller inventories, it may become cumbersome and not worth the investment. A unique feature of considering inventory size is the ability to scale; an app might be cost-effective for small inventories, but it could be a nightmare at a larger scale.
Type of Equipment
Now, let’s dive into the Type of Equipment. Different industries utilize different types of machinery, each with its own maintenance needs. For instance, a medical facility will have specialized machinery compared to a manufacturing plant. This affects everything from the frequency of maintenance checks to the specific data recorded in the tracking system.
The distinguishing trait here is specificity. An app designed for heavy machinery might not suit a hospital's needs. This specificity can be a //blessing// for relevant industries. However, not having the features needed for unique environments could lead to a mismatch. Customization options in tracking apps can play a vital role in ensuring that they accommodate diverse equipment types.
Budget Constraints
Lastly, we touch upon Budget Constraints. This is often the make-or-break factor when it comes to technology adoption. Organizations must weigh the potential return on investment against upfront costs, including licensing fees, training expenses, and ongoing maintenance.
The main characteristic here is affordability matched with functionality. An app that offers extensive features but at an exorbitant price effectively becomes a luxury. Companies need to ensure that the investment is justified by the anticipated improvements in efficiency and cost reductions. One unique aspect of budget considerations is seeking out tiered pricing; this allows organizations to choose a plan that fits their direct needs without overextending financially.
Evaluating Software Features
The evaluation of an application should include a thorough examination of key software features.
User Interface and Experience
When discussing User Interface and Experience, we're delving into how intuitive and user-friendly the app is. If the interface looks like a jigsaw puzzle, your staff isn't going to engage with it. Simplicity is key.
The hallmark of a quality user interface is ease of navigation. A well-designed UI can boost productivity as staff don’t waste time figuring out how to use the app. But, a fancy interface laden with features doesn’t mean a lot if it complicates basic tasks. One feature to keep an eye out for is mobile compatibility; staff in the field often require access to data on-the-go, and a mobile-friendly interface can significantly enhance usability.
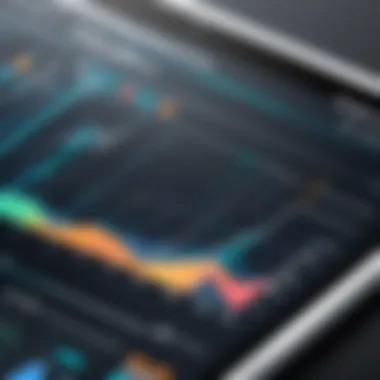
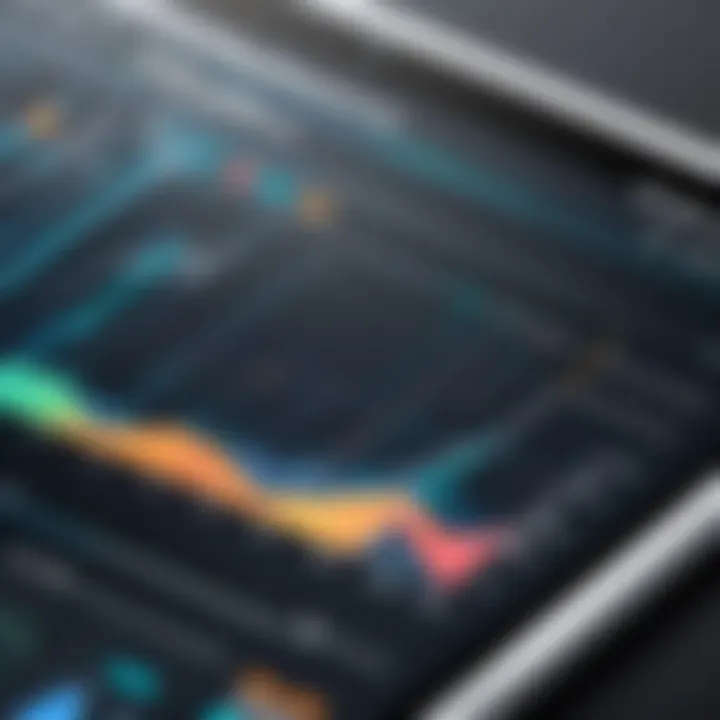
Integration Capabilities
On to the Integration Capabilities. An app is only as effective as its ability to work well with other systems. If it can’t connect with existing IT infrastructure, businesses may end up with information silos, hindering efficiency.
Integration’s critical characteristic is compatibility with other software. Many organizations use various applications for inventory, customer relations, and financial management. If the maintenance tracking solution can seamlessly integrate with these, it makes a massive difference. However, complex integration processes can deter companies from adopting new tech. A flexible API feature is vital in making sure that data flows freely without creating headaches for IT.
Scalability
Lastly, we must address Scalability. Businesses grow, and their needs evolve. The last thing a company wants is to invest in a tracking app that can’t accommodate future requirements.
The highlight of scalability is adaptability to changing business landscapes. A scalable app can grow in functionality alongside the organization, whether that means adding more equipment or users. It may provide different tiers of features as the size and complexity of operations increase. Yet, organizations must be careful; an overly complex solution can lead to confusion and operational slowdowns if not managed appropriately.
Implementation Strategies for Maintenance Tracking Apps
Implementing a maintenance tracking app is not just about choosing the right software; it's also about strategizing how to effectively integrate it into your operations. A well-thought-out implementation plan can make the difference between a seamless transition and a chaotic rollout. By focusing on specific steps such as planning and preparation, as well as monitoring and evaluation, organizations can ensure that they leverage their tracking apps to the fullest.
Planning and Preparation
Before diving headfirst into the implementation of a maintenance tracking app, organizations need to lay the groundwork. Planning and preparation serve as the stepping stones towards successful adoption.
Training Staff
Training staff on the new maintenance tracking app is crucial. It ensures that all users are familiar with the features and functionalities that the application offers. One key characteristic of effective training is its adaptability to different learning styles. Not every staff member absorbs information in the same way—some might benefit from hands-on sessions, while others might prefer guided tutorials.
The unique aspect of training staff is that it not only enhances productivity but also boosts morale. When employees feel equipped to handle new tools, they are generally more enthusiastic about their tasks. This can lead to a more engaged workforce, which is invaluable for maintaining a culture of continuous improvement. On the flip side, if training is overlooked or poorly executed, it can lead to frustration and resistance to the new system.
Setting Up Processes
Setting up clear processes is another vital aspect of preparation. This involves defining how tasks will interconnect with the maintenance tracking app. A standout feature of setting up these processes is the clarity it brings to workflows. Lack of defined processes can lead to chaos, confusion, and miscommunication, which ultimately hampers the benefits of implementing the app.
Establishing processes can be beneficial in aligning the application functions with real-world operations. It helps ensure that everyone knows not just how to use the tool, but why it matters for the organization's success. However, the challenge lies in potential over-complication. If processes are too rigid or elaborate, staff might find them cumbersome, which could defeat the purpose of simplifying maintenance tasks.
Monitoring and Evaluation
Once the app is implemented, the work doesn't just stop there. Ongoing monitoring and evaluation are essential to ensure the application continues to meet organizational needs.
Key Performance Indicators
Setting Key Performance Indicators (KPIs) is a powerful method to measure the effectiveness of the maintenance tracking app. These indicators provide a tangible way to assess whether the app is achieving its intended goals. A defining trait of KPIs is their ability to pinpoint areas for improvement. For example, if the average downtime of equipment hasn’t decreased post-implementation, it may indicate that further adjustments are needed.
The unique feature of utilizing KPIs lies in their quantitative nature. They can offer concrete data that can lead to actionable insights. By closely monitoring these indicators, organizations can fine-tune their maintenance strategies and maximize their app's utility. However, it’s essential to choose KPIs judiciously; focusing on too many metrics can dilute efforts and lead to analysis paralysis.
Feedback Loops
Creating feedback loops can greatly enhance the overall implementation process. They facilitate open lines of communication between staff and management, allowing for dynamic adjustments based on user experience. An important characteristic of feedback loops is their cyclical nature, promoting continuous learning and adaptation to the app’s functionalities.
The advantage of having feedback loops established is two-fold: They help in early identification of issues and encourage employee involvement in the improvement process. However, it’s crucial that feedback isn't just collected but actively utilized to make meaningful changes. Otherwise, it could lead to frustration and a feeling that staff opinions don’t matter, which can undermine trust and productivity.
"The effectiveness of any maintenance tracking app is directly proportional to the commitment shown in both its implementation and ongoing evaluations."
In summary, a meticulous approach towards implementing equipment maintenance tracking apps can yield significant advantages. By focusing on the preparation phase such as staff training and process setup, alongside rigorous monitoring through KPIs and feedback loops, organizations can not only enhance their operational effectiveness but also foster a culture of continuous improvement.
Challenges in Adopting Maintenance Tracking Apps
Adopting maintenance tracking apps can seem like a walk in the park, but, to say the least, the road can be a bit bumpy. Understanding the challenges associated with integrating these applications is pivotal for any organization looking to enhance their operational efficiency. The reluctance of employees to change how they do things, the hassle of aligning the new tools with current systems, and relying on technical support are just a few speed bumps on this journey. These factors play a key role in either making or breaking the success of the new system.
Addressing these challenges head-on can not only ease the transition but can also unlock numerous benefits, making it worthwhile to stick with the process. When the app integrates well into the workflow, it can streamline maintenance and lead to better resource allocation, ultimately lowering costs. Let's dive into these hurdles in more detail.
Resistance to Change
One of the biggest hurdles organizations face is the human factor—resistance to change. Often, employees get comfortable with familiar routines. Introducing new software like maintenance tracking apps can stir up feelings of unease and skepticism.
When folks are faced with new tools, they may feel like they've suddenly been thrown into the deep end. Some staff may ask, 'Why fix what's not broken?' This mentality can result in pushback, making the implementation process a tougher nut to crack. To smooth this over, businesses should focus on educating and training the workforce about the specific benefits of using a maintenance app.
- Involve employees early: Get their input during the decision-making process.
- Provide hands-on training: Allow staff to familiarize themselves with the app in a low-pressure environment.
- Show tangible benefits: Share success stories or data illustrating efficiency gains.
"Sometimes, it's not about the tools you use; it's about how well the team uses them."
Integration with Existing Systems
Another stumbling block can be the need for proper integration with existing systems. Companies often operate on a web of interconnected software, and pulling in a new maintenance tracking application can lead to alignment headaches. The risk is that if these systems don’t shuffle along together smoothly, it could lead to data silos and duplication of efforts. In short, it’s crucial to ensure that all systems effectively speak the same language.
The challenges include:
- Data Migration: Transferring historical data into the new app can be cumbersome and sometimes risky if not done accurately.
- Software Compatibility: Not every app plays nicely with others. Research is key – ensure that the new app can integrate with tools already in use.
- User Experience: Remember that a clunky user interface can drive employees up the wall rather than easing their workload.
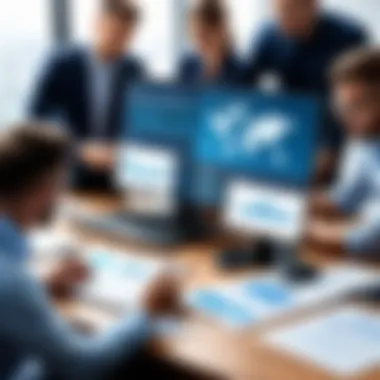
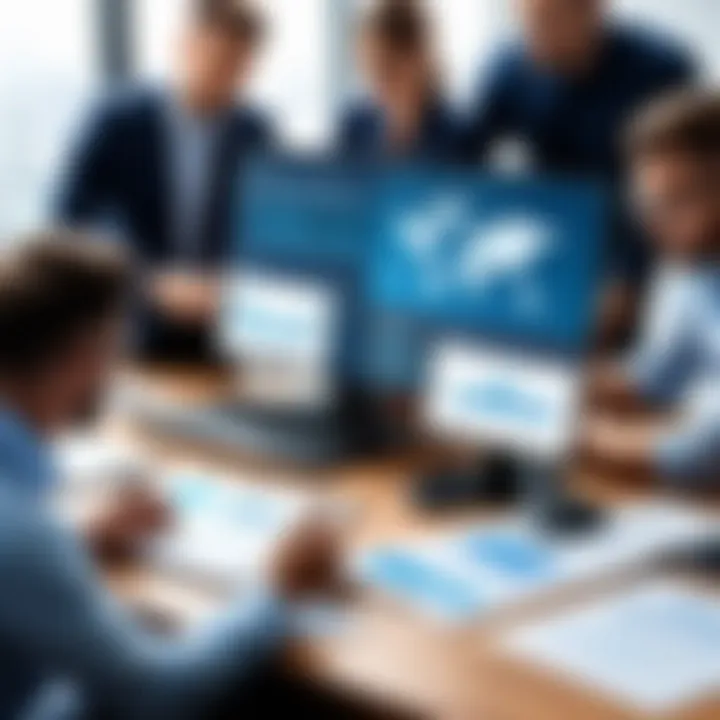
Strategically planning the integration process can help alleviate some of these concerns, making the transition much smoother.
Technical Support Requirements
Finally, there’s the matter of technical support. You can have the best app money can buy, but if it breaks down and there’s no one around to help, it’s as useful as a chocolate teapot. Ensuring adequate support is in place is crucial for moving forward.
Organizations need to figure out:
- In-house vs Outsourced Support: Will the company depend on internal IT teams, or will they rely on vendor support?
- Availability: Is there 24/7 support or just during business hours? Depending on the operational needs, this can dramatically affect productivity during off-hours issues.
- Training for IT staff: Ensure that those who will troubleshoot the app are properly trained and can react quickly when problems arise.
Ultimately, having a robust support system in place not only ensures uptime but also boosts employee confidence when using the maintenance tracking app, making them more likely to embrace the change.
In summary, while the challenges in adopting maintenance tracking apps may seem daunting, understanding and addressing them effectively can pave the way for a smoother transition. With a well-thought-out approach, the benefits of enhanced maintenance processes will far outweigh the discomfort of change.
Case Studies of Successful Implementations
The world of equipment maintenance tracking apps has transformed various industries, proving that effective maintenance management can lead to substantial gains in productivity and cost efficiency. By examining real-world implementations, organizations can understand how these applications can optimize their processes. This section delves into key case studies from different sectors, highlighting the benefits and nuanced considerations when adopting such technologies.
Manufacturing Industry
In the manufacturing sector, efficiency is everything. One notable case is Fabrico Corp, a mid-sized manufacturer of automotive parts. Before adopting maintenance tracking software, the company faced frequent machinery breakdowns that led to costly downtimes. Implementing the CMMS Pro app, they began to schedule preventive maintenance tasks systematically.
The results turned out to be impressive; downtime was reduced by 30% in just six months.
Key takeaways from Fabrico's experience included:
- Real-time Monitoring: The app allowed them to check machine performance in real time, enabling swift responses to potential issues.
- Data-Driven Decisions: By analyzing repair histories, Fabrico could determine which machines required more frequent maintenance, optimizing resource allocation.
- Increased Lifespan of Equipment: With regular maintenance, equipment longevity improved significantly, reducing replacement costs.
"Investing in a maintenance tracking app was a game changer for us. It’s not just about fixing things when they break, it’s about preventing those breaks from happening in the first place."
– Operations Manager, Fabrico Corp
Healthcare Sector
A pressing need for reliability defines the healthcare sector. MediHealth Services, a hospital infrastructure provider, faced challenges with managing the maintenance schedules of life-saving equipment like MRI machines and ventilators. They turned to the MedTrack maintenance app, designed specifically for healthcare applications.
The implementation led to remarkable improvements, especially in terms of compliance with health regulations. Some of the outcomesincluded:
- Enhanced Safety: Regular checks ensured that equipment operated at peak performance, crucial for patient safety.
- Automated Alerts: With timely notifications for service needs, the staff managed maintenance without disrupting patient care.
- Compliance Support: The app provided logs and records needed for inspections, significantly easing the administrative burden.
This shift underscored the importance of maintaining high standards in equipment upkeep, which is vital in a health care setting.
Field Services
Field service management has its unique set of challenges. Tech Solutions Inc., a company specializing in on-site repairs for consumer electronics, faced irregular maintenance scheduling, leading to inefficient service delivery. They adopted the FieldForce app, which allowed technicians to update maintenance logs on-the-go.
Benefits observed during this implementation included:
- Streamlined Operations: The ability to manage tasks in the field allowed for more organized service delivery and reduced response times.
- Improved Customer Satisfaction: Clients reported higher satisfaction due to shorter wait times and more effective service resolutions.
- Data Capture in Real-time: Technicians could instantly log repair issues, giving management deeper insights into frequently encountered problems.
The success of Tech Solutions Inc. showcases the profound impact that efficient tracking can have in the field service industry, particularly in enhancing customer satisfaction.
In closing, the exploration of these case studies illustrates how diverse sectors have leveraged equipment maintenance tracking apps to align with their unique operational demands. Often, the essence of success comes from not merely adapting new technologies but tailoring them to fit existing workflows and addressing specific challenges.
Future Trends in Equipment Maintenance Tracking Apps
In the rapidly evolving world of technology, equipment maintenance tracking apps are not just fads; they’re paving the way for future operational efficiencies. As businesses strive for better performance and longevity of their equipment, understanding the trends that shape these applications becomes paramount. In the coming years, emerging technologies will not only redefine how maintenance is conducted but will also enhance decision-making processes across industries. Therefore, staying ahead of the curve is vital for decision-makers looking to maintain competitive edges.
Artificial Intelligence and Machine Learning
Artificial Intelligence (AI) and Machine Learning (ML) are increasingly becoming integral to equipment maintenance tracking apps. These technologies have the potential to revolutionize predictive maintenance by analyzing historical data and identifying patterns that can indicate equipment failures before they occur. For instance, an AI-driven application might alert a factory manager to possible faults in a machine based on its performance metrics over time. This level of foresight can lead to significant cost savings and operational uptime, pleasing both management and the techs in the field.
The implementation of these technologies helps in automating routine tasks, from scheduling maintenance to ordering replacement parts. As AI gets more sophisticated, it can even learn from each maintenance cycle to optimize future processes. By leveraging AI and ML, businesses can ensure that their maintenance strategies become more proactive rather than reactive, leading to improved operational efficiency.
"AI in equipment maintenance is like having a crystal ball – it doesn't just show the future; it helps you shape it."
Mobile Accessibility
The accessibility of equipment maintenance tracking apps through mobile platforms is another trend gaining momentum. With the vast majority of professionals carrying powerful smartphones, the demand for mobile-friendly applications has surged. Mobile accessibility enables field technicians to access real-time data, log maintenance activities, and receive alerts from virtually anywhere. This flexibility bridges the gap between the office and the field, enhancing communication and efficiency.
Mobile apps can also offer users functionalities such as barcode scanning for inventory management and photo uploads for documenting maintenance tasks. Instant notifications about equipment status changes can streamline communications and decision-making processes, leading to timely interventions when issues arise. Moreover, mobile accessibility aligns with the increasing move toward remote work, allowing maintenance professionals to keep their operations running smoothly even when they are not physically present at the facility.
Finale
Understanding the role of equipment maintenance tracking apps is vital in today's fast-paced industry landscape. The conclusion not only ties up the arguments presented throughout this article but also emphasizes the powerful impact these tools can have on operational efficiency and compliance standards.
Summary of Key Takeaways
A few key points to carry away from this extensive examination include:
- Enhanced Efficiency: These apps streamline the maintenance process, allowing for quicker reactions to equipment issues, lowering downtime, and increasing productivity.
- Cost Control: Effectively tracking maintenance leads to more informed budgeting decisions, providing financial clarity and setting a clear assessment of expenditure versus savings.
- Data Insight: The wealth of data generated by these apps enables predictive maintenance strategies, helping organizations to foresee potential equipment failures and act preemptively.
- Regulatory Compliance: Keeping maintenance logs in an organized manner assists organizations in adhering to industry-specific regulations, minimizing the legal risks involved in non-compliance.
Final Thoughts on Implementation
To sum it up, one last thought on implementation: don’t treat the adoption of an equipment maintenance tracking app as an afterthought. It’s crucial for decision-makers to engage all stakeholders in the selection and implementation process.
Identify the unique needs of your organization.
Provide adequate training to ensure everyone knows how to use the app effectively.
Regularly review app performance and gather user feedback to adjust processes as necessary.
Incorporating this technology is not just about automating tasks, but about rethinking how your organization approaches equipment management. With the right app in place, you’ll find that maintaining your equipment can be both efficient and insightful, paving the way for a more productive future.