Inventory and Distribution: A Comprehensive Guide
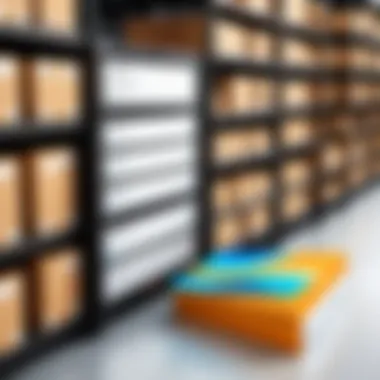
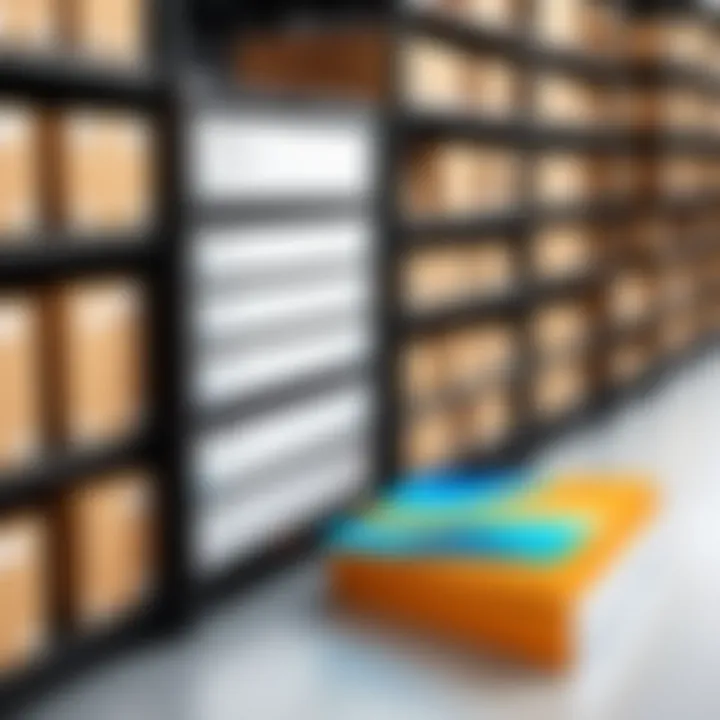
Intro
In the contemporary landscape of business operations, the significance of effective inventory and distribution systems cannot be overstated. These systems not only underpin the logistical framework of an enterprise but also play a pivotal role in determining customer satisfaction and operational efficiency. This guide delves into the fundamental aspects of inventory and distribution, emphasizing the latest trends, challenges, and technological advancements that are shaping the industry today.
Understanding the complexities of inventory management requires a detailed perspective on various components, including the methodologies employed, the technology utilized, and the strategies implemented to optimize overall performance. It is crucial for decision-makers and IT professionals to grasp how these features interlink and influence both productivity and profitability.
Overview of Core Features
An effective inventory and distribution system comprises several essential functionalities designed to streamline operations and enhance accuracy. These functionalities typically include inventory tracking, order management, demand forecasting, and reporting capabilities.
Description of essential functionalities
- Inventory Tracking: Keeping a real-time record of stock levels is vital. Organizations utilize inventory management software to monitor inventory in different locations and types.
- Order Management: Efficient order processing is necessary to meet customer demand swiftly. This feature helps businesses manage order entries, processing, fulfillment, and payment all in one platform.
- Demand Forecasting: This functionality leverages historical data and market trends to predict future inventory needs, minimizing excess stock and reducing the risk of stockouts.
- Reporting Capabilities: Robust reporting tools provide insights into inventory performance, helping in strategic planning and decision-making.
Comparison of features across top software options
Not all inventory and distribution software are created equal. A few notable solutions include systems such as Oracle NetSuite, SAP Business One, and TradeGecko. Each offers a range of features, but they excel in different areas:
- Oracle NetSuite focuses heavily on scalability and integrates seamlessly with financial systems.
- SAP Business One is recognized for its comprehensive ERP capabilities, suitable for larger enterprises.
- TradeGecko, on the other hand, is designed for small to medium businesses, offering user-friendly interfaces and essential functionalities without the complexity.
These differences highlight the importance of selecting a system that aligns best with specific business needs and operational scale.
User Experience and Interface
The user experience (UX) and interface (UI) design of inventory and distribution systems can significantly affect how effectively users interact with the software.
Insights into UI/UX design aspects
An intuitive UI enhances usability, allowing employees to navigate the system with ease. Key design elements should include a clear layout, accessible menus, and responsive features. Engaging graphics and straightforward paths to essential functions can reduce training time and improve productivity.
Importance of usability and accessibility
Ensuring that inventory and distribution systems are user-friendly makes it easier for employees to adopt new tools quickly. Usability also plays a role in minimizing errors during order processing and inventory tracking. Moreover, accommodating various user needs, including those with disabilities, enhances inclusivity and allows for a more diverse workforce to engage with the system.
A well-designed inventory and distribution system directly impacts operational efficiency, reducing delays and minimizing errors.
Investing in systems that prioritize these design aspects is crucial for organizations aiming to boost their operational effectiveness and satisfaction levels among users.
Understanding Inventory Management
Inventory management is a critical aspect of successful business operations. It involves overseeing the flow of goods from manufacturers to warehouses and ultimately to the point of sale. Effective inventory management helps businesses maintain the right stock levels to meet customer demand while reducing costs associated with excess inventory.
Definition of Inventory
Inventory refers to the assortment of goods and materials that a company keeps on hand. This includes raw materials, work-in-progress items, and finished products. Understanding inventory is essential for businesses as it directly influences cash flow and overall efficiency. Managing this crucial asset effectively ensures that operations run smoothly.
Types of Inventory
There are several key types of inventory, each with specific characteristics and roles in a business's overall strategy.
Raw Materials
Raw materials are the basic inputs used in the manufacturing process. They are crucial for production and contribute to a company's ability to fulfill orders. The characteristic of raw materials is their role as the foundation for creating finished products. They are a popular choice because they allow flexibility in production. However, holding too much raw material can tie up capital, creating a disadvantage for the business in terms of liquidity.
Work-In-Progress
Work-in-progress inventory includes items that are in the production stage but not yet finished. This type of inventory is significant as it helps track the progress of production. The key characteristic here is that it reflects the manufacturing process. It maintains a balance between production speed and efficiency. While necessary, excessive work-in-progress can also lead to inefficiencies and slow down overall production, which can be a drawback.
Finished Goods
Finished goods are completed products ready for sale. This type of inventory is crucial for meeting immediate customer demand. The characteristic of finished goods is that they are the final step in the production process. Having a sufficient stock of finished goods is beneficial for attracting sales and ensuring availability. However, maintaining too much finished inventory can result in storage costs and potential obsolescence, which can be seen as a disadvantage.
Importance of Effective Inventory Management
Effective inventory management is crucial for several reasons. It optimizes storage costs, ensures product availability, and enhances customer satisfaction. Properly managed inventory prevents stockouts and overstock situations, which can strain financial resources. Additionally, when inventory is well-managed, it allows companies to adapt quickly to market changes, ensuring they remain competitive. By integrating effective inventory management strategies, organizations bolster their operational efficiency and improve profitability.
Inventory Management Techniques
Understanding inventory management techniques is essential for any organization striving to maintain effective control over their stock levels and optimize operational efficiency. Proper management not only ensures that products are available when needed but also helps reduce waste and save costs. Companies can significantly enhance their overall performance by adopting these techniques. This section discusses three notable methods: Just-In-Time inventory, ABC Analysis, and Economic Order Quantity.
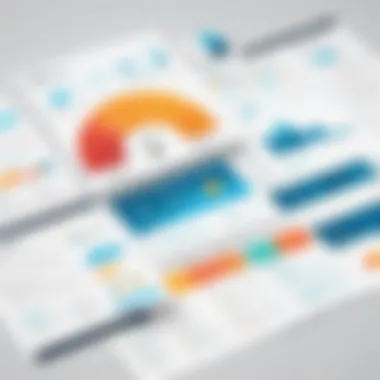
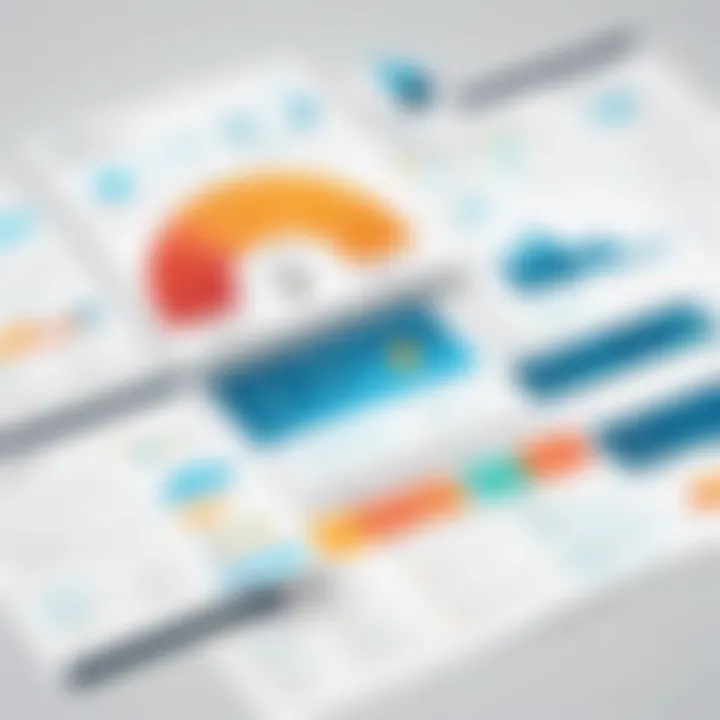
Just-In-Time (JIT) Inventory
Just-In-Time (JIT) inventory is a strategy that aims to reduce waste and increase efficiency by receiving goods only as they are needed in the production process. This technique minimizes inventory holding costs and reduces the space required for storage. JIT shifts the focus toward efficiency and reliability.
Implementing JIT requires strong supplier relationships, precise demand forecasting, and efficient logistics. Companies using this approach must be prepared to adjust production schedules to align with supply arrival. If managed correctly, JIT can lead to significant cost savings and improved productivity for a business.
ABC Analysis
ABC Analysis categorizes inventory into three groups based on their importance and value to the company. In this method, 'A' items are the most valuable, constituting a small percentage of the total inventory. 'B' items are moderate in value, while 'C' items are the least valuable and make up the majority of the inventory.
Using this strategy helps businesses direct their resources more effectively. For instance, more attention and control are placed on 'A' items, given their high value. Organizations often apply different monitoring and management practices across these categories to ensure that significant resources are allocated effectively, enhancing overall inventory performance.
Economic Order Quantity (EOQ)
The Economic Order Quantity (EOQ) model determines the optimal order size that minimizes total inventory costs, including holding costs and ordering costs. This technique helps balance the carrying cost of inventory with the ordering cost to find a sweet spot in inventory management.
Implementing EOQ involves evaluating several factors:
- Demand rate: How often do items need to be restocked?
- Holding costs: What is the cost to store goods?
- Order costs: What do suppliers charge to process an order?
By using EOQ, companies can make data-driven decisions about when and how much to order, ultimately streamlining inventory management. The focus remains on reducing overhead costs while meeting demand efficiently.
By mastering these inventory management techniques, organizations can align their stock levels with demand while minimizing costs and enhancing service delivery.
These inventory management techniques represent critical elements in a comprehensive strategy. By effectively integrating JIT, ABC Analysis, and EOQ into their operations, businesses can achieve substantial improvements in efficiency and cost-effectiveness.
The Role of Technology in Inventory Management
Technology has become an indispensable part of inventory management in modern business. Its integration optimizes processes, enhances visibility, and increases efficiency across supply chains. Organizations that leverage technology can respond quicker to market demands and ensure that stock levels align with customer needs. This section explores several technological elements crucial in inventory management.
Inventory Management Software
Inventory management software serves as a foundational tool for businesses. Applications such as Oracle NetSuite, Fishbowl, and TradeGecko allow companies to track inventory levels in real-time. Users can set alerts for stock shortages and gather data on inventory turnover. This software also aids in the automation of repetitive tasks, minimizing human error and maximizing accuracy. The ability to analyze trends assists businesses in making informed decisions about future stock purchases.
Automation and Robotics
Automation and robotics are transforming inventory management practices. Automated systems streamline processes by handling tasks like picking and packing goods, which reduces the time taken to fulfill orders. Automated guided vehicles (AGVs) and drones can navigate warehouses, transporting items efficiently. The initial investment in automation may be substantial, but the return on investment often materializes through reduced labor costs and higher operational speed.
Data Analytics in Inventory Strategies
Data analytics plays a vital role in optimizing inventory strategies. With advanced analytics, organizations can gather insights from sales patterns, customer behaviors, and market trends. These insights inform stock decisions, allowing for better forecasting and demand planning. Businesses can utilize tools such as Tableau or Google Analytics to visualize data, making it easier to identify areas for improvement. Understanding how data impacts inventory will lead to more strategic and intelligent practices.
The integration of technology in inventory management is not just about efficiency; it's about creating a competitive advantage in an ever-evolving marketplace.
In summary, technology has redefined inventory management, injecting precision and expediency into systems that are critical for operational success. Embracing these technological advancements is essential for organizations wishing to thrive in contemporary market environments.
Distribution Fundamentals
Distribution is a vital component in the supply chain process, influencing how products reach the end consumer. Understanding distribution fundamentals can help businesses enhance efficiency and minimize costs. This section discusses essential elements like definitions, channels, and strategies for effective distribution. It also addresses the benefits and considerations that come with mastering these concepts.
Definition and Key Concepts
Distribution refers to the process of delivering products from manufacturers to consumers. This includes various activities, such as warehousing, inventory management, transportation, and order fulfillment. Key concepts include:
- Logistics: The planning and execution of moving products. It encompasses transportation and inventory management.
- Distribution Network: The interconnected system of warehouses, transportation methods, and channels used to deliver goods.
- Market Coverage: The extent to which a distribution strategy reaches potential customers in a given area.
Understanding these concepts is fundamental for businesses aiming to optimize their distribution systems.
Distribution Channels
Distribution channels are pathways through which products flow from producers to consumers. Recognizing and leveraging the right channels can significantly impact sales and customer satisfaction.
Direct Distribution
Direct distribution involves selling products straight from the manufacturer to the consumer without intermediaries. This model offers the benefit of better control over pricing and customer interaction. Additionally, it allows businesses to gather direct feedback from end-users. The key characteristics include:
- Cost-effectiveness: Reduces costs by eliminating middlemen.
- Customer Relationships: Encourages direct engagement with buyers.
However, it may require more resources in marketing and logistics, which can be a challenge for some businesses.
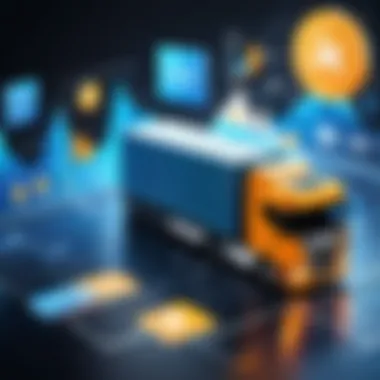
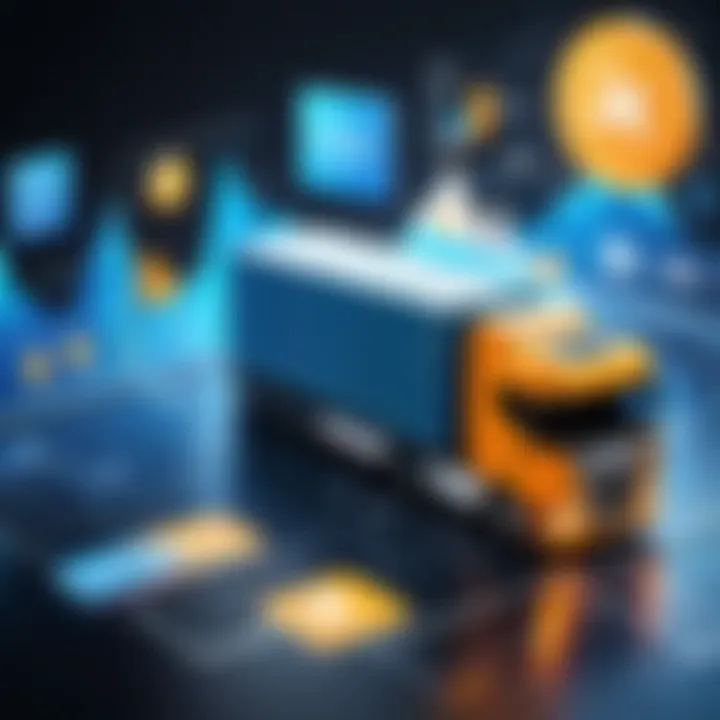
Indirect Distribution
Indirect distribution relies on intermediaries like wholesalers or retailers to get products to consumers. This method is beneficial because it often leads to broader market reach. The key features include:
- Wider Coverage: Provides access to various markets through established channels.
- Reduced Burden: Frees manufacturers from responsibilities such as retail operations.
Nonetheless, relying on intermediaries can decrease pricing control and customer relationship management.
Strategies for Effective Distribution
To ensure successful distribution, companies should implement effective strategies. Some key strategies include:
- Select Appropriate Channels: Choose channels that align with the target market.
- Invest in Technology: Utilize software for inventory management and logistics operations.
- Monitor Performance: Regular evaluations of distribution efficiency can help identify areas for improvement.
Adopting these strategies can enhance distribution effectiveness.
"Understanding distribution fundamentals is essential for optimizing product flow and improving customer satisfaction."
Logistics and Its Influence on Distribution
Logistics plays a crucial role in the distribution process, serving as the backbone that connects various components of the supply chain. It encompasses the planning, implementation, and control of the movement and storage of goods, services, and related information. Understanding logistics is essential for organizations aiming to enhance their distribution strategies. Effective logistics can lead to cost reduction, time savings, and improved customer satisfaction.
Logistics Management Overview
Logistics management involves a range of activities. It includes transportation, warehousing, inventory management, order fulfillment, and distribution planning. These elements are vital for efficient supply chain performance.
Main responsibilities in logistics management include:
- Transportation Management: Overseeing the movement of goods between locations. Choosing the right transportation methods can significantly affect shipping times and costs.
- Warehousing: Managing storage sites for inventory. Optimizing warehouse layout can improve picking efficiency and reduce lead times.
- Inventory Control: Ensuring an accurate count of stock. This prevents stockouts and excess inventory, which can tie up capital and lead to waste.
- Order Processing: Ensuring timely handling of customer orders. Streamlining this process can improve customer experience and loyalty.
Achieving a balance between these components is critical. The right logistics strategy can reduce operational costs while ensuring that products reach customers in a timely manner.
Supply Chain Dynamics
Supply chain dynamics refer to the interconnected flow of materials, information, and finances as products move from suppliers to consumers. Each link in the chain impacts the overall efficiency of logistics and distribution.
Key aspects of supply chain dynamics include:
- Collaboration: Strong relationships among suppliers, manufacturers, and retailers enhance information sharing and problem-solving.
- Visibility: Real-time tracking of inventory and shipments can help organizations respond promptly to any disruptions in the chain.
- Flexibility: The ability to adapt to changes in demand or market conditions is crucial. Supply chains must be resilient to handle unexpected events.
In today's global market, businesses must continually assess their supply chain dynamics to ensure they can meet customer demands efficiently.
Impact on Customer Satisfaction
Logistics and distribution have a direct influence on customer satisfaction. When done effectively, they can lead to better service levels, reduced delivery times, and enhanced product availability.
Factors to consider include:
- Delivery Speed: Customers expect fast turnaround times. Efficient logistics can drastically reduce lead times from order to delivery.
- Accuracy: Accurate order fulfillment ensures customers receive what they ordered, leading to satisfaction and repeat business.
- Cost Management: Managing logistics costs helps keep product prices competitive without sacrificing service quality.
"The right logistics strategy not only enhances distribution efficiency but also elevates the customer experience to a new level."
In summary, a solid understanding of logistics and its influence on distribution is essential for organizations aiming to thrive in the competitive market. Proper logistics management can create a seamless flow of goods, reflecting positively on customer satisfaction and operational success.
Challenges in Inventory and Distribution
In the landscape of inventory and distribution, it is essential to address the challenges that many businesses encounter. These challenges can significantly affect operational efficiency and customer satisfaction. Recognizing and understanding these obstacles allows decision-makers to implement effective solutions. Investing time to analyze these issues leads to better planning and optimization of resources. Addressing this topic enhances the reader's grasp of potential pitfalls and prepares them for various scenarios that may arise.
Common Obstacles in Inventory Management
Effective inventory management can be undermined by various common obstacles. Some of these include:
- Inaccurate Inventory Records: Discrepancies often arise from manual counts or poor data entry.
- Demand Fluctuation: Sudden changes in customer demand can lead to stockouts or excess inventory.
- Supplier Reliability: Delays from suppliers can affect the timely availability of stock.
- Limited Visibility: Without the right tools, businesses may lack insights into inventory levels.
- Inefficient Processes: Outdated methods can waste time and resources, leading to higher operational costs.
Each of these obstacles presents unique challenges. Overcoming them requires a strategic approach and implementation of modern inventory management practices.
Distribution Challenges
Distribution is not without its challenges. Companies frequently face issues such as:
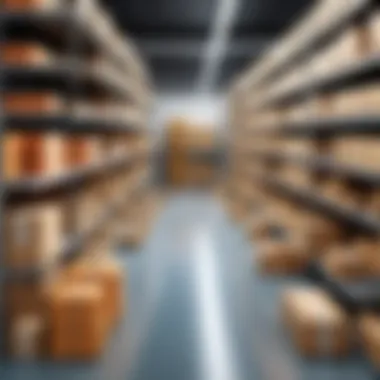

- Transportation Costs: Rising fuel prices and logistics can escalate expenses significantly.
- Route Optimization: Ineffective routing can lead to delayed deliveries and unhappy customers.
- Order Fulfillment Errors: Mistakes in order processing and shipping affect customer trust.
- Inventory Allocation: Balancing stock across multiple locations can be complex and prone to errors.
- Regulatory Compliance: Keeping up with local and international laws can complicate operations.
Addressing these distribution challenges is critical. By developing efficient systems and logistics strategies, companies can enhance their overall performance and customer satisfaction.
Impact of Global Events
Global events can dramatically shape the landscape of inventory and distribution. Factors such as:
- Pandemics: Events like COVID-19 have caused widespread supply chain disruptions.
- Natural Disasters: Hurricanes, floods, or earthquakes can hinder shipping and logistics.
- Political Instability: Changes in government policies and trade agreements can impact operations.
- Market Demand Changes: The global economy's volatility affects purchasing behavior and inventory needs.
The response to these global events must be agile. Businesses that can adapt quickly to changing circumstances often emerge stronger and more resilient.
"Understanding the spectrum of challenges in inventory and distribution enables better preparedness and strategic planning."
Each of these sections reveals the complexities tied to inventory and distribution management. Organizations must acknowledge these hurdles and employ effective methods to navigate them for ongoing success.
Best Practices for Inventory and Distribution Efficiency
In todayโs rapidly changing market, mastering inventory and distribution efficiency is essential for sustaining competitive advantage. The cost of holding excess inventory can be significant, impacting cash flow and profitability. Therefore, businesses must adopt best practices in managing these core operations. Efficient inventory and distribution processes contribute not only to reducing costs but also to improving customer satisfaction through timely deliveries and better product availability.
Inventory Optimization Strategies
Optimizing inventory levels is crucial. This involves finding the balance between meeting customer demand and minimizing excess stock. Here are some key strategies:
- Demand Forecasting: Analyze historical sales data to predict future demand. This helps in adjusting inventory levels proactively.
- Safety Stock Calculation: Maintain a buffer stock to protect against uncertainties in demand and supply chain disruptions.
- Regular Audits: Conduct periodic reviews of inventory status, which helps in identifying slow-moving items and allows timely decisions on stock clearance.
- Lean Inventory Techniques: Adopt methods like Just-in-Time, which reduces holding costs by receiving goods only as they are needed.
Incorporating these strategies helps businesses maintain optimal inventory levels while reducing waste and ensuring efficiency in operations.
Improving Distribution Processes
Distribution processes are vital in delivering products to customers efficiently. Improving these processes involves several steps:
- Route Optimization: Use software tools for planning effective delivery routes. This minimizes travel time and costs.
- Centralized Distribution Centers: Establishing central hubs can streamline logistics and improve delivery speed to different regions.
- Inventory Visibility: Implementing real-time tracking systems allows businesses to monitor inventory levels across distribution points.
- Collaborative Partnerships: Work with logistics providers to enhance service levels and reduce delivery times.
Focusing on these elements can lead to significant improvements in how products reach consumers and enhance overall customer experience.
Integrating Systems for Better Data Flow
A seamless flow of information is critical for efficient operations in inventory and distribution. Integrating systems can enable comprehensive data analysis and provide actionable insights. Here are some considerations:
- Use of ERP Systems: Implementation of an Enterprise Resource Planning (ERP) system allows businesses to integrate all facets of their operations, improving data accuracy.
- Automation of Processes: Employ automated systems in warehousing, such as Automated Guided Vehicles (AGVs) and robotics. These help in reducing manual errors and speeding up operations.
- Cloud-based Solutions: Utilizing cloud technologies ensures real-time data access for all stakeholders, improving communication and response times.
- API Integrations: Leverage APIs to connect different software and platforms, ensuring smooth data transfer.
Integrating these systems enhances transparency and supports informed decision-making across the organization.
"Efficiency in inventory and distribution is not just about speed; itโs about strategic alignment across processes."
By adopting these best practices, organizations can not only enhance their efficiency but also prepare themselves for the changing landscape in inventory and distribution management.
Future Trends in Inventory and Distribution
The landscape of inventory and distribution is ever-evolving. Understanding future trends is crucial for businesses aiming to remain competitive and efficient. Organizations must adapt to changes driven by technology, consumer behavior, and environmental considerations. These trends inform operational choices that can enhance efficiency, reduce costs, and improve customer satisfaction. This section explores key advancements and shifts that are set to shape the future of inventory and distribution.
Emerging Technologies
Artificial Intelligence
Artificial Intelligence (AI) is revolutionizing inventory and distribution by facilitating smarter decision-making. AI's ability to analyze vast datasets means businesses can predict demand more accurately and manage stock levels effectively. A key characteristic of AI is its capacity to learn from patterns, allowing it to optimize operations continuously. This makes AI a beneficial choice for enhancing inventory management strategies.
One unique feature of AI is its predictive analytics capability. By using machine learning algorithms, it can forecast customer behavior and stock requirements, leading to reduced waste and improved service levels. However, AI implementation can come with challenges. Data privacy concerns and the need for specialized expertise can deter some organizations.
Blockchain
Blockchain technology serves as a promising tool for improving transparency in the supply chain. Its decentralized nature ensures that each transaction is recorded in a secure and tamper-proof manner. This characteristic makes blockchain a popular choice for businesses focused on authenticity and traceability.
A unique feature of blockchain is its smart contract capability, which automates agreement enforcement. This leads to increased efficiency in transactions and reduced costs associated with intermediaries. Despite its advantages, blockchain presents challenges, such as high initial setup costs and the need for widespread adoption across supply chain participants.
Sustainability in Distribution Practices
Sustainability is becoming a major focus in inventory and distribution. Companies are increasingly seeking ways to minimize their environmental impact. This includes optimizing logistics routes to reduce fuel consumption and integrating eco-friendly packaging solutions.
Additionally, sustainable practices often result in cost savings. By minimizing waste and improving resource use, organizations can enhance their bottom line. The importance of transparency in sustainable practices cannot be understated. Consumers today expect companies to demonstrate accountability in their supply chain.
E-commerce and Direct-to-Consumer Trends
The rise of e-commerce has transformed the way businesses think about inventory and distribution. Companies are adapting by developing direct-to-consumer models that eliminate middlemen. This trend allows businesses to offer competitive pricing and personalized customer experiences.
Furthermore, rapid delivery expectations influence inventory management as companies strive to balance stock levels against potential demand spikes. This shift pushes businesses to invest in technology that enhances fulfillment processes. Integrating effective e-commerce strategies can foster stronger relationships with customers, ensuring loyalty and driving growth.