Manufacturing Software Systems: A Comprehensive Overview
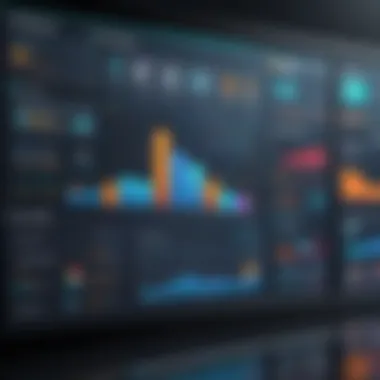
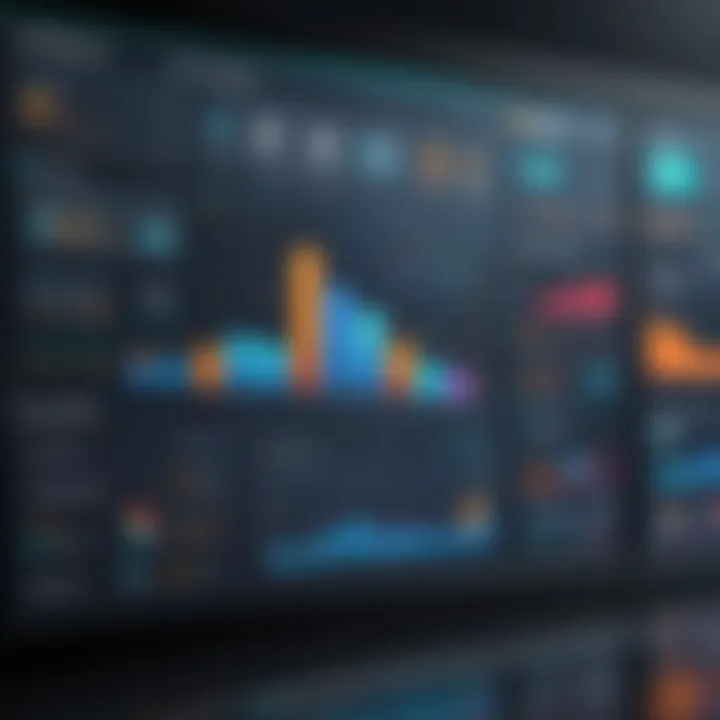
Intro
Manufacturing software systems serve as a cornerstone in the modern production landscape. As industries strive for enhanced efficiency and productivity, the role of software cannot be understated. The optimization of production processes has become paramount, and these systems rise to the occasion by improving workflows and ensuring better resource management. Understanding the various types of software solutions available can be challenging, yet it is crucial for the decision-makers and IT professionals in the field. In this article, we will dissect the essential features and functionalities, user experiences, and future trends within manufacturing software systems.
Overview of Core Features
Manufacturing software encompasses a range of functionalities tailored to streamline production and improve operational efficiency. Understanding these core features can aid in selecting the most appropriate solution for specific business needs.
Description of essential functionalities
Key functionalities of manufacturing software systems often include:
- Production Planning and Scheduling: This function allows manufacturers to optimize production schedules, ensuring that resources are utilized effectively and time is not wasted.
- Inventory Management: A critical feature, inventory management tracks raw materials and finished goods, giving real-time visibility into stock levels.
- Quality Control: This ensures the final products meet certain standards, reducing waste and enhancing customer satisfaction.
- Analytics and Reporting: Many systems come equipped with tools to analyze performance data, generating valuable insights for decision-making.
- Supply Chain Management: Effective systems also integrate supply chain processes, facilitating better communication between suppliers and manufacturers.
Comparison of features across top software options
When comparing leading software solutions, it is essential to focus on how their features align with business goals. Some notable options include:
- SAP Manufacturing Execution: Known for comprehensive analytics and real-time reporting features.
- Oracle Manufacturing Cloud: Offers superior inventory management and robust supply chain capabilities.
- Plex Manufacturing Cloud: Renowned for its focus on quality control and production planning.
Each option presents unique advantages that cater to various operational demands.
User Experience and Interface
The user experience (UX) and interface (UI) design of manufacturing software are crucial in maximizing its functionality. An intuitive interface can enhance usability and ensure that employees can effectively engage with the system.
Insights into UI/UX design aspects
Modern manufacturing software often incorporates user-friendly designs that facilitate ease of navigation and accessibility. Important design aspects include:
- Clear Navigation Menus: Users should find it easy to access different functions without excessive clicks.
- Responsive Design: Software should function seamlessly across devices, including tablets and smartphones.
- Visual Data Representation: Charts and dashboards can help users quickly grasp critical performance metrics.
Importance of usability and accessibility
Usability and accessibility cannot be overlooked in manufacturing software. Systems that prioritize these aspects have been shown to improve productivity and reduce training time for new users. Ensuring all team members can access essential functions, regardless of their technical skill level, is vital for effective implementation.
"User-friendly design is not just about aesthetics; it fundamentally influences productivity and operational efficiency in a manufacturing environment."
The combination of robust features and an effective user interface ultimately enhances the overall effectiveness of manufacturing software systems. As industries continue to evolve, it is vital to remain adaptable and informed about the available solutions.
Prolusion to Manufacturing Software Systems
Understanding manufacturing software systems is critical in today's fast-paced production environments. This article aims to explore the vital role these systems play in manufacturing. With technological advancements, software solutions have transformed traditional processes, making them more efficient and responsive. Manufacturers must grasp these elements to stay competitive and optimize their operations.
Defining Manufacturing Software
Manufacturing software refers to a range of applications and tools designed to support and enhance various production processes. These applications can help with everything from planning and scheduling to inventory management, quality control, and more. Specific examples include Enterprise Resource Planning (ERP) systems, Manufacturing Execution Systems (MES), and Quality Management Systems (QMS). Each system serves distinct purposes, addressing specific needs within the manufacturing lifecycle. By integrating these solutions, manufacturers can streamline operations and improve overall productivity.
The Importance of Software in Manufacturing
Software plays a crucial role in modern manufacturing environments. As companies strive for operational excellence, the significance of effective software systems cannot be overstated. These systems enable a high level of efficiency, allowing manufacturers to minimize downtime and reduce waste. Furthermore, they facilitate improved collaboration among teams and departments, breaking down silos that often hinder productivity.
"The right manufacturing software can serve as a backbone for decision-making, guiding strategies and informing critical changes."
Moreover, with increasing market pressure, being agile and responsive is essential. Manufacturing software supports these demands by offering real-time data analytics and insights. This capability enables manufacturers to make informed decisions quickly, ensuring that they can react promptly to changing conditions. In summary, the role of software in manufacturing transcends mere operational support; it is integral to driving innovation and achieving market success.
Types of Manufacturing Software Systems
Understanding the various types of manufacturing software systems is crucial for organizations wanting to streamline their operations. Each type serves distinct purposes and offers unique benefits that can significantly impact productivity and efficiency.
Enterprise Resource Planning (ERP) Systems
ERP systems are integrated platforms that manage day-to-day business activities. They provide a consolidated view of core business processes, including finance, supply chain management, and human resources. The primary goal of an ERP is to enhance efficiency by ensuring that information from various departments is harmonized and accessible.
Benefits of ERP systems include:
- Improved data accuracy through real-time information updates
- Enhanced collaboration as departments can share information seamlessly
- Better compliance with industry regulations due to standardized processes
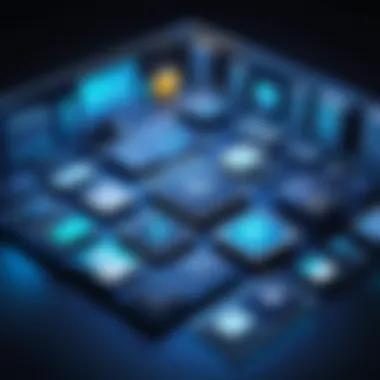
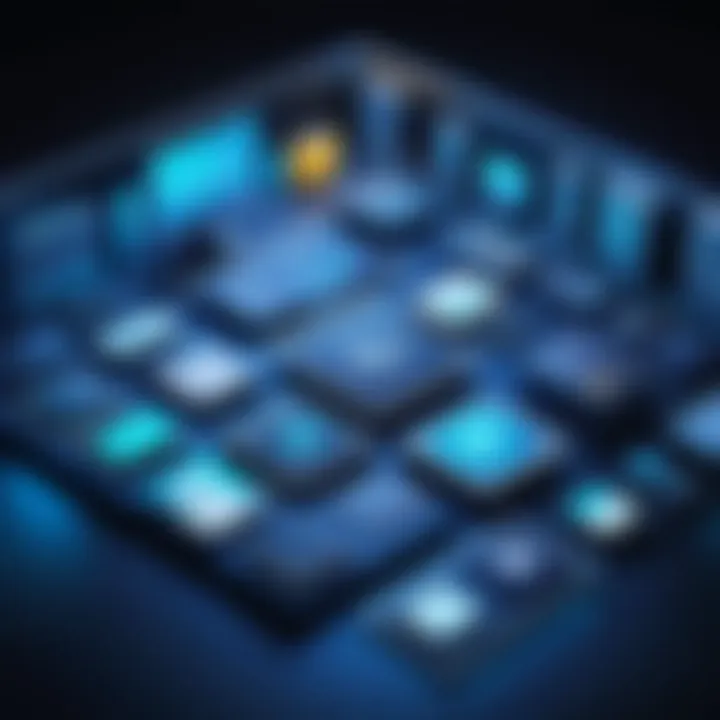
Key players in the ERP space include SAP, Oracle, and Microsoft Dynamics. Each provides a range of functionalities tailored to different industry needs.
Manufacturing Execution Systems (MES)
MES are designed to monitor and control manufacturing processes on the shop floor. They bridge the gap between enterprise-level systems and production-level activities, offering insights into real-time operations. MES improves production efficiency by providing tools for tracking work-in-progress, maintaining quality standards, and managing labor and equipment.
Some core functionalities include:
- Real-time production tracking to identify bottlenecks
- Inventory management to ensure materials are available when needed
- Quality control features to maintain product specifications
Notable software solutions for MES include Siemens Opcenter and Rockwell Automation's FactoryTalk.
Product Lifecycle Management (PLM) Software
PLM software helps organizations manage a product's lifecycle from inception through design and manufacturing to service and disposal. It enables efficient product data and process management across different teams. By centralizing product information, PLM systems facilitate better collaboration and informed decision-making.
Features of PLM software include:
- Version control to manage changes in product design
- Regulatory compliance tools to ensure products meet necessary standards
- Collaboration tools that enable teams to work together on product development
Top PLM solutions include PTC Windchill and Dassault Systèmes’ ENOVIA.
Supply Chain Management (SCM) Software
SCM software focuses on optimizing the flow of goods, services, and information throughout the supply chain. Effective SCM solutions improve overall supply chain visibility, coordination, and efficiency. Companies can leverage real-time data to make strategic decisions to reduce lead times and costs.
Key benefits of SCM software involve:
- Enhanced demand forecasting to manage supply effectively
- Increased supplier collaboration leading to better procurement strategies
- Transportation and logistics optimization for cost savings
Renowned SCM systems include Oracle SCM Cloud and SAP Integrated Business Planning.
Quality Management Systems (QMS)
QMS software ensures that products meet quality standards and comply with industry regulations. These systems are essential in minimizing defects and enhancing overall product quality. By implementing a QMS, manufacturers can continuously improve their processes and products.
Important features of QMS include:
- Document control to maintain quality documentation
- Non-conformance management to address quality issues swiftly
- Audit management to evaluate compliance with quality standards
Popular QMS solutions include ISO 9001 Software and MasterControl.
Key Features of Manufacturing Software Systems
Understanding the key features of manufacturing software systems is essential for organizations aiming to improve their production processes. These features determine the effectiveness, usability, and adaptability of any software solution in the manufacturing arena. With industries evolving at a rapid pace, the ability to leverage the right software can significantly impact operational success. Key features serve as a foundation for assessing various software systems, ensuring that decision-makers choose solutions that align with their specific business needs. Below are critical attributes to consider:
Integration Capabilities
Integration capabilities are crucial for manufacturing software systems. The ability for different systems to communicate with each other enhances information flow and operational coherence. For example, a manufacturing company that uses an Enterprise Resource Planning (ERP) system must ensure it can integrate seamlessly with Manufacturing Execution Systems (MES) and Quality Management Systems (QMS). This ensures that data from various departments—like production, finance, and inventory management—works in unison, resulting in more accurate reporting and better decision-making. Effective integration minimizes the risk of data silos, enabling real-time monitoring and adjustments as needed.
Real-time Data Analytics
Real-time data analytics is another paramount feature of modern manufacturing software. Availability of instant data empowers organizations to make quicker and more informed decisions. For instance, data analytics tools can provide immediate insights into production efficiency and downtimes. This allows managers to tackle issues proactively rather than reactively. In complex manufacturing environments, real-time insights lead to enhanced operational visibility, thus facilitating precision management in processes. Companies that can analyze their performance data instantly are often more agile and capable of adapting to market fluctuations or internal changes.
User-friendly Interfaces
User-friendly interfaces play a significant role in guaranteeing high user adoption rates. Software solutions that prioritize user experience tend to attract less friction during training and implementation phases. A clean, intuitive interface allows users across varying skill levels to interact with the system efficiently. For example, if a quality control technician can easily navigate through a QMS, they will likely report issues quickly and accurately. Consequently, ease of use directly correlates with productivity and operational efficiency; poor interface design often leads to frustration and decreased output.
Scalability and Flexibility
Scalability and flexibility are vital considerations for any manufacturing software. As organizations grow or adapt to changing market demands, their software systems must have similar capabilities. Software that can scale allows businesses to add features or users without significant disruptions. Flexibility in systems means that companies can adjust functionalities based on industry shifts or internal processes. A manufacturing firm, for instance, may expand into new product lines. If the software can adapt, the transition becomes smoother and less costly. This attribute is essential for long-term viability and sustainability in an ever-changing manufacturing landscape.
Compliance and Regulatory Features
Finally, compliance and regulatory features are critical. Manufacturing often operates under stringent regulatory environments. Software that helps organizations comply with various regulations—from environmental standards to safety protocols—can prevent costly fines and disruptions. Features like audit trails, automated compliance reporting, and documentation management are highly valuable for staying compliant. Ensuring that manufacturing processes adhere to regulations protects companies not just from legal issues but also enhances their reputation with customers and stakeholders.
In summary, the key features of manufacturing software systems—integrations, real-time analytics, user interfaces, scalability, and compliance—together dictate their effectiveness and applicability in real-world manufacturing scenarios. Decision-makers must invest time in understanding these elements when evaluating potential solutions.
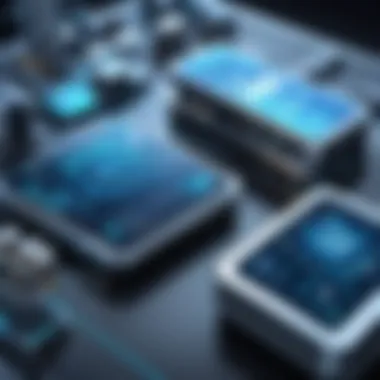
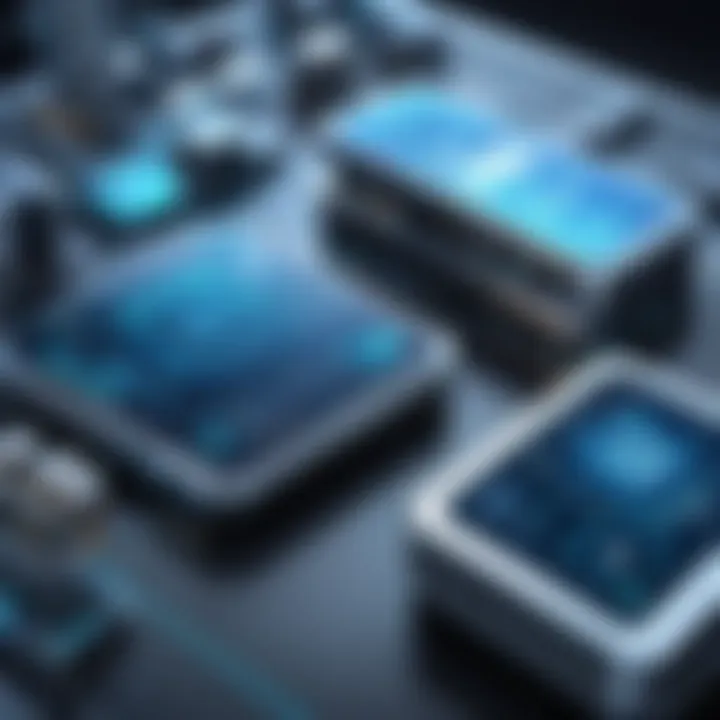
Ultimately, these features form the bedrock of successful manufacturing operations, enabling companies to thrive in competitive markets.
Benefits of Implementing Manufacturing Software
Implementing manufacturing software brings transformative benefits that go beyond simple enhancements to operational functions. Recognizing these advantages can significantly help decision-makers optimize their processes, tailor solutions, and drive competitive advantage. This section outlines key benefits including operational efficiency, cost reduction, improved collaboration, enhanced quality control, and data-driven decision making.
Operational Efficiency
Operational efficiency is a primary benefit of manufacturing software. These systems streamline production processes by automating routine tasks, reducing manual errors, and enhancing workflow. Automating inventory management, scheduling, and production tracking minimizes delays and maximizes resource utilization.
Moreover, real-time monitoring capabilities allow companies to quickly assess and respond to issues such as machine breakdowns or supply shortages. Overall, an efficient operation leads to higher output and lower cycle times, resulting in better meeting customer demands.
Cost Reduction
Manufacturing software contributes to significant cost reduction. By optimizing resource allocation and minimizing wastage, these systems allow manufacturers to save money in various aspects, including labor, materials, and overhead costs. For instance, an Enterprise Resource Planning (ERP) system can help maintain inventory levels, reducing costs associated with excess stock or stockouts.
Furthermore, improved forecasting tools assist companies in planning for fluctuations in demand, which prevents costly last-minute adjustments or expedited shipping fees. Investing in the right software results in measurable financial benefits.
Enhanced Collaboration
Enhanced collaboration is another critical benefit that arises from implementing manufacturing software. These systems facilitate better communication between departments such as production, supply chain, and quality assurance. Centralized data ensures that every team member has access to the same relevant information, fostering a culture of collaboration and teamwork.
With shared platforms, teams can quickly exchange updates regarding production schedules, inventory levels, or quality metrics. Such improvements lead to informed decision-making and reduce inefficiencies caused by miscommunication.
Improved Quality Control
Quality control is paramount in manufacturing. Software solutions provide tools for monitoring quality standards consistently. By implementing Quality Management Systems (QMS), businesses can automate quality checks throughout the production processes.
Real-time data reporting allows for immediate identification of anomalies, enabling swift corrective actions. This proactive approach to quality management leads to lower defect rates and increased customer satisfaction, which ultimately affects a company's reputation and profitability.
Data-driven Decision Making
Finally, manufacturing software enhances data-driven decision making. Access to accurate and comprehensive data allows decision-makers to analyze trends, performance metrics, and other critical indicators. These insights are crucial for identifying areas of improvement and fostering innovation.
Being data-driven means companies can pivot strategies as needed, adjust production plans according to market demand, or determine effective cost-cutting measures. The utilization of such analytic capabilities is essential for maintaining competitive advantage in an ever-evolving marketplace.
"Manufacturing software does not just automate tasks; it revolutionizes how decisions are made across the enterprise."
In summary, the benefits of implementing manufacturing software systems are profound and multifaceted. Organizations that adapt to these systems stand to gain operational efficacy, cost reductions, enhanced collaboration, improved quality control, and informed decision-making capabilities.
Challenges in Manufacturing Software Implementation
Implementing manufacturing software systems is not a straightforward process. It involves several challenges that organizations must navigate to ensure successful adoption. Understanding these challenges is vital for decision-makers and IT professionals. They shape the framework for what to expect during implementation, directly influencing how efficiently the software integrates into existing processes. The repercussions of underestimating these challenges can lead to project delays, increased costs, and failed initiatives.
Integration Issues with Existing Systems
One of the most significant hurdles in implementing manufacturing software is integrating it with existing systems. Many organizations use several software applications that operate in silos. Each system may support specific functions like inventory management, order processing, or production scheduling. When new software enters this ecosystem, it is crucial to ensure that it can communicate seamlessly with legacy systems. Failure in integration can lead to data discrepancies, poor analytics, and reduced operational efficiency.
Moreover, legacy systems often lack new features found in modern software. Custom connection interfaces or middleware may be needed to facilitate communication streams. This can add complexity and length to the implementation timeline. A thorough analysis of existing systems must be conducted to create a robust integration plan.
Change Management and User Adoption
Change management is another key aspect that affects the success of software implementation. Employees accustomed to specific tools and processes may resist new systems. The attitude of the workforce towards change significantly influences user adoption. If staff members do not understand the benefits or how to use the new software, it may lead to pushback or misuse.
Training programs become essential in this scenario. They should guide users through the new functionalities and demonstrate the advantages it brings. Ongoing support after the initial rollout can also smooth the transition. Addressing concerns and providing resources fosters a culture of acceptance, easing the worries related to change.
"New tools are only as effective as the people using them."
Ignoring change management strategies can result in a partially utilized or underperforming system, negating the intended benefits of the software.
Cost Overruns and Budget Constraints
Cost overruns are a common concern when implementing manufacturing software. Initial budget estimates may not account for all expenses involved. Issues such as unanticipated integration costs, extended training sessions, or additional licensing fees can inflate overall expenses. If stakeholders do not monitor costs closely throughout the implementation, they may exceed their initial budgets, leading to financial strain.
Setting a realistic budget with a contingency plan is crucial. It is important to consider all aspects: software costs, hardware upgrades, user training, and potential ongoing maintenance. Regular assessments during the process ensure the project stays within budgetary limits.
Evaluating Manufacturing Software Solutions
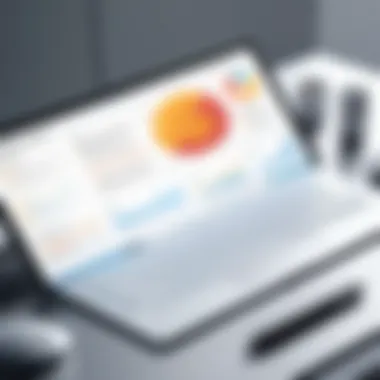
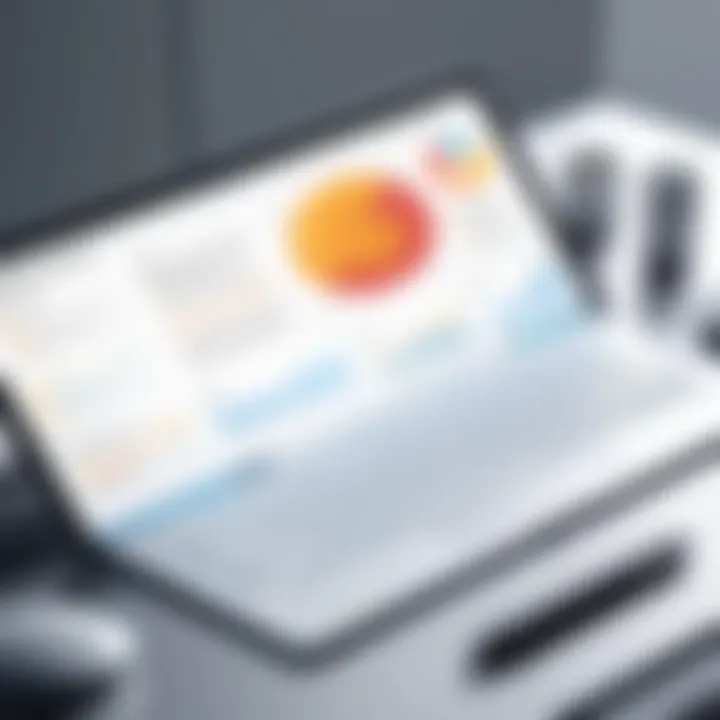
When considering the implementation of manufacturing software, evaluation is a critical step. Proper evaluation ensures that the selected software aligns with the organization's unique operational requirements. This section discusses how to effectively evaluate manufacturing software solutions by highlighting several key elements that matter significantly to decision-makers.
Assessing Business Needs
Before moving forward with any software solution, it is essential to assess specific business needs. Companies should first identify their goals and objectives. Are they looking to increase efficiency, reduce costs, or improve quality control? Each goal may lead to different software requirements.
A comprehensive assessment involves examining current processes, identifying bottlenecks, and determining how software can address those issues. Engaging with different stakeholders during this assessment can provide varied perspectives on what is necessary for operational success. It can be helpful to:
- Conduct interviews with employees from different levels and functions.
- Analyze workflows to pinpoint inefficiencies.
- Review existing systems to evaluate gaps.
This groundwork is crucial. An accurate assessment will guide you to software solutions that meet your needs.
Conducting a Vendor Comparison
Once needs are clearly defined, the next step is to conduct a vendor comparison. Various manufacturers offer a range of software products. The challenge is to find the best fit within that array. Key considerations include:
- Features: Does the software cover all functionalities that the business needs?
- Pricing: Is the vendor's pricing model transparent and does it match your budget?
- Support and Training: What kind of post-implementation support does the vendor offer?
- Scalability: Can the software grow with your business?
Crafting a comparison matrix can assist in evaluating these elements quantitatively. Consider reaching out to multiple vendors for demonstrations to see the software in action, which helps in assessing usability and functionality directly.
Checking User Reviews and Testimonials
User reviews and testimonials are also essential when evaluating software solutions. Real-world feedback from other manufacturers provides insights that cannot always be captured in a sales pitch. Websites like Reddit and Facebook can be useful platforms to find honest reviews. Look for:
- Comments on ease of use.
- Reports on customer service experiences.
- Feedback on performance and reliability.
Analyzing user experiences gives clarity beyond marketing descriptions, helping to discern the actual impact of the software on business processes. Gathering a diverse set of opinions ensures that you make a well-informed decision.
"Thorough evaluation is key to ensuring that manufacturing software solutions not only meet immediate needs but also fit long-term strategic goals."
Future Trends in Manufacturing Software Systems
The landscape of manufacturing software systems is ever-evolving. Staying updated on future trends is critical for decision-makers. By understanding these trends, they can enhance their operational strategies, ensure competitive advantages, and keep pace with industry transformations. Notably, advancements in technology directly influence how manufacturing systems function.
Industrial Internet of Things (IIoT)
The Industrial Internet of Things (IIoT) represents a significant advancement in manufacturing software. It integrates smart devices and machines into production processes. This connectivity enables better data collection. Real-time monitoring of manufacturing systems becomes possible. Through IIoT, businesses can achieve improved efficiency in production. Immediate insights help in minimizing downtime and reducing waste. Additionally, manufacturers can harness predictive maintenance. By monitoring equipment health, they can foresee failures before they occur. This foresight saves costs associated with unplanned maintenance and enhances reliability.
Several companies utilize IIoT to streamline their operations. For example, General Electric employs IIoT technologies in their manufacturing process, resulting in enhanced productivity and reduced operational costs. The application of IIoT is a trend worth noting for managers aiming for longevity in their manufacturing systems.
Artificial Intelligence and Machine Learning Integration
Artificial Intelligence (AI) and Machine Learning (ML) are transforming manufacturing software systems into intelligent solutions. These technologies analyze vast amounts of data quickly. They enable predictive analytics, leading to data-driven decision making. AI’s ability to learn from patterns enhances customization in production processes.
For instance, manufacturers can optimize supply chain management. They can analyze past trends to predict future demands more accurately. This capability reduces excess inventory and improves customer service levels.
Moreover, AI-driven algorithms can assist in quality control. Automated inspection processes allow for consistent monitoring of products. This reduces defects and ensures higher quality in production. Decision-makers must consider AI and ML integration as a crucial trend for future growth.
Cloud-based Solutions
Cloud-based solutions are revolutionizing how manufacturing software is deployed and managed. They offer scalability and flexibility, allowing organizations to adapt to changing demands easily. By storing data on the cloud, manufacturers minimize the risk of data loss and ensure that vital information is accessible from anywhere.
These solutions often come with a subscription model. It reduces the immediate capital expenditure that traditional systems require. Furthermore, cloud-based systems support collaboration across different departments and locations. Teams can work together more efficiently, streamlining processes from engineering to production.
On the other hand, security is a significant concern for cloud adoption. Decision-makers must implement robust security measures to protect sensitive data. However, the advantages often outweigh the risks, making cloud solutions a trending choice for many manufacturers.
"Understanding future trends in manufacturing software systems is essential for maintaining efficiency and competitiveness in the market."
Closure
In closing, the exploration of manufacturing software systems reveals their crucial role in the evolving landscape of production. These systems are more than just tools; they serve as the backbone of modern manufacturing, enabling companies to streamline operations, improve efficiency, and maintain competitiveness. The insights gained throughout this article provide decision-makers, IT professionals, and entrepreneurs with a comprehensive understanding of the importance of implementing the right software solutions.
Summarizing Key Insights
- Diverse Software Types: From ERP to MES, understanding the various types is vital to cater to specific manufacturing needs. Each software category offers unique functionalities that contribute to overall production efficiency.
- Feature Significance: Key features like integration capabilities and real-time data analytics are indispensable. These elements work together to facilitate better decision-making and ensure quality control.
- Benefits Realization: The adoption of manufacturing software can lead to significant operational efficiency, reduced costs, and improved quality control. Understanding these benefits encourages investment in technology.
- Challenges to Address: Recognizing challenges such as integration issues and user adoption barriers can prepare organizations for smoother implementation processes.
"Investing in the right manufacturing software is not simply a technological upgrade; it is a strategic move towards sustaining long-term growth."
Implications for Future Considerations
The future of manufacturing lies in the continued evolution of software systems. With emerging trends like the Industrial Internet of Things (IIoT) and the integration of Artificial Intelligence, manufacturing software will not only advance but redefine the manufacturing sector.
- Technology Integration: As IIoT and AI become mainstream, manufacturers must be proactive in adopting software that can leverage these technologies to enhance productivity and innovation.
- Cloud Solutions: The shift towards cloud-based software solutions offers flexibility and scalability, which are essential for modern manufacturing operations. Companies that embrace this change will benefit from improved collaboration and data accessibility.
- Sustainability Focus: As corporate responsibility becomes increasingly important, software systems that help monitor and optimize resource usage will become essential.
In summary, the right manufacturing software systems are integral to not just operational success but also future competitiveness in a rapidly changing market. Decision-makers must remain vigilant and informed about these systems to ensure they can navigate the complexities of modern manufacturing.