Unlocking Efficiency: Process Manufacturing Software
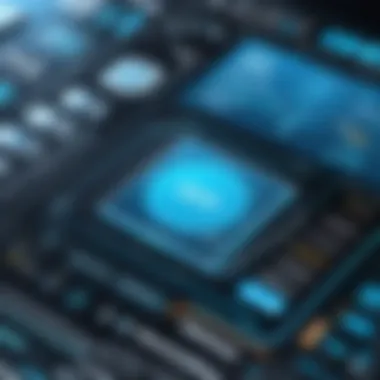
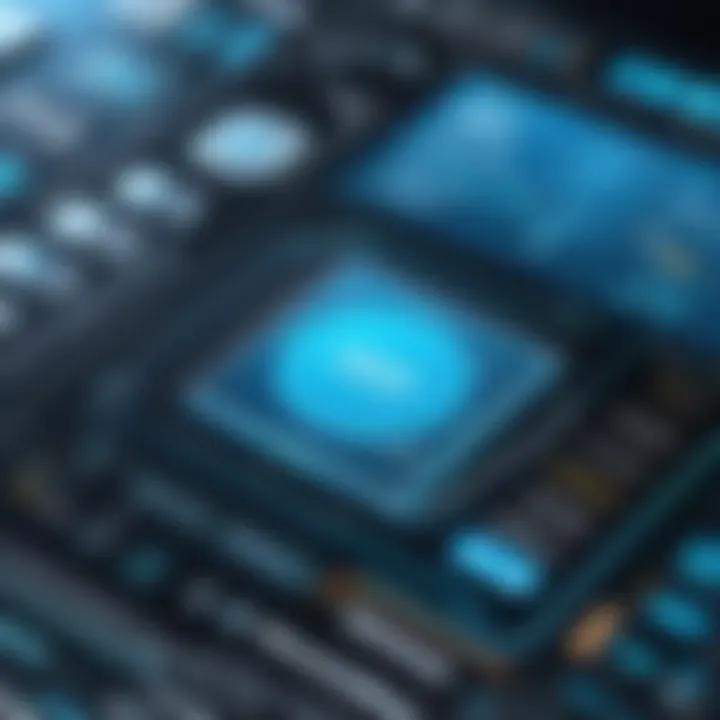
Intro
Process manufacturing software forms a critical component of modern industrial operations. Its significance extends beyond basic task management, impacting efficiency, productivity, and overall operational effectiveness. As industries evolve, the adoption of specialized software tailored to the unique aspects of process manufacturing becomes essential. The nuances of this software encompass everything from inventory management to compliance monitoring, shaping how organizations approach manufacturing challenges.
In this article, we will delve into the essential features, user experience attributes, and forward-looking trends within the realm of process manufacturing software. Understanding these aspects is vital for decision-makers and IT professionals aiming to optimize their manufacturing processes and improve strategic decision-making.
Overview of Core Features
Process manufacturing software possesses a diverse set of functionalities aimed at streamlining operations. Here’s a closer examination of these core features:
- Inventory Management: Keeping track of raw materials and finished goods ensures optimal stock levels, preventing production delays.
- Production Scheduling: Efficiently organizing production runs minimizes downtime and improves resource allocation.
- Quality Control: Built-in quality assurance modules help maintain product standards, reducing waste and recalls.
- Reporting and Analytics: Real-time data analysis supports agile decision-making and strategic planning.
- Regulatory Compliance: Automated compliance monitoring keeps industries aligned with necessary regulations, avoiding potential fines and penalties.
The importance of these features cannot be overstated, as they directly correlate with an organization’s ability to respond swiftly to market fluctuations while ensuring quality and compliance.
Comparison of features across top software options
When selecting process manufacturing software, it is essential to compare the features of various top options. For instance, SAP S/4HANA stands out for its robust analytics capabilities while Oracle Cloud ERP shines for its comprehensive inventory management tools. Meanwhile, Infor CloudSuite offers advanced supply chain visibility, enabling better risk management. Choosing the right software involves evaluating these specialized features against your specific operational needs.
"The choice of software in process manufacturing significantly impacts efficiency and accuracy in operations. A thorough analysis can deliver compelling results."
User Experience and Interface
The design of user interfaces and user experience plays a significant role in the effectiveness of process manufacturing software. A well-designed interface minimizes training time and encourages user adoption.
- UI Design Aspects: Simple, clean layouts with intuitive navigation can aid users in executing tasks swiftly. Clear visualization of data is also crucial for enhancing comprehension and decision-making.
- Usability and Accessibility: Software that supports various devices, including mobile platforms, increases flexibility in operations. Additionally, accessibility features ensure that all users can engage with the software effectively, empowering a broader range of team members.
In summary, the efficiency of process manufacturing software is deeply intertwined with both functionality and user experience. Decision-makers must prioritize these factors when implementing solutions to achieve optimized performance in their operations.
Understanding Process Manufacturing
Understanding process manufacturing is essential to grasp the technological advancements within modern industry. This segment lays the foundation for discussing how software can enhance these operations. Process manufacturing refers to the production methods where goods are produced through a continuous flow of materials. This is as opposed to discrete manufacturing which involves assembling distinct items. Industries such as food and beverage, chemicals, and pharmaceuticals heavily rely on this approach.
Definition and Scope
Process manufacturing is defined as the method of producing goods by combining raw materials through various methods. It encompasses a broad range of industries that focus on transforming bulk substances into finished products. The scope of process manufacturing is significant. It includes not only the materials used but also the techniques utilized, such as chemical reactions, mixing, heating, and cooling. Understanding this scope aids businesses in recognizing the intricate dynamics of their operations.
This approach leads to several advantages. For instance, continuous production allows for greater efficiency and consistency in product quality. Additionally, the ability to monitor processes in real-time can lead to improved decision-making and reduced waste.
Key Characteristics of Process Manufacturing
There are several key characteristics that define process manufacturing. Firstly, it often involves the transformation of materials in bulk. This can include liquid, gas, or powder forms. As a result, this production can necessitate precise control systems to monitor various conditions like temperature and pressure.
Secondly, process manufacturing is typically regulated by rigorous standards. Industries such as pharmaceuticals and food production must comply with specific safety and quality regulations.
Another important feature is the reliance on integrated systems. Successful process manufacturing may utilize advanced software solutions to manage operations, track materials, and ensure compliance with regulations. This integration becomes vital when considering the complexity of large-scale production processes.
Significance of Software in Process Manufacturing
In the complex landscape of modern industry, the significance of software in process manufacturing cannot be understated. Process manufacturing relies heavily on software solutions to facilitate operations, improve productivity, and respond to market demands. The integration of advanced software systems enhances various aspects of manufacturing, offering benefits that range from operational efficiency to stringent quality control, which are critical in maintaining competitiveness in the industrial field.
Enhancing Operational Efficiency
Operational efficiency sits at the core of any manufacturing business. By leveraging process manufacturing software, companies can streamline workflows and minimize waste. The automation of routine tasks reduces manual interventions, which often lead to human errors.

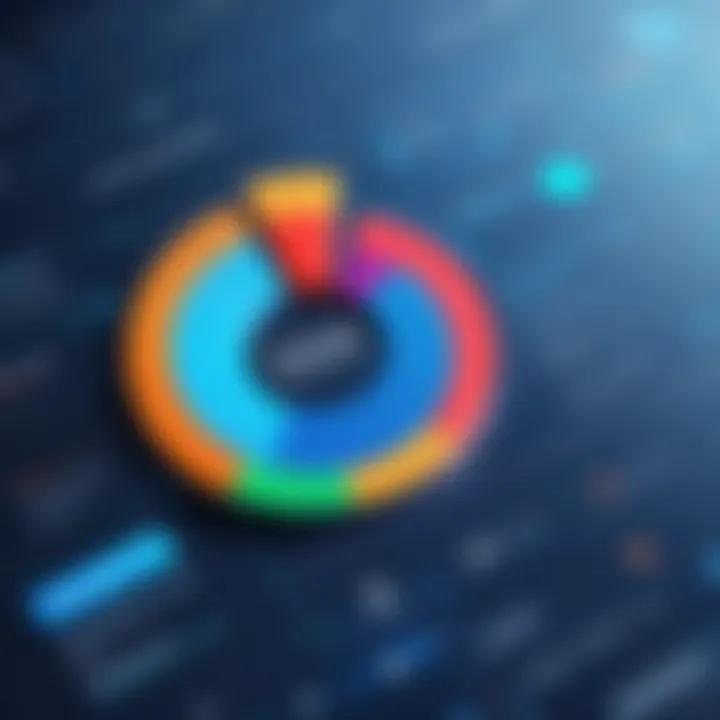
Key benefits include:
- Real-Time Data Access: Operators and managers can access essential data in real time. This immediacy aids in quick decision-making and swift response to production issues.
- Resource Optimization: Software enables better tracking of raw materials and inventory. This optimization leads to cost savings as it helps prevent overstocking or stockouts.
- Enhanced Production Scheduling: Advanced algorithms within manufacturing execution systems can create optimal schedules that maximize resource utilization, effectively balancing workload across different machine centers.
The result is a more agile manufacturing process. Companies can adapt more easily to changes in consumer demand or operational constraints. The interconnectivity of systems facilitates seamless communication between departments, ensuring that production adjusts dynamically to the overall business strategy.
Improving Quality Control
Quality is a fundamental aspect of process manufacturing. In industries such as pharmaceuticals, food production, and chemicals, quality assurance is not just beneficial but often a regulatory requirement. Software tools play a vital role in ensuring quality standards are met consistently throughout the production cycle.
Important aspects include:
- Automated Data Recording: Software systems allow for automated data collection during production. This ensures accurate records that are crucial for audits and regulatory compliance.
- Statistical Process Control: Advanced software can implement statistical methods to monitor production quality. This helps in identifying trends or issues before they escalate, enabling timely interventions.
- Tracking and Traceability: In process manufacturing, being able to trace components back to their origin is essential. Software provides traceability, which enhances transparency and accountability in the production process.
"Quality assurance is not a cost; it’s an investment in future business sustainability."
Types of Process Manufacturing Software
Understanding the various types of process manufacturing software is vital for businesses aiming to optimize their operations. Each software category addresses specific needs within the manufacturing process, enabling organizations to enhance efficiency, productivity, and quality in their operations. Recognizing the distinct functionalities of these systems is crucial for decision-makers to select the most suitable software for their particular context and challenges.
Enterprise Resource Planning (ERP) Systems
Enterprise Resource Planning (ERP) systems play a central role in integrating various functions across an organization into a single cohesive system. These systems provide a unified database that enhances data accuracy and accessibility. They streamline processes such as finance, human resources, and supply chain management, ensuring that all departments operate with real-time information.
The benefits of ERP systems include improved resource allocation and reduced operational costs. By consolidating data, firms can make better-informed decisions, which lead to enhanced productivity. For instance, with ERP, inventory levels can be optimized based on real-time demand forecasting, thereby minimizing waste and excess stock.
However, implementing an ERP system can be challenging. Organizations must carefully consider factors such as scalability and system compatibility with existing processes. Transitioning to an ERP solution requires thorough training of staff and adequate support to ensure effective use.
Manufacturing Execution Systems (MES)
Manufacturing Execution Systems (MES) serve as a crucial link between the production floor and business operations. They provide real-time monitoring and control of manufacturing processes. MES helps track production activities, ensuring that operations align with scheduled plans and provide visibility into production metrics.
The critical importance of MES lies in its ability to enhance production efficiency, reduce cycle times, and ensure compliance with quality standards. For example, plant managers can use MES to detect process variances early, which allows for timely adjustments that prevent significant production issues. This capability is essential for maintaining high levels of production quality and efficiency.
Nonetheless, deploying an MES comes with its own set of challenges. These include integration with existing systems, data overload, and the need for continuous process improvement. The organizational culture must also support the shift toward a data-driven approach, making change management essential in this transition.
Quality Management Software
Quality Management Software (QMS) focuses on maintaining high standards across all manufacturing processes. It ensures compliance with industry regulations and internal quality benchmarks. Through features that allow for documentation, tracking, and auditing, QMS helps organizations to systematically manage and improve quality over time.
One significant advantage of QMS is its ability to facilitate continuous improvement. By analyzing data and trends, organizations can identify areas for enhancement. For example, corrective actions can be promptly implemented when quality issues are detected, thereby minimizing the risk of non-compliance or customer dissatisfaction.
However, simply adopting a QMS is not enough. Organizations need to create a culture that prioritizes quality and invest in staff training to maximize the benefits of the software. Furthermore, selecting a QMS that aligns with specific operational needs is critical.Having thorough vendor evaluations and user feedback mechanisms can aid in making the right choice.
Key Features to Consider
Considering the vast landscape of process manufacturing software, it is crucial to identify the key features that dramatically impact efficiency and productivity. These features can differentiate between a system that meets business needs and one that falls short. A well-rounded evaluation is crucial to ensure that the software aligns with operational goals.
Data Integration Capabilities
Data integration capabilities stand as a cornerstone for process manufacturing software. In a complex operational environment, the ability to amalgamate data from various sources is vital. Integration allows for consistency in data accessibility and use across the organization. When various systems align seamlessly, decision-makers can analyze comprehensive data sets, leading to more informed strategies.
Investing in software that boasts robust integration capabilities means that organizations can link ERP systems, MES, and other tools directly, reducing data silos. This ultimately enhances visibility into manufacturing processes, boosts collaboration among departments, and fosters real-time decision-making.
Real-Time Monitoring and Reporting
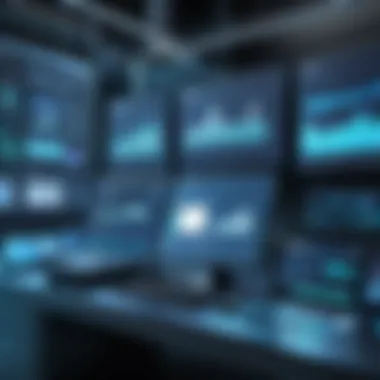
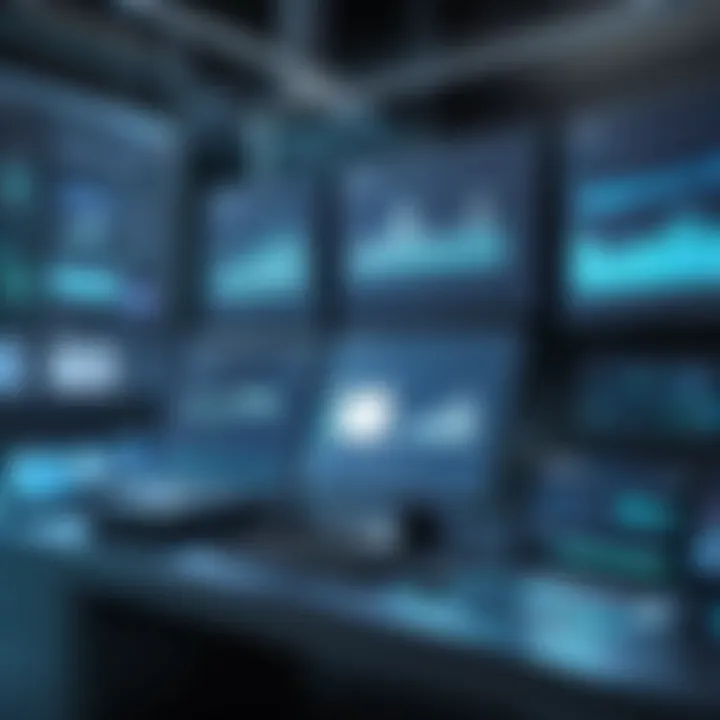
In modern industry, the necessity for real-time monitoring cannot be overstated. Process manufacturing software that facilitates immediate visibility into operations allows managers to track performance metrics, detect issues promptly, and respond effectively. Analytics features generally include dashboards displaying critical KPIs related to production efficiency, equipment uptime, and material usage.
Real-time reporting provides more than just data; it offers insights that can drive performance improvements. Metrics can be evaluated live, allowing businesses to pivot strategies or operational tactics as necessary. This capability is essential for maintaining competitive advantages in a rapidly evolving marketplace, enabling proactive rather than reactive management.
Scalability and Customization Options
Scalability and customization are key considerations when selecting process manufacturing software. As organizations grow, their operational needs evolve. A scalable solution allows businesses to expand functionality without overwhelming existing systems or requiring expensive replacements.
Moreover, customization options further empower organizations to tailor the software to fit unique processes or industry specifications. Custom functionalities can include specific reporting features, unique workflows, or integrations with niche equipment. Such flexibility ensures that the software can adapt over time, aligning with business growth and industry trends.
Implementation Challenges
Implementing process manufacturing software can yield significant benefits, but it also incurs challenges that organizations must navigate effectively. Recognizing these hurdles is crucial, since they can impact both the timeline and overall success of the software deployment. Addressing factors like cost, change management, and the requirements for training and support are all essential components of a successful implementation strategy.
Cost Considerations
Cost is often the primary barrier for companies considering process manufacturing software. The investments required can be substantial, encompassing licensing fees, hardware costs, and system integration expenses. Moreover, ongoing maintenance costs can add to the financial burden.
When budgeting for software implementation, organizations should consider both direct and indirect costs. Indirect costs, which may not be immediately apparent, include potential downtimes during the transition phase and the costs associated with lost productivity if the software is not integrated properly. To mitigate financial risks, it is advisable to conduct a thorough cost-benefit analysis. This analysis can guide decision-makers in understanding the total cost of ownership over time versus the projected gains in efficiency and productivity.
Change Management Issues
Change management is another critical aspect of successful software implementation. Employees often resist changes to established routines, and this resistance can lead to conflicts and decreased morale. Effective change management includes clear communication regarding the reasons for the transition and the expected outcomes.
Encouraging team involvement during the implementation process can also facilitate smoother transitions. Involving employees in discussions about how the new software will impact their roles can reduce uncertainty and foster a sense of ownership. Training sessions can be implemented to address concerns and highlight the benefits of the software, aiding in the adoption and reducing pushback from staff.
Training and Support Needs
Providing adequate training and support is paramount for successful software implementation. The complexity of process manufacturing software often demands a steep learning curve. Organizations should design tailored training programs catering to varying levels of expertise within staff.
Support needs extend beyond initial training. Continuous support systems are essential, as employees will have ongoing questions and require assistance as they adapt to the new tools. Establishing a support framework, comprising help desks, documentation, and regular check-ins, can ensure team members feel supported throughout the transition.
Overall, tackling these implementation challenges requires strategic planning and a proactive approach. By acknowledging and addressing cost factors, change management, and training, organizations can foster a smoother integration of process manufacturing software into their operations.
Best Practices for Software Selection
Selecting the right process manufacturing software is critical for organizations aiming to optimize their manufacturing operations. This section focuses on the best practices involved in choosing the most suitable software. Adhering to these practices can lead to improved productivity, lower operational costs, and enhanced decision-making.
Conducting a Needs Assessment
A comprehensive needs assessment is the foundational step in software selection. It involves analyzing the specific requirements of the organization, including production goals, budget constraints, and existing system integrations. This process entails gathering information from various departments such as production, quality control, and logistics.
Key elements to consider during the assessment include:
- Functional Requirements: Identify essential features like inventory management, scheduling, and compliance tracking that align with business objectives.
- Technical Infrastructure: Evaluate current IT resources and compatibility with potential software solutions.
- User Adoption: Assess the ease of use and accessibility for staff at different levels.
By carrying out a thorough needs assessment, organizations can ensure they choose software that not only meets immediate demands but also supports future growth.
Evaluating Vendor Offerings
Once the needs assessment is complete, the next step is evaluating various vendors' offerings. Each vendor may propose different features and pricing. Therefore, a matrix comparing solutions can be very beneficial. Consider the following factors:
- Reputation and Reliability: Research vendor reviews and reliable sources for performance insights.
- Customization Flexibility: Determine if the software can be tailored to meet unique organizational needs.
- Support and Maintenance: Inquire about ongoing technical support and software updates post-implementation.
- Cost Transparency: Ensure that all costs are clear, including initial setup and ongoing fees.
This evaluation process helps reduce risks associated with vendor selection and enhances organizational confidence in their choice.
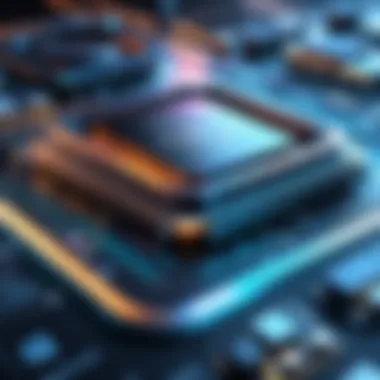
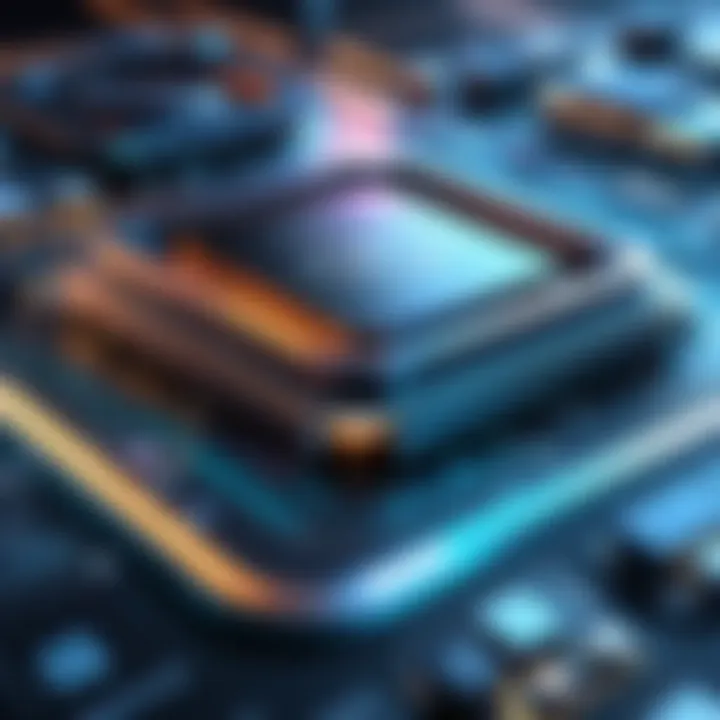
Seeking User Feedback
Incorporating user feedback into the decision-making process is vital. This step ensures that software solutions resonate well with end-users who will interact with the system on a daily basis. Engaging users early can yield valuable insights about functionality and ease of use. Consider these approaches:
- Conducting Surveys: Gather data from potential users regarding their preferences and pain points with current systems.
- Organizing Demos: Encourage team members to participate in product demonstrations to evaluate the user interface and features comprehensively.
- Pilot Testing: If feasible, run pilot programs with selected software solutions to gather real-time feedback before full-scale implementation.
"User involvement in software selection increases the likelihood of successful adoption and maximizes return on investment."
Actively seeking and responding to user feedback positions an organization for greater satisfaction with the new software.
When software selection is approached methodically, organizations set the stage for an effective implementation that enhances operational efficiency. Following these best practices can significantly streamline the selection process and yield long-term benefits.
The Future of Process Manufacturing Software
The landscape of process manufacturing is evolving rapidly, shaped by advancements in technology and shifting market demands. The future of process manufacturing software holds significant promise for optimizing operations and delivering greater efficiencies. Understanding the emerging trends and technologies is essential for decision-makers, IT professionals, and entrepreneurs as they navigate through this complex industry.
Emerging Technologies
Innovations such as the Internet of Things (IoT) and advanced data analytics are paving the way for smarter manufacturing processes. IoT, in particular, allows devices and machines to communicate with each other, providing real-time data that can enhance decision-making. This integration of devices can lead to better monitoring of production lines, reducing downtime and increasing productivity. Moreover, data analytics tools are becoming essential as businesses gather large volumes of data. These tools help in identifying patterns and insights that can inform production strategies.
Key Technologies to Watch Out For:
- IoT Systems: Enhancing communication between machines.
- Artificial Intelligence (AI): Improving predictive maintenance and operations.
- Augmented Reality (AR): Assisting in training and maintenance procedures.
Sustainability and Environmental Impact
Sustainability is no longer just a buzzword; it is a fundamental consideration for modern manufacturing. The future of process manufacturing software must focus on reducing environmental footprints and complying with regulations. Technologies that monitor energy consumption and resource usage will be vital. Software solutions that integrate sustainability metrics into daily operations can help organizations minimize waste and optimize resource use.
Benefits of Sustainable Software Solutions:
- Lower Operational Costs: Reducing waste often leads to saving money.
- Regulatory Compliance: Staying ahead of environmental regulations is crucial.
- Brand Image: Aligning with sustainability can boost reputation and customer loyalty.
AI and Automation in Manufacturing
Artificial Intelligence and automation are transforming how manufacturers operate. Predictive analytics powered by AI can foresee equipment failures before they occur, allowing for preemptive repairs and minimal operational disruption. Automation streamlines repetitive tasks, allowing human workers to focus on more complex and value-added operations. The integration of AI into process manufacturing software represents a significant leap towards autonomous manufacturing.
Advantages of AI and Automation:
- Enhanced Efficiency: Reducing time spent on manual processes.
- Improved Accuracy: Lowering the chance of human error in production.
- Scalability: Adjusting production levels according to demand with ease.
"The future is not something we enter. The future is something we create."
— Leonard I. Sweet
As industries move forward, the relationship between process manufacturing software and emerging technologies will become increasingly intricate. The consideration of sustainability and the application of AI will dominate discussions into the coming years. Manufacturers must embrace these changes to remain competitive and innovative in an ever-evolving market.
Finale
The conclusion section provides a pivotal perspective on the significance of process manufacturing software in modern industrial practices. This article has dissected various aspects of the technology, imparting crucial information about its implementation and effectiveness. The following highlights summarize the essential points.
Recapitulation of Key Points
- Understanding the Landscape: Process manufacturing is characterized by its unique requirements and processes. Recognizing these traits is essential to unlocking the full potential of software solutions.
- Software Importance: Emphasizing the role of software in enhancing operational efficiency and quality control demonstrates the tangible benefits of digital integration.
- Diverse Types of Software: Different systems such as ERP, MES, and Quality Management Software serve various needs within process manufacturing, highlighting the importance of tailored solutions.
- Implementation Challenges: Addressing cost considerations, change management, and the need for training can significantly ease the transition to new software.
- Best Practices: Conducting thorough needs assessments and evaluating vendor offerings ensures a more informed selection process for industry stakeholders.
- Future Trends: Technologies like AI and sustainability considerations are evolving, shaping the future of process manufacturing and offering new opportunities for innovation.
Implications for Industry Professionals
For decision-makers, IT professionals, and entrepreneurs, understanding process manufacturing software is no longer optional; it is essential for survival and growth in a competitive landscape. The interplay of software capabilities and manufacturing processes allows for:
- Informed Decision-Making: Having the right data and reporting features enables better resource allocation, ultimately driving profits.
- Competitive Advantage: Companies that implement these systems effectively can outperform competitors who utilize outdated practices and tools.
- Alignment with Trends: Staying aware of emerging technologies ensures that organizations can adapt swiftly to changes in market demands.
"In today's fast-paced industrial environment, the strategic integration of process manufacturing software is not just beneficial but imperative."
Developing a deep comprehension of these elements fosters a more adept, agile workforce that is prepared to meet the demands of modern industry. Engaging with this topic is invaluable for professionals aiming to position their organizations at the forefront of innovation.