The Role of Shop Work Orders in Enhancing Efficiency
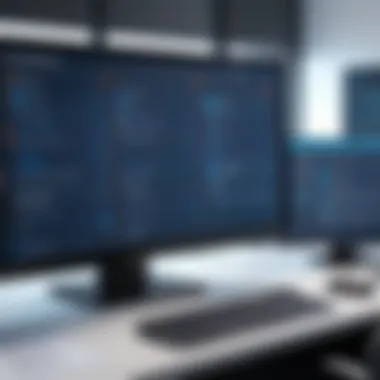

Intro
In the fast-paced world of manufacturing and service industries, operational efficiency isn't just a buzzword; it's a necessity. Among the myriad of processes that contribute to streamlined operations, shop work orders hold significant weight. They serve as the backbone through which tasks are organized, prioritized, and monitored. It's easy to overlook the systematic nature of work orders when they're taken for granted, but they are much more than just forms or checklists. They embody the processes that keep workflows smooth and accountable.
Properly managed shop work orders bring clarity to daily operations. They help ensure that resources are allocated correctly and that tasks are completed on time. Without them, the chaos can quickly spiral out of control, leading to missed deadlines, underutilized resources, and frustrated staff.
Let's unfold this exploration of shop work orders, starting with their core features that serve as the foundation for operational success.
Overview of Core Features
Description of Essential Functionalities
At their core, shop work orders are designed to organize tasks effectively. Each work order contains vital details, such as:
- Task descriptions: Clear outlines of what needs to be done.
- Priority levels: Indications of which tasks are urgent or important.
- Resource allocations: Information on personnel, equipment, or materials needed.
- Timeframes: Deadlines for completion and estimated times for tasks.
These functionalities work together to create an organized approach for managing workloads. This organization brings in the potential for better communication among team members. When everyone knows their responsibilities and timelines, there’s less room for misunderstanding or errors.
Comparison of Features Across Top Software Options
Not all work order management tools are created equal. Each comes with its own set of features, making some better suited for certain industries than others. Here’s a glimpse of what you might typically find in popular solutions like JobBOSS, Release, or Fishbowl:
- JobBOSS: Offers highly customizable templates that allow businesses to tailor their work orders to specific needs, making it ideal for manufacturers.
- Release: Known for its user-friendly interface, it helps service providers to easily track service requests and customer interactions seamlessly.
- Fishbowl: Integrates inventory management directly into its work order system, bridging gaps between production planning and stock management.
Each of these platforms highlights the critical requirement for flexibility and adaptability in managing shop work orders. Depending on the specific operational requirements, the choice of software can dramatically impact efficiency.
Insights into UI/UX Design Aspects
User experience plays a crucial role in how effectively a work order system gets deployed. If the interface is cluttered, or if key functions are hard to find, team members are likely to struggle rather than thrive. A good user interface is characterized by simplicity, clarity, and intuitive navigation. Ideally, it should allow users to generate work orders swiftly, making it easy to update and track progress.
Importance of Usability and Accessibility
Furthermore, in today’s diverse workplace, accessibility cannot be ignored. It’s essential to consider that employees may have different needs based on their roles and technological familiarity. An intuitive design isn’t just a luxury; it fosters an inclusive environment where everyone can contribute effectively. The ability to quickly learn the system and access information from various devices improves task efficiency and minimizes delays.
In summary, the importance of shop work orders as an engine for operational efficiency is manifold. They contribute to structured task management, enhance team communication, and determine the most suitable tools for unique operational demands. Understanding these core aspects prepares businesses to optimize their workflows and increase productivity.
Understanding Shop Work Orders
Understanding shop work orders is essential for any organization seeking to optimize its operations and boost efficiency. Work orders act as a roadmap, guiding tasks from inception to completion. They ensure that everyone is on the same page and minimize confusion that can lead to costly delays. These documents are not just forms; they carry significant weight in how business processes are executed.
Definition and Purpose
A work order can be defined as a formal document that outlines specific tasks to be performed, usually within a set timeframe and budget. Primarily, its purpose is to communicate what needs to be done, who will do it, and the resources required to complete the job. In a manufacturing environment, for instance, a work order might specify that a particular machine requires maintenance. It includes details such as the parts needed, the estimated time for repair, and the personnel assigned.
Benefits of Work Orders:
- Clarity: They eliminate guesswork, defining exact responsibilities.
- Tracking: Allows for meticulous tracking of tasks, leading to improved accountability.
- Resource Allocation: Helps in planning the necessary resources, averting waste or shortages.
There is much to gain from implementing organized work order systems. They provide not merely a sense of direction but also cultivate accountability across teams. In essence, efficiently managed work orders can improve communication and collaboration, ultimately enhancing overall productivity.
Evolution of Work Orders
Work orders have come a long way from their origins. Traditionally, they were simple documents, often handwritten, that communicated basic task instructions. As industries expanded and technology progressed, they evolved into more complex formats. The initial focus on just the task itself burgeoned into a comprehensive ecosystem that includes tracking, resource management, and analytics.
In today’s world, digital transformation has revolutionized how work orders are created, managed, and executed. Software platforms now enable seamless integration between various systems, allowing businesses greater visibility into their operations.
Some key developments in this evolution include:
- From Manual to Digital: The shift from paper-based processes to digitized solutions has saved countless hours.
- Integration with Inventory Management: Work orders can now automatically trigger inventory management systems, ensuring necessary materials are in stock.
- Real-time Monitoring: With IoT and other technologies, managers can monitor work orders in real-time, adjusting schedules as required to optimize workflow.
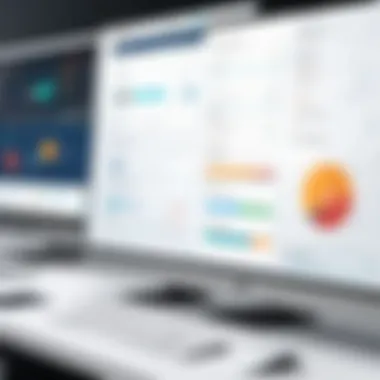

Understanding how work orders have evolved helps stakeholders recognize the potential they hold today. As systems and technologies continue to progress, more robust methodologies surrounding work orders will emerge, establishing them as prioritised tools in operational efficiency.
Key Components of a Work Order
Understanding the key components of a work order is crucial for achieving operational efficiency in various sectors. These components not only help in maintaining clarity but also enhance accountability among team members handling tasks. The process of creating and managing work orders becomes more streamlined when specific elements are properly defined and utilized. The significance of these components lies in their ability to facilitate communication, ensure resource allocation, and support effective project management.
Identifying Information
The identifying information in a work order serves as the backbone for project tracking and accountability. This includes details such as:
- Work Order Number: A unique identifier for each work order, which helps in referencing and tracking progress.
- Creation Date: Indicates when the order was issued.
- Contributor and Assignee Details: Names and roles of those responsible for carrying out the work.
By having precise identifying information, it becomes easier for managers to oversee operations. It can prevent confusion when multiple tasks are being handled simultaneously. Imagine looking for that one needle in a haystack; without proper identification, you simply might not find it.
Description of Work
Next in line is the description of the work to be done. This section lays out the specifics of the task at hand. A well-articulated description might include:
- Scope of Work: Clearly defines what is included in the task along with any exclusions.
- Objectives: What the task aims to achieve.
- Steps Involved: Detailed outlines of how the work will be accomplished.
A precise description ensures that everyone involved understands what needs to get done. It minimizes the chances of miscommunication, which can lead to delays and increased costs. You wouldn't set out on a long road trip without a map, so why approach a project without a comprehensive description?
Materials and Resources Required
Every task under a work order requires specific materials and resources, which can significantly affect timeliness and cost-efficiency. This section generally includes:
- List of Materials: Detailed enumeration of all items needed to complete the task.
- Personnel Involved: Identifies which team members will be needed and their specific roles.
- Equipment Required: Details the machinery or tools necessary for the task.
By meticulously listing materials and resources, companies can ensure that everything is on hand before work begins, saving time and avoiding interruptions. Think of it like cooking a complex dish; if you don’t gather all your spices first, you’ll get caught in the hustle of running around when you’re in the middle of cooking.
Time Estimates and Scheduling
Effective time management is essential for operational success. In this section, time estimates and schedules are typically outlined as follows:
- Estimated Time for Task Completion: A realistic timeframe for how long the task should take.
- Milestones: Key points in the project timeline to measure progress.
- Due Dates: Final deadlines for task completion.
A well-planned schedule serves as a roadmap that can help teams stay on track. When deadlines are communicated clearly, it fosters accountability among team members and reduces the likelihood of project overruns. It’s like setting a goal in a race; without checkpoints, it’s easy to lose your way and slack off.
"In a fast-paced environment, knowing exactly what to do and when to do it is not just an advantage; it’s a necessity."
By attending to these key components, organizations can sharpen their operational efficiency, reduce errors, and improve overall productivity. This clarity regarding work orders becomes invaluable, as it helps businesses respond effectively to challenges and capitalize on opportunities.
Process of Creating a Work Order
Understanding the process of creating a work order is crucial for enhancing operational efficiency. A well-structured work order lays a solid foundation for a successful project. It ensures that tasks are systematized, resources are properly allocated, and everyone involved is on the same page. By focusing on key elements—such as initiating requests, review processes, and final assignment—we create a seamless workflow that can substantially reduce delays and misunderstandings.
Initiating the Request
The first step in creating a work order is gathering the necessary input to initiate the request. Generally, this involves the person requiring the service—like maintenance or production—submitting a detailed request to the relevant department. It's essential to capture specific details right from the start, such as the nature of the work, urgency, and desired completion date. This clarity helps prevent misunderstandings later on.
For instance, a technician might request repairs on a piece of machinery by filling out a form that includes the machine's model, the exact issue, and any relevant history. This sets a clear benchmark for what needs to be accomplished.
Review and Approval Stages
Once the request is submitted, it generally goes through a review and approval phase. This stage is not merely a formality; it acts as a filtration system, ensuring that only the most relevant and necessary tasks are taken forward.
During this phase, multiple stakeholders may need to weigh in—from managers to finance departments—to check if resources are available and if the work aligns with broader organizational goals. This collaborative nature helps foster cross-departmental communication, which can expose other pressing needs that might affect overall efficiency.
It's better for all parties if the work order is vetted thoroughly upfront to avoid costly modifications down the line.
"A stitch in time saves nine". This old saying couldn't ring truer here; catching issues early can save significant time and effort later.


Assigning the Work Order
The final step in creating a work order involves assigning the task to the appropriate personnel. Once the work order is approved, it is typically assigned either to individuals or teams based on their skills and availability. This is a critical juncture, as the success of the project often hinges on the qualifications of those chosen.
In organizations that utilize enterprise resource planning (ERP) systems, assigning a work order is often automated, allowing for real-time updates and tracking. It's not just about who does the work, but also how effectively it is managed during the execution phase.
A well-structured assignment means everyone knows their roles and timelines, minimizing confusion and the risk of overlapping responsibilities.
In closing, the process of creating a work order involves careful planning and communication. Each element plays a vital role in ensuring that work is initiated, approved, and executed smoothly. By following these steps, organizations can bolster their operational efficiency, making it easier to achieve their goals.
The Role of Technology in Work Order Management
In today’s fast-paced business world, leveraging technology for work order management has become an essential part of operational efficiency. The implementation of technology speeds up processes and minimizes errors in various industries. Without doubt, technological advancements have transformed traditional workflows and enhanced productivity, effectively acting as a backbone for managing shop work orders.
Software Solutions Available
Organizations have a plethora of software solutions at their disposal for managing work orders. From specialized programs to cloud-based systems, these tools simplify the entire process. Some well-known software includes:
- SAP: This enterprise resource planning software integrates work orders with comprehensive project management features, enabling seamless tracking from initiation to completion.
- Trello: Simple and adaptable, it enhances visibility for teams on various tasks while giving room for customizability.
- Airtable: Combines the functionality of spreadsheets and databases, making it easy to track work orders and collaborate internally.
- Monday.com: Offers robust project management tools, enabling teams to plan, track, and optimize tasks in a visual manner.
Moreover, using mobile applications enables workers in the field to access work orders, report progress, and communicate effectively with their teams. This real-time update mechanism mitigates a lot of confusion that may arise between office and on-site workers.
Integration with Other Systems
The true power of software tools lies in their ability to integrate with existing systems within an organization. This integration can lead to monumental positive changes in managing work orders, making everything run smoother. When work order management software is connected to inventory management, customer relationship management (CRM), and financial systems, the result is a linear flow of valuable data.
For instance, when an inventory management system updates stock levels automatically after a work order is fulfilled, it decreases the chances of shortages. Similarly, connecting work orders with CRM systems allows businesses to keep track of customer inquiries and service requests linked to work orders.
In addition, cloud-based platforms aid in provision of accessibility to data from anywhere. This breaks down silos within organizations, allowing for clearer communication and proactive decision-making across departments.
"Utilizing technology for work order management represents not just an upgrade but a complete evolution in operational efficiency."
In summary, integrating technology into work order management facilitates not only streamlined processes but also fosters collaboration and enhances productivity. As the business landscape continues to evolve, embracing innovation in work order management remains a key advantage for companies aiming to thrive in a competitive environment.
Benefits of Organized Work Order Management
The effectiveness of organizational operations often hinges on how well tasks are defined and executed. This is especially true when discussing the management of shop work orders. By streamlining the processes involved in work orders, businesses can witness a cascade of benefits that enhance overall operational efficiency. The vitality of a structured approach cannot be overstated, particularly in minimizing misunderstandings and maximizing output.
Improved Communication
When work orders are clearly organized, communication among team members takes on a new, clearer form. Think about it: when everyone knows what the plan is, questions reduce significantly. For example, imagine a manufacturing setting where there is a muffled exchange of emails about equipment repair. Without a structured work order, the likelihood of missing critical details amplifies. However, if the work order lays out every detail—task descriptions, responsible personnel, and timelines—every team member can navigate their responsibilities with precision.
Furthermore, having a clear format for work orders allows for quicker updates. Any changes can be communicated in real time, ensuring that everyone is on the same page. This improvement in communication directly contributes to efficiency. It's like the wheels of a well-oiled machine; if they turn smoothly, everything flows better.
Enhanced Productivity
A well-structured work order system doesn't just keep things organized; it elevates productivity to new heights. The rhythm of a busy shop can often resemble a chaotic orchestra if communication and tasks aren't well managed. Streamlined work orders set the tempo for this orchestra, guiding each musician on when to play their part. When tasks and responsibilities are articulated with clarity, workers can dive straight into their roles without being bogged down by confusion.
Moreover, having a systematic method to track progress allows managers to identify bottlenecks in real-time. If a particular task is taking longer than expected, it raises a flag—giving managers the opportunity to intervene early rather than dealing with a jam further down the line. When processes are streamlined, workers can focus on doing their best rather than wondering what needs to be done next.
Resource Optimization
Efficient work order management also plays a significant role in resource optimization. Each work order outlines the materials and resources required for a task. When organized well, this helps ensure that resources are used judiciously and reduce wastage. For instance, consider a situation in a repair shop—if each work order specifies the parts needed for a vehicle, it helps in planning inventory requirements better. No more scrambling for parts last minute or over-ordering supplies that gather dust in the back.
Additionally, optimized work orders allow for a smoother allocation of human resources. Team members can be assigned based on their strengths and availability, leading to a more balanced workload. If one individual is struggling under a pile of assignments, it's easier to redistribute tasks when everyone knows who is responsible for what. This approach not only maximizes productivity but also contributes to a more harmonious work environment.
In summary, organized work order management serves as a cornerstone for effective communication, heightened productivity, and efficient resource utilization. By implementing best practices around work orders, industries can transition from chaos to coherence, ultimately driving operational success and an enhancing the bottom line.
Challenges in Work Order Management
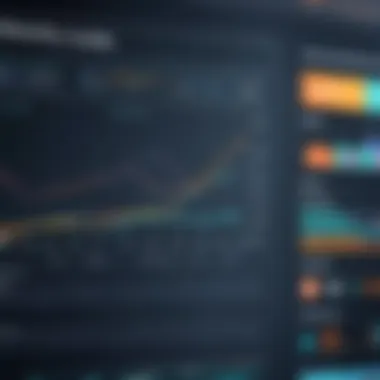

Managing work orders is no walk in the park. As businesses strive for operational efficiency, it's paramount to recognize the challenges that arise in work order management. These hurdles can impact productivity, lead to miscommunication, and create a cascade of inefficiencies that can ripple through an organization. Acknowledging these challenges not only helps in mitigating risks but also improves overall workflow. Here are some essential elements to consider while navigating this complexity:
- Inadequate Communication: A breakdown in communication often leads to misunderstanding work order requirements. Employees might miss important details, causing delays in completion. Clarity is key.
- Lack of Standardization: Without a unified process for creating and executing work orders, variations can emerge. These inconsistencies can lead to confusion among teams, resulting in mistakes and rework.
- Data Overload: In an effort to track everything, organizations can find themselves drowning in data, making it difficult to focus on what's truly important. Sorting through excessive information can bog down decision-making.
"Streamlining processes is about clarity, precision, and the ability to focus on priorities."
Recognizing these challenges equips decision-makers with the insight needed for effective management.
Common Pitfalls to Avoid
When it comes to work order management, avoiding common mistakes can be the difference between smooth sailing and a bumpy ride. Some pitfalls include:
- Neglecting Documentation: Failing to keep accurate and up-to-date records can lead to severe gaps in understanding project requirements and expectations.
- Ignoring Team Feedback: Employees on the ground often have valuable insights. Disregarding their input can hinder improvements in work order processes.
- Overburdening Employees: If too many work orders are assigned at once, staff may feel overwhelmed. This can lower morale and productivity.
By steering clear of these pitfalls, organizations can enhance their operational efficiency.
Dealing with Overlapping Orders
Another major hassle in work order management is the phenomenon of overlapping orders. When multiple orders converge, confusion typically follows. Here are a few strategies to tackle this issue:
- Prioritizing Orders: Clearly defining which orders take precedence can reduce conflicts and streamline workflow.
- Utilizing Technology: Modern software tools can help track and manage work orders efficiently. Automation can minimize human error and enhance clarity.
- Regular Review Meetings: Holding frequent check-ins can help teams resolve overlapping issues on the fly. Open discussions foster problem-solving and maintain focus on the task at hand.
Through effective management of overlapping orders, businesses can enhance productivity and ensure timely completion of tasks, essential for operational success.
Best Practices for Effective Work Order Management
Managing work orders efficiently is like oiling the gears of a well-functioning machine; it ensures everything keeps running smoothly. In today’s fast-paced operations, the need for attainable and effective work order management best practices cannot be overstated. Adopting these practices can significantly enhance productivity, communication, and the overall efficiency of processes within any organization. Here’s what you ought to know.
Standardization of Processes
Standardizing work order processes helps eliminate confusion and streamlines workflows. When everyone on the team understands the procedures, it minimizes the chances for errors and misunderstandings, like sending an installer with the wrong parts to a job site. Imagine if everyone used different sheets or formats for recording orders – information could easily slip through the cracks.
Standardization creates a uniform approach, which not only saves time but also enhances accountability. By having a clear, singular system in place, employees can follow set protocols, making it easier to train new staff. Moreover, consistent workflows allow for better tracking and reporting of performance metrics.
Regular Training for Staff
Investing in regular training is paramount for sustaining an efficient work order management system. Staff must be well-acquainted with the processes, tools, and software used in managing work orders. A seasoned worker fresh from training might still make errors simply because the processes or technology used change rapidly. Keeping staff updated ensures that they are competent and comfortable with any new systems introduced.
- Benefits include:
- Improved accuracy in work order completion.
- Reduction in time spent on troubleshooting and clarifying procedures.
- Enhanced employee morale, as team members feel valued when given a chance to learn and grow.
As an ongoing effort, business leaders should schedule periodic workshops and training sessions. Utilizing diverse learning materials can keep engagement high, ensuring no one is left behind.
Continuous Monitoring and Feedback
The phrase "you can't manage what you don't measure" rings especially true in the realm of work order management. Continuous monitoring allows managers to assess how well the system is functioning, identifying bottlenecks, redundancies, and areas for improvement. It’s akin to having a magnifying glass that brings to light every aspect of the operation.
Encouraging feedback from staff also plays a crucial role in this process. They are often the ones working most closely with the systems, and their insights can enlighten management on effective practices or issues that require addressing.
Some effective monitoring techniques include:
- Regular reviews of work order completion times.
- Staff surveys to gather opinions about the existing processes.
- Key performance indicators (KPIs) to evaluate efficiency and productivity.
Culmination
In wrapping up the exploration of shop work orders, it becomes evident how crucial they are for operational efficiency across various sectors. The effective management of work orders directly translates into improved workflow, ensuring tasks are completed in a timely manner. Systematic work order protocols facilitate clarity among team members, minimizing the chances of miscommunication or resource wastage.
Recap of Key Points
- Defining Shop Work Orders: Understanding what a work order is and its role in operations is the first step towards harnessing its potential. It serves as the blueprint for tasks at hand and lays the groundwork for successful outcomes.
- Key Components: Elements such as detailed project descriptions, material requirements, and time estimates are essential to avoid hiccups during execution. Having these well-documented helps maintain accountability and efficiency.
- Technology's Role: With the advent of various software solutions, managing work orders has become more streamlined. Integration with other operational systems enhances data flow, making tracking progress simpler.
- Best Practices: Applying standardization, providing regular training, and establishing continuous monitoring lead to an effective workflow that can adapt to changes quickly.
Future of Work Orders in the Industry
Looking ahead, the landscape of work orders continues to evolve. As industries increasingly embrace automation and AI, the future of work order management may involve predictive analytics, helping organizations anticipate resource needs before they arise. Furthermore, the integration of real-time data from Internet of Things (IoT) devices could redefine how decisions are made regarding resource allocation.
In an era where every second counts, organizations that harness the power of proactive work order management are likely to stay one step ahead of the competition. Developing flexibility and responsiveness in their operations will be key for businesses that want to thrive in an ever-changing market. The importance of shop work orders will remain a vital topic as companies seek to maximize efficiency and continuously improve operational frameworks.