Comprehensive Overview of Tool Inventory Systems
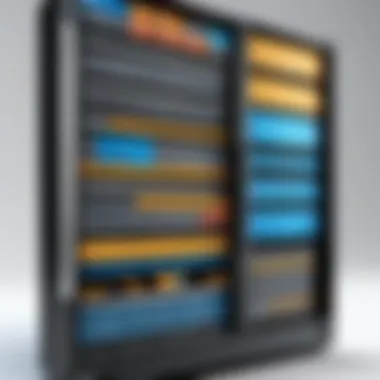
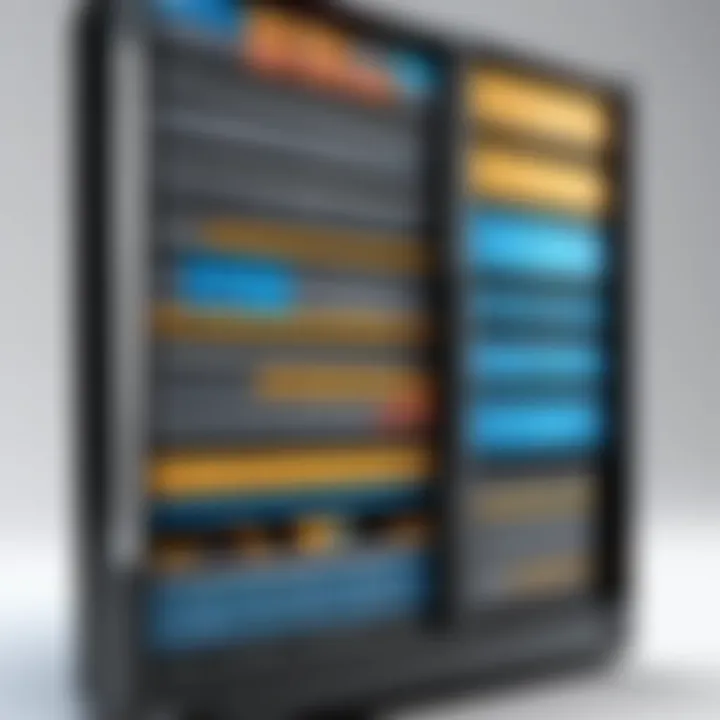
Intro
Tool inventory systems play a vital role in the efficient management of assets within any business or organization. As companies strive for operational excellence, these systems bring structure and clarity to the handling of tools and equipment. They allow for better tracking, usage optimization, and maintenance practices, which ultimately lead to reduced costs and enhanced productivity. In this article, we explore essential features, user experience, challenges faced during implementation, and emerging trends that shape the future of tool inventory systems.
Understanding the components and significance of these systems is crucial for decision-makers, IT professionals, and entrepreneurs aiming to optimize their asset management practices. The insights provided here aim to equip you with a comprehensive foundation for making informed decisions regarding tool inventory systems.
Overview of Core Features
An effective tool inventory system provides various functionalities tailored to accommodate diverse operational needs. Below are some essential features that such systems commonly include:
- Asset Tracking: The ability to monitor tools and materials, including their location, usage, and condition. This feature minimizes loss and improves accountability.
- Automated Alerts: Notifications for maintenance schedules, check-in/check-out reminders, or when stock levels reach predetermined thresholds.
- User Management: Access control features that offer varying levels of permission for different users, protecting sensitive data and allowing for user-specific tracking.
- Reporting Tools: Comprehensive reports that provide insights into usage patterns, maintenance history, and equipment life cycles. This data supports strategic decision-making.
The following table highlights how the features stack up across leading software options in the market:
| Feature | ToolWatch | GigaTrak | Asset Panda |
| Asset Tracking | Yes | Yes | Yes |
| Automated Alerts | Yes | No | Yes |
| User Management | Yes | Yes | No |
| Reporting Tools | Yes | Yes | Yes |
User Experience and Interface
User experience (UX) is a cornerstone of any tool inventory system's effectiveness. A well-designed UI enables users to navigate the platform with ease, ensuring all necessary features are within reach. Key aspects include:
- Intuitive Navigation: A clear layout helps users find information quickly without unnecessary confusion.
- Responsive Design: Compatibility across devices enhances accessibility, allowing users to operate the system from desktops, tablets, or smartphones.
- Customizable Dashboards: Users should be able to adjust their interface, focusing on metrics and reports that concern their specific roles. This flexibility improves efficiency.
The importance of usability cannot be understated. A system that is challenging to use can lead to resistance from staff, resulting in poor adoption rates and underutilization of valuable tools and data.
"A tool is only as effective as its user. Proper training on the system is essential for maximum benefit."
By focusing on user-centric design, organizations can ensure that their investment in a tool inventory system translates into tangible improvements in workflow and resource management.
Prelude to Tool Inventory Systems
In today's business landscape, efficient management of resources fundamentally influences operational success. Tool inventory systems exemplify this efficiency. They serve as a critical framework for tracking, managing, and optimizing the use of tools and equipment within a company.
Defining Tool Inventory Systems
Tool inventory systems refer to organized processes or software solutions designed to monitor and control the tools and equipment a business owns. These systems can be manual or automated, depending on the specific needs and scale of the operation. They keep detailed records of every item in the inventory, including its location, condition, and availability. The essence of tool inventory systems lies in their ability to provide real-time data, which helps organizations minimize losses and streamline operations. Through systematic categorization and tracking, companies can ensure that all tools are accounted for, which reduces the time wasted searching for misplaced equipment.
Importance in Modern Business
The relevance of tool inventory systems in modern business cannot be overstated. They bring several benefits that directly impact productivity and cost-effectiveness. A well-implemented system enhances operational efficiency by ensuring that the necessary tools are available when needed. This reduces downtime in various operations, allowing companies to meet deadlines and service commitments more effectively.
Moreover, these systems play a vital role in financial management. By closely monitoring the usage and condition of tools, businesses can avoid unnecessary purchases. This is crucial, especially for companies that rely on specialized equipment, where costs can quickly escalate if tools are lost or damaged.
"Effective inventory management is not just a task, it's an integral part of a successful business strategy."
Incorporating tool inventory systems also aids in compliance and safety regulations. For industries with stringent regulations, having precise records of tools used can significantly reduce liability while enhancing workforce safety. This multifaceted nature of tool inventory systems underlines their importance, making them a worthy investment for any business aiming for operational excellence.
Core Components of Tool Inventory Systems
The core components of tool inventory systems play a pivotal role in ensuring that businesses effectively manage their tools and assets. These elements not only optimize efficiency but also align with strategic goals of reducing operational costs and enhancing productivity. Understanding each component helps organizations tailor their systems to fit specific needs and challenges.
Database Management
Database management serves as the backbone of any robust tool inventory system. It involves the creation, storage, and retrieval of data concerning tools and equipment. An effective database can maintain detailed records encompassing vital information such as the type of tool, serial numbers, location, and maintenance schedules. This information facilitates quick access to data, which is essential during audits or when tracking tool usage.
Moreover, a well-structured database allows for easy updates and enhances data accuracy. This accuracy is fundamental in preventing discrepancies that could lead to potential losses. The use of advanced database software can also assist in establishing a centralized system that integrates with other software used in an organization.
Tracking and Monitoring
Tracking and monitoring tools are crucial for maintaining oversight of asset allocation and usage across an organization. This component provides real-time insights into the location and condition of each tool. Implementing tracking solutions, such as RFID tags or barcodes, simplifies the process of auditing and reduces the risk of tool loss or theft.
Businesses can leverage monitoring systems to analyze usage patterns, which in turn can inform purchasing and maintenance decisions. Regular monitoring not only helps optimize asset utilization but also promotes accountability among employees. Consistent tracking mechanisms empower managers to pinpoint when tools require repair or replacement, ultimately preserving capital.
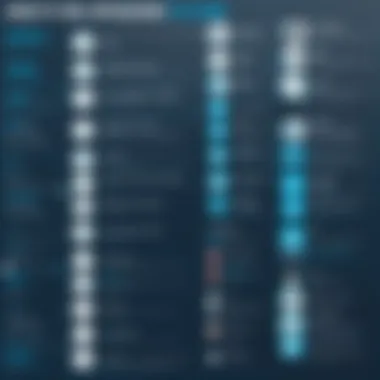
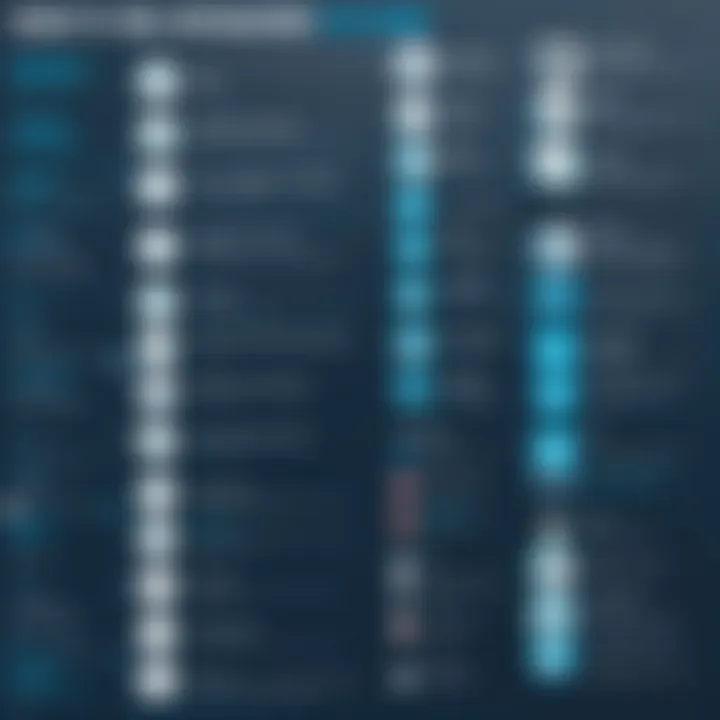
User Access Control
User access control is essential in ensuring the security of tools and sensitive data within the inventory system. This component sets permissions determining who can view, modify, or delete information. It is imperative for maintaining data integrity and protecting against unauthorized access.
Organizations need to establish clear user roles with varying levels of access. For instance, administrative staff may require full access for management purposes, while general employees might only need limited access to check out tools. Proper user access control not only enhances security but also fosters trust among employees by ensuring that access is aligned with responsibilities.
By focusing on these core components, companies can pave the way for a successful tool inventory management strategy. Each element builds on the others, creating a comprehensive system that streamlines operations and enhances overall efficiency.
"An effective tool inventory system is not just about tracking assets; it’s about creating a framework for precision and accountability within the organization."
Types of Tool Inventory Systems
Understanding the different types of tool inventory systems is crucial for organizations seeking to optimize their asset management. Each type serves unique business needs, and the choice impacts efficiency, cost, and overall management strategies. Decision-makers must weight the advantages and disadvantages of each format to align with specific operational goals. This section will analyze three primary types: Manual Inventory Systems, Automated Inventory Systems, and Cloud-Based Solutions.
Manual Inventory Systems
Manual inventory systems involve the traditional methods of tracking tools and equipment without reliance on technology. This can include spreadsheets, paper logs, and physical inventories. While many organizations still utilize manual systems for their simplicity, it is essential to recognize their limitations.
Key characteristics include:
- Cost-Effective: There are no upfront costs for software or licenses. Organizations may already use available tools, such as Microsoft Excel, for tracking.
- Simplicity: Many employees find manual systems straightforward and familiar. It does not require extensive training.
- Limited Features: Manual systems lack advanced features such as real-time updates and alerts for low stock levels. This increases the risk of errors.
- Time-Consuming: Conducting a physical inventory can take considerable time, and mistakes could arise from human error.
While manual inventory systems can work for small operations, they become cumbersome as the scale grows. Therefore, organizations with significant tool inventories should consider more advanced systems to minimize risks associated with errors or inefficiencies.
Automated Inventory Systems
Automated inventory systems utilize technology to manage tools and equipment efficiently. These systems can integrate barcode scanning, RFID technology, and sophisticated inventory management software. This approach streamlines data entry, tracking, and reporting.
Advantages of automated systems include:
- Accuracy: Automation reduces the potential for human error when tracking tools. Scanning a barcode, for example, increases precision in recording tool usage.
- Real-Time Tracking: Automated systems can provide live updates on inventory levels, enabling better decision-making regarding stock levels.
- User-friendly Interfaces: Many solutions offer intuitive dashboards and data visualization tools that make it easier for users to understand inventory status at a glance.
- Integration Capabilities: They often integrate seamlessly with other organizational systems, such as financial management software, which enhances interdepartmental communication.
The shift to automated systems often leads to increased productivity. However, investment in technology can be a barrier, especially for smaller businesses.
Cloud-Based Solutions
Cloud-based inventory systems represent the most advanced option. They hosted on remote servers allow access from any internet-connected device. This flexibility is a significant advantage, especially for organizations that have multiple locations or remote workers.
Notable features of cloud-based solutions include:
- Accessibility: Users can access tool inventory data anytime, anywhere. It supports mobile and remote operations.
- Scalability: Organizations can adjust their subscription or features as needed, making it suitable for companies that expect growth.
- Data Security: Many cloud-based systems provide advanced security features to protect sensitive inventory data.
- Automatic Updates: Software updates and enhancements occur without disrupting operations, ensuring the system remains current and efficient.
However, businesses should remain mindful of potential internet dependency and costs associated with subscription models.
In summary, choosing the right type of tool inventory system involves careful consideration of the company's needs, growth potential, and available resources. Evaluating these systems against budget constraints and operational requirements is crucial for making an informed decision.
Benefits of Implementing Tool Inventory Systems
Tool inventory systems serve crucial roles in modern businesses, contributing significantly to operational efficiency. When effectively implemented, these systems provide several key advantages that positively impact the overall success of an organization. Understanding these benefits helps decision-makers recognize the value of integrating such systems into their operations.
Cost Efficiency
One of the most tangible benefits is cost efficiency. Tool inventory systems allow organizations to accurately track tools and equipment usage. By keeping detailed records, businesses can analyze which tools are frequently used and which remain idle. This analysis helps reduce purchasing redundant tools or equipment.
In addition, these systems aid in the maintenance of tools, ensuring they are serviced on time. Regular maintenance can prevent costly breakdowns, thus saving money in the long run. For example, a construction company monitoring its tools might notice a trend in excessive wear on certain equipment, prompting preemptive maintenance which could avoid a more expensive and extensive repair.
Enhanced Productivity
Enhanced productivity is another compelling benefit. Tool inventory systems streamline workflows by minimizing the time employees spend searching for tools. When tools are organized and tracked within an inventory system, workers can quickly access needed equipment, leading to improved efficiency.
Moreover, automated systems often feature alerts and reminders. For instance, if a tool is due for maintenance, an automated notice can notify staff, preventing downtime from unexpected failures. Additionally, accurate inventory levels can prevent work stoppages due to unavailable tools.
Improved Asset Management
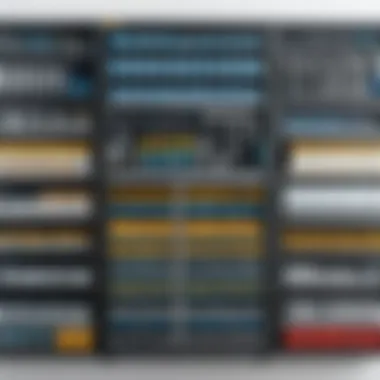
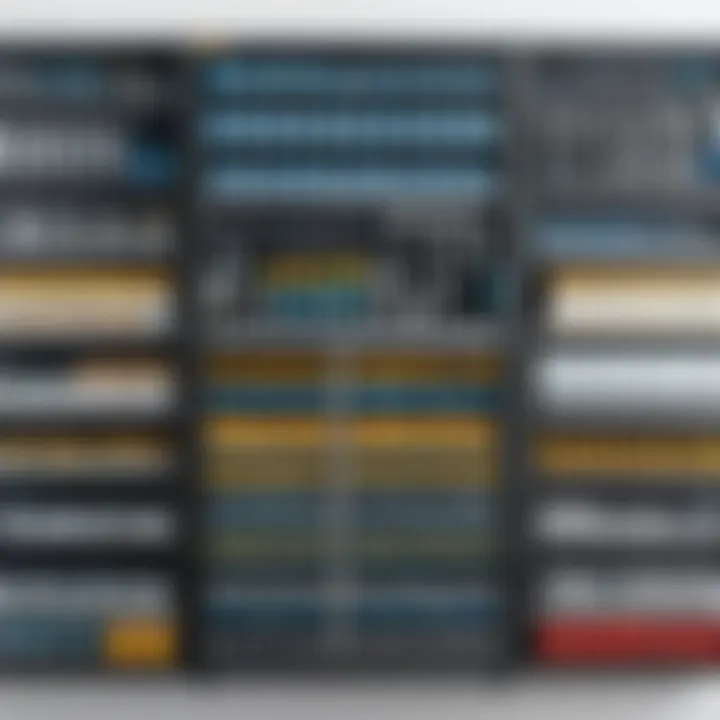
Improved asset management rounds out the main benefits of tool inventory systems. Organizations gain better visibility into their assets, which fosters more strategic decision-making. With accurate data, organizations can determine when to purchase new tools, retire old ones, or redeploy assets to where they are most needed.
This enhanced management also extends to tracking the location and condition of tools, which can reduce loss and theft. In sectors such as construction where equipment represents significant financial investment, monitoring tools can significantly safeguard against unexpected losses.
In summary, the implementation of tool inventory systems leads to numerous benefits, ranging from cost efficiency to improved asset management. Each of these factors plays a vital role in enhancing operational effectiveness. Organizations that invest in such systems often experience considerable advantages in their functionality and productivity.
Challenges Faced in Tool Inventory Management
Managing a tool inventory system comes with an array of challenges that can hinder efficiency and effectiveness. Recognizing and addressing these challenges is crucial for businesses aiming to improve asset management. As organizations adopt various tools and software for inventory management, they often discover several obstacles that could lead to mismanagement or deficiencies in their operations.
The following sections outline three primary challenges in tool inventory management: data accuracy issues, resistance to change, and integration difficulties with existing systems. By understanding these challenges, decision-makers can take proactive steps to minimize their impact.
Data Accuracy Issues
Data accuracy is paramount in a tool inventory system. When inventory records are inaccurate, organizations face significant risks. Errors in data can result in misplaced tools, inadequate stock levels, or budgeting issues. For example, underreporting tools can lead to unnecessary purchases, raising costs and straining financial resources. Likewise, over-reporting can create a false sense of security about asset availability, leading to project delays.
To mitigate these issues, it is essential to implement regular audits and use technology that enhances data integrity. Real-time tracking systems can significantly improve data accuracy by providing up-to-date information on the location and usage of tools. Moreover, training staff on the importance of accurate data entry can reinforce accountability.
Resistance to Change
Implementing a new tool inventory system often encounters resistance from personnel. Employees may feel comfortable with existing processes, even if they are inefficient. This resistance can stem from fear of the unknown, the perceived complexity of new systems, or the additional effort required for training.
To overcome this resistance, organizations must focus on communication and involvement. Engaging staff early in the process can foster a sense of ownership. Providing comprehensive training and showcasing the benefits of the new system will also help in building buy-in. A smooth transition is crucial. It ensures that employees feel supported rather than overwhelmed by new methodologies.
Integration Difficulties with Existing Systems
Integrating a new tool inventory system with existing platforms can present various complications. Many businesses employ a patchwork of systems that do not align seamlessly. This can lead to data silos, where information is trapped and inaccessible for essential decision-making processes.
To address integration issues, organizations should select tools designed with interoperability in mind. Selecting a comprehensive system that can communicate with other software will reduce complications. Furthermore, conducting a thorough assessment of current systems and processes beforehand can facilitate smoother integration, helping pave the way for a more cohesive inventory management strategy.
"Acknowledging the challenges in tool inventory management is the first step towards creating effective solutions that enhance operational efficiency."
In summary, recognizing and addressing the challenges associated with tool inventory management is essential for optimizing asset management. Improving data accuracy, overcoming resistance to change, and ensuring seamless integration will significantly contribute to the success of any tool inventory initiative.
Implementing a Tool Inventory System
Implementing a tool inventory system is crucial for organizations aiming to optimize their asset management. This topic covers various aspects that enhance operational efficiency. An effective implementation can lead to significant improvements in tracking, control, and resource allocation. Furthermore, the adherence to a structured process can mitigate common challenges businesses face during the implementation. Ensuring all stakeholders are aligned with the system’s objectives is essential.
Steps to Successful Implementation
Assessing Needs: The first step involves identifying the specific needs of your organization. Understanding the nature of the tools and the volume of transactions plays a significant role in determining the features required in a system.
Choosing a Project Team: Assemble a team from relevant departments. This includes IT professionals, inventory managers, and end-users. Their different perspectives will guide requirements and support throughout the implementation process.
Setting Goals: Define clear, measurable goals. Goals should reflect the overall intent of the tool inventory system, such as reducing discrepancies or decreasing downtime associated with missing tools.
Selecting the Appropriate Software: The choice of software directly impacts the success of the implementation. Evaluate different options based on features, scalability, and user-friendliness.
Training Employees: Ensure that employees receive adequate training on the new system. A well-informed staff is more likely to embrace the tool, reducing resistance to change. Consider ongoing training and resource availability.
Conducting a Pilot Test: Before a full roll-out, conducting a pilot test helps to identify potential issues in a controlled environment. Feedback from users is invaluable at this stage.
Full System Deployment: After successful testing, deploy the system organization-wide. Monitor its operation closely during the initial phase to address any immediate concerns.
Regular Maintenance and Updates: Establish a schedule for routine check-ups. Regular maintenance ensures the system operates efficiently and stays updated with the latest technology advancements.
Choosing the Right Software
Selecting the right inventory software is a pivotal decision in implementing a tool inventory system. There are several factors to consider:
Features and Functionality: Look for comprehensive features that meet the unique needs of your operations. This includes tracking capabilities, reporting functions, and user access controls.
Usability: The interface should be intuitive. A user-friendly design minimizes training time and helps in quicker adaptation.
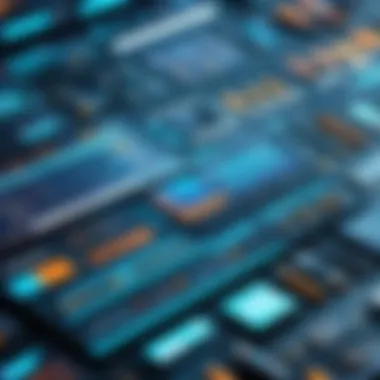
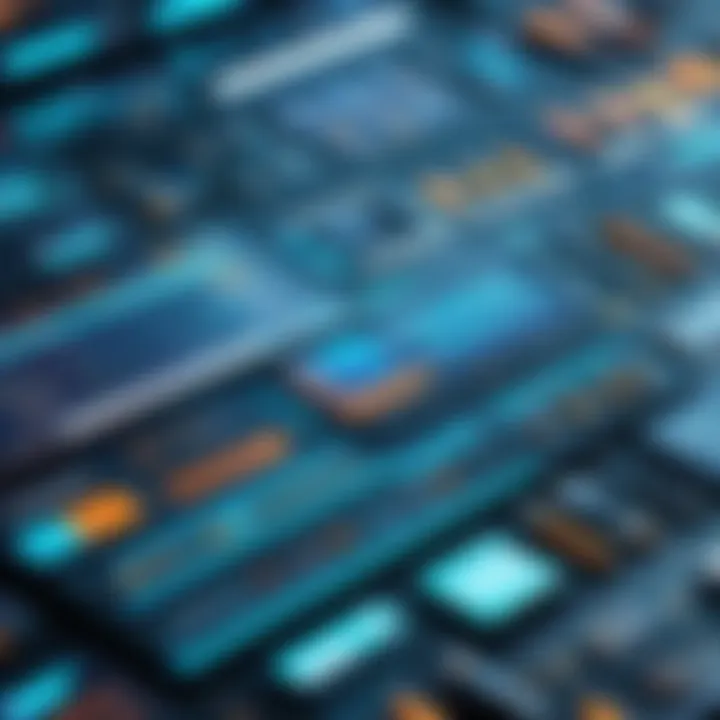
Integration Options: It’s essential to check if the software can smoothly integrate with existing systems. Compatibility reduces the likelihood of workflow disruptions.
Scalability: As your business grows, your tool inventory system should be able to accommodate increased inventory volume and complexity.
Vendor Support: Assess the level of customer support offered by the software vendor. Reliable support can make a significant difference during both implementation and ongoing use.
Cost-Benefit Analysis: Analyze the costs versus the potential benefits the software can provide. Avoid overspending on features that may not be essential for your organization.
Implementing a structured approach to selecting and deploying a tool inventory system maximizes the chances of success. With the right steps and software, organizations can see marked improvements in efficiency and productivity.
Future Trends in Tool Inventory Systems
As businesses evolve and technology advances, the landscape of tool inventory systems also changes. Understanding future trends in this domain is critical for decision-makers. It enables companies to remain competitive and efficient as they navigate the increasingly complex business world. Recognizing patterns in automation, data analytics, and user accessibility significantly influence operational success.
Artificial Intelligence Integration
The integration of Artificial Intelligence (AI) in tool inventory systems is no longer merely an idea for the future; it is actively reshaping how organizations manage their assets. AI enhances predictive analytics, which serves to foresee tool requirements and inventory levels. This capability helps prevent shortages and reduces excess inventory, which can lead to unnecessary spending.
Moreover, AI algorithms assess usage patterns and suggest optimal reorder points. They can analyze data from multiple sources, providing insights that are difficult to obtain through traditional methods. Consequently, organizations enjoy increased operational efficiency and a clearer understanding of their inventory needs. A more automated approach to inventory management led by AI allows employees to focus on more strategic tasks, fostering innovation and efficiency.
"AI provides businesses the opportunity to not just react, but to anticipate their inventory needs for greater efficiency."
Incorporating AI also aids in minimizing human error during data entry and inventory tracking. Enhanced accuracy in managing assets leads to better resource allocation. As a result, organizations will likely see lower overhead costs and improved productivity levels across teams.
Increased Mobile Accessibility
Another significant trend is the rise of mobile accessibility in tool inventory systems. As the workforce becomes more mobile, the need for solutions that allow inventory management from anywhere has increased. This shift is crucial for organizations that require field operations or have teams distributed across various locations.
Mobile applications enable staff to update inventory in real-time. This feature enhances communication and updates all users immediately about tool availability. The use of mobile devices helps in minimizing delays, ensuring that operations are not hindered by outdated inventory information.
Furthermore, increased mobile accessibility promotes accountability among users. When employees can easily input and track their inventory interactions, it fosters a sense of ownership. Training staff on mobile systems is often straightforward, making the transition to these technologies seamless.
Case Studies of Successful Tool Inventory Implementations
Tool inventory systems are becoming essential for companies in various sectors. Case studies showcasing successful implementations provide tangible insights into how these systems can be applied effectively. They illustrate real-world applications and outcomes, serving to highlight best practices and common pitfalls. Examining these examples can show not only the functional aspects but also the strategic advantages gained from utilizing an effective tool inventory system.
Industry-Specific Examples
In the manufacturing sector, a leading automotive company adopted an automated inventory system to manage their tools. Before the implementation, they faced significant delays and losses due to inefficiencies in tracking their assets. Post-implementation, the company reported a 30% reduction in downtime caused by tooling issues. This case emphasizes the importance of accurate tracking and monitoring that an automated system provides. It showcases how such systems enhance overall production efficiency.
Another example comes from the construction industry. A general contractor integrated a cloud-based tool inventory solution to manage equipment across multiple job sites. The results were noteworthy; the contractor documented a decrease in equipment loss by 50% within the first year. Having real-time access to inventory details made it easier for managers to allocate resources more effectively. This instance highlights how adaptability to specific industry needs is crucial in selecting the right tool inventory system.
Lessons Learned from Implementations
Several key lessons emerge from analyzing these case studies. First, the alignment of the tool inventory system with company objectives is imperative. Organizations need to ensure that the features of the system match their operational goals to optimize functionality.
Second, employee training plays a vital role in the success of implementation. Companies that prioritized comprehensive training sessions saw a smoother transition and higher utilization rates. Employees who understand how to leverage the system are more likely to contribute to its success.
Third, continuous evaluation of the system is necessary. Collecting feedback from users and analyzing performance metrics periodically helps organizations stay current with evolving needs and technologies. Organizations can improve their inventory practices by remaining flexible and responsive to challenges.
Closure
In the realm of business operations, the efficacy of tool inventory systems cannot be overstated. These systems play a vital role in enhancing overall asset management strategies. They ensure that tools and equipment are accounted for, thereby minimizing losses and increasing accountability. Businesses that implement these systems can better align their operational processes with industry standards, ultimately improving decision-making and resource allocation.
Recap of Key Points
Several key aspects underscore the significance of tool inventory systems:
- Cost Savings: By reducing equipment loss and streamlining procurement processes, organizations can see substantial financial benefits.
- Operational Efficiency: Enhanced tracking and monitoring capabilities ensure that tools are always available when needed, reducing downtime.
- Data Management: Robust data management allows for more informed decisions based on real-time information about available tools and their condition.
- User Management: Access control features help to limit exposure to risks by ensuring that only authorized personnel can access certain tools.
In summary, the significant benefits and applications of tool inventory systems mark them as indispensable for modern businesses.
Final Thoughts on Selecting and Managing Tool Inventory Systems
Choosing the right tool inventory system requires careful consideration. Organizations must evaluate their specific needs and the existing infrastructure. It is important to assess:
- Scalability: Will the system grow with your business?
- User-Friendliness: How easy is it for staff to adopt and utilize?
- Integration: Does it fit well with other systems already in place?
Additionally, ongoing management is crucial. Regular audits and updates ensure the accuracy of tool data. Businesses should also engage with users to gather feedback, fostering an environment of continuous improvement. Prioritizing these considerations will result in a system that not only meets but exceeds operational demands.