Understanding Shop Construction Costs: A Calculator Guide
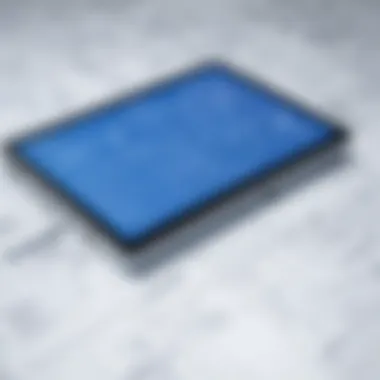
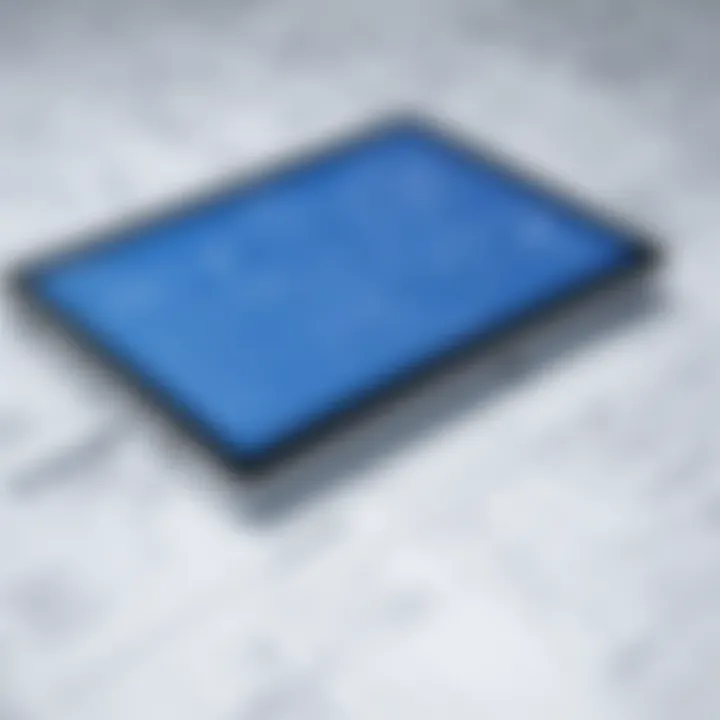
Intro
In the world of construction and entrepreneurship, planning is key. If you're venturing into building a shop, understanding the costs involved is crucial to turning your vision into a tangible reality. Using a cost to build a shop calculator can be a game-changer, transforming complex numbers and estimates into a clear roadmap. This guide not only explains how this tool functions but also highlights various factors that could affect your budget and planning.
Equipped with insights into budgeting strategies, this article provides a deeper understanding of the elements that come into play when constructing a shop. From assessing raw materials to manpower and everything in between, your ability to accurately estimate these costs can make or break your project. So, let's dig in and explore the core features of these calculators and what they can offer.
Overview of Core Features
To start, understanding the functionalities of a cost to build a shop calculator is pivotal. These calculators typically serve several key purposes:
- Cost Estimation: They provide a reliable estimate through simple input variables such as sizes, materials, and labor costs.
- Time Management: Helps in establishing timelines by integrating time estimates with cost predictions.
- Resource Allocation: Ensures optimal distribution of funds and materials throughout the building phase.
Description of essential functionalities
Cost to build a shop calculators are not one-size-fits-all tools; they encompass various features:
- Material Cost Breakdown: A detailed look at individual material expenses, allowing for more accurate budgeting.
- Labor Cost Calculation: Estimations that factor in local labor rates and project timelines tailored to your locality.
- Customization Options: Users can often input unique specifications to reflect their project more closely, from square footage to desired finishes.
- Reporting Tools: Generate detailed reports which can be invaluable during the planning phase and while seeking financing.
Comparison of features across top software options
Numerous software packages exist on the market, each boasting unique advantages:
- Buildertrend: Offers an all-in-one solution with project management, scheduling, and budgeting in one place.
- CoConstruct: Excellent for custom builders, focusing heavily on client interactions while providing detailed cost estimates.
- ProEst: This tool integrates seamlessly with other systems, providing robust analytics and cost benchmarking capabilities.
Ultimately, the right tool for one project might not be the best for another. Consider what specific features you value before making a decision.
User Experience and Interface
Having robust functionalities is just one side of the equation. If the calculators arenât user-friendly, youâre likely to run into some hiccups that could cause delays or inaccuracies.
Insights into UI/UX design aspects
A well-designed user interface ensures that even those new to construction budgeting can navigate the software without drowning in a sea of options. Many calculators provide:
- Intuitive Dashboards: First-rate calculators present all necessary info upfront, reducing the need for excessive clicks.
- Visual Data Representation: Charts and graphs help in understanding complex data, making comparisons easier.
Importance of usability and accessibility
In a field where time is of the essence, ease of access to calculations and real-time updates is critical. Mobile compatibility is becoming increasingly important, allowing users to make changes on the fly, whether on-site or virtually.
"Usability directly impacts productivity. If professionals can't use a tool effectively, it becomes a burden rather than a helper."
Understanding these elements enhances not merely the experience of using the calculator but significantly influences project success.
Through this guide, youâll be well on your way to mastering the art of planning, estimating, and ultimately executing your shop construction project with confidence.
Understanding the Cost to Build a Shop Calculator
When it comes to constructing a shop, understanding the cost elements can make or break a project. A cost to build a shop calculator serves as a vital tool for stakeholders, giving them a clearer picture of the expenses involved in setting up a shop. These calculators help demystify the often convoluted process of budgeting, guiding future owners in making informed financial decisions.
Definition and Functionality
A cost to build a shop calculator is essentially a digital tool designed to estimate the expenses associated with building a shop. The functionality of these calculators usually encompasses various parameters, such as size, location, materials, and labor costs. By inputting specific data points related to the intended project, users can generate quick estimates that offer a snapshot of potential financial commitments.
Here's how it generally works:
- Input Variables: Users can enter details like square footage, design features, and site specifications.
- Calculation Process: The calculator crunches these figures, often referencing regional averages for construction costs.
- Output Estimates: Finally, a breakdown of anticipated costs appears, covering major categories like materials, labor, and overhead expenses.
Good calculators also include options for customizing values based on local pricing trends, thus ensuring a degree of accuracy tailored to the user's specific area. This means, if you're looking to set up shop in Seattle, for instance, the calculator can reflect the unique economic landscape of the Pacific Northwest.
Importance in Financial Planning
In the realm of financial planning, having a reliable cost to build a shop calculator is not just helpful; it's indispensable. The tool plays a critical role in setting realistic budgets and identifying potential financial pitfalls before they emerge. This foresight helps minimize the chance of cost overruns that could derail a project.
- Guiding Investment Decisions: By providing estimates, the calculator assists business owners in evaluating whether their investment aligns with their financial capabilities. It helps prevent the scenario where someone jumps into building without a clear understanding of the monetary implications.
- Risk Mitigation: Accurate estimations can highlight hidden costs like permits, utility connections, and site preparation. Recognizing these factors from the get-go enables better risk management.
- Funding Requirements: It aids in formulating funding strategies. If the estimates are crystal clear, entrepreneurs can present concrete data to banks or investors, increasing their chances of securing necessary capital.
As a pivotal resource, a cost to build a shop calculator not only facilitates immediate insights but also lays down a solid foundation for more complex financial planning down the line.
"Planning without action is futile, action without planning is fatal."
- Unknown
Thus, grasping the functionality and significance of this calculator serves as a stepping stone in navigating the financial landscape of shop construction.
Key Features of a Cost to Build a Shop Calculator
Understanding the key features of a cost to build a shop calculator can save time, money, and headaches during the planning stages of any construction project. While these calculators are essential tools, their true power lies in the details they offer. The effectiveness of a calculator hinges on its ability to factor in various elements that impact the overall cost, creating a bespoke estimation that aligns with individual projects.
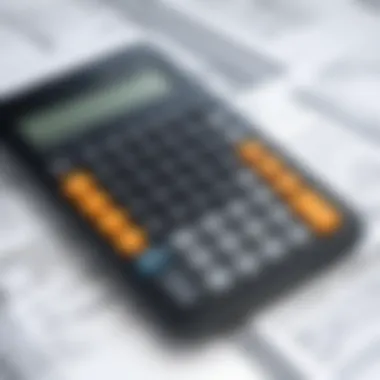
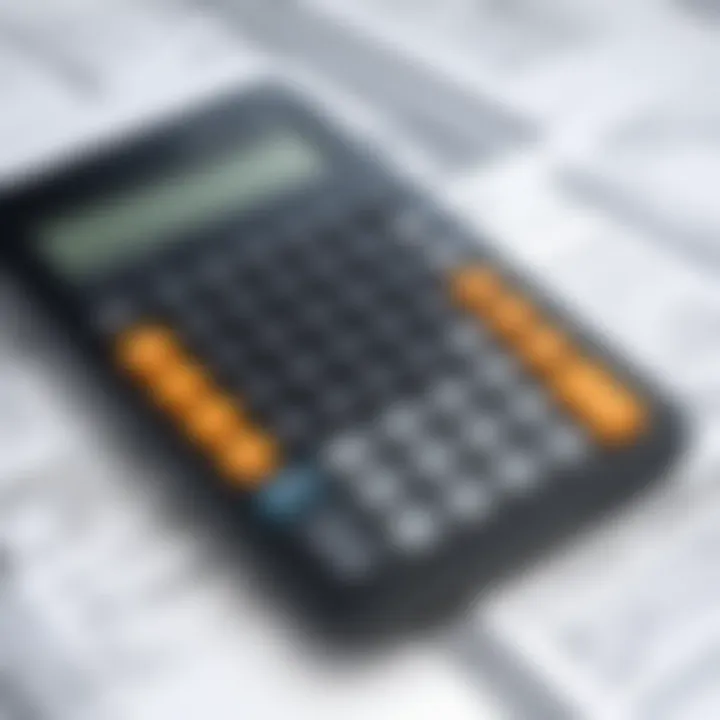
Cost Estimation Variables
When utilizing a calculator for cost estimation, itâs crucial to recognize the multitude of variables at play. These include:
- Material Costs: The prices of construction materials can fluctuate due to market demand and availability. A good calculator will integrate up-to-date prices.
- Labor Rates: Different tradespeople come with varying costs; electricians, plumbers, and carpenters have unique rates based on their expertise and locality.
- Design Specifications: The complexity of design can dramatically affect costs. More intricate designs require more skilled labor and higher-quality materials.
- Size and Dimensions: Square footage and layout will naturally dictate material needs and labor hours.
A comprehensive calculator should assess these variables, allowing users to tweak inputs and see immediate adjustments to the estimated costs.
User-Friendly Interfaces
Navigating cost calculators should not feel like rocket science. A user-friendly interface is paramount. When a calculator simplifies the input process, it enhances the experience significantly. Popular features include:
- Intuitive Layout: Clear sections for inputting data minimize errors and confusion.
- Visual Indicators: Graphs or charts showing cost breakdown may help users understand where their money goes.
- Real-Time Updates: Instant feedback after each input helps users grasp their project's shifting financial landscape.
Seeing how costs change in response to adjustments provides immediate insight and empowers decision-making with confidence. If the interface feels cumbersome, the usefulness of the calculator can be lost in translation.
Integration with Local Regulations
Building construction is heavily influenced by regulations that vary by region. A cost to build a shop calculator that offers integration with local requirements can significantly improve accuracy. Key points to consider are:
- Permit Costs: Local jurisdictions often impose fees for necessary permits. A well-designed calculator will include these in the estimate seamlessly.
- Zoning Laws: Understanding restrictions or requirements tied to land use could save project owners from costly setbacks or fines.
- Environmental Regulations: Local environmental building codes might influence material choices and construction practices, impacting overall costs directly.
By incorporating these local regulations into estimates, calculators reassure users that their budgets are realistic and compliant.
The right cost to build a shop calculator can be the difference between a well-planned project and a chaotic budget nightmare. By honing in on estimation variables, ensuring user-friendly designs, and adapting to local rules, users can navigate their shop projects with clarity and confidence.
Components Affecting Shop Construction Costs
Understanding the various components that influence shop construction costs is essential for anyone considering a building project. Each element, from location to material choices, can create significant differences in the overall budget. Grasping these factors allows decision-makers to navigate the financial landscape more efficiently and reduces the chance of unexpected expenses. Letâs dive into each component that plays a vital role in shaping costs and outcome of a construction project.
Location Considerations
The first point of consideration in estimating shop construction costs is location. Not all places are createdequal; they come with unique advantages and challenges. Urban areas might offer more foot traffic but also have higher costs in terms of real estate and permits. Conversely, rural locations can provide lower land costs but might lack the customer base to sustain a business.
- Zoning Regulations: Make sure to check local zoning laws. A shop can be hindered by restrictions.
- Land Availability: Is the desired land ready for a build? You may encounter issues with land clearance or existing structures.
- Utilities Access: The proximity to essential services like water, electricity, and sewage has a direct impact on setup costs.
Each of these factors can alter the cash outlay significantly. Knowing what to expect in terms of location can help you set your budget wisely.
Material Selection
Material choice is another major player in the cost equation. Selecting high-quality materials may lead to a higher initial investment, but it can enhance durability and reduce long-term maintenance costs. On the other hand, going low-budget might save you dollars on day one, but it could also mean high repair bills down the line. Here are several points to think about:
- Durability and Lifespan: Choose materials that ensure longevity to avoid frequent replacements.
- Local Sourcing: If you can source materials locally, you may save on transportation and import fees, leading to a more cost-effective project.
- Environmental Impact: Eco-friendly materials could carry a higher price tag, but they often lead to savings on energy bills in the long run.
Choosing wisely here can save your bottom line while enhancing the aesthetic and functional qualities of your shop.
Labor Expenses
Labor costs can often make or break a budget. Understanding labor dynamics in your region is important for accurate estimates. Skilled labor naturally commands a premium, but cutting corners can lead to inferior workmanship, which might cost you more in the long run. Keep these considerations in mind:
- Labor Market: Evaluate the demand for skilled trade workers in your area. High demand may push wages upward.
- Total Work Hours: Breakdown project phases to calculate labor hours accurately. Think of unexpected delays; labor can add up quickly.
- Union vs. Non-Union Wages: Some regions have a unionized workforce that can come with higher costs but might ensure better quality standards.
Getting a grip on labor costs early on allows you to plan better and reduce the chance of financial surprises during construction.
Design Complexity
Finally, design complexity plays a crucial role in determining construction costs. A simple, straightforward design generally equates to lower costs. However, a more intricate layout can introduce variables that will increase both time and expense. Consider this:
- Architectural Features: Unique details usually cost more. Make sure theyâre necessary for your business model before committing.
- Functionality Needs: Does the design meet all functional requirements? If not, adjustments may lead to higher costs down the line.
- Future Flexibility: Consider modular designs that allow for easy future expansions or adjustments.
In essence, balancing design desires with cost realities helps ensure that your shop not only looks good but is also financially sustainable.
Remember: Every decision you make affects the overall budget. Prioritize information and research to make informed choices.
In summary, understanding these components affects decision-making and prepares you for the realities of shop construction costs. With careful planning and consideration of the factors discussed, budgeting for your construction project becomes a more manageable task.
Analyzing Cost Estimates
Analyzing cost estimates plays a crucial role in effectively managing shop construction projects, ensuring that every financial angle is scrutinized before the first brick is laid. This process is not just about crunching numbers; itâs about strategic foresight. Thorough analysis can help in mitigation of risks, ensuring that unforeseen costs don't derail your budget. By engaging in this analysis, decision-makers can have a clearer picture of expense allocations and future projections, ultimately leading to a more favorable financial outcome.
Initial Budgeting Strategies
Before embarking on any construction project, establishing a solid initial budget is necessary. This begins with understanding the core costs involved. Think of it like preparing a road map for a long journey; without it, you might find yourself lost down the wrong path.
- Gather All Potential Costs: Start with a comprehensive list that covers initial expenses like permits, materials, and labor. Consulting local contractors or use tools, including the cost to build a shop calculator, can yield important baseline figures.
- Prioritize Your Needs: Differentiate between 'must-haves' and 'nice-to-haves'. It helps in making tough decisions if funds become tight. For instance, if your budget is limited, investing more in high-quality foundational materials might take precedence over aesthetic upgrades.
- Contingency Funds: Allocate around 10-20% of your budget as a cushion for unexpected costs. Itâs like an insurance policy against unforeseen expenditures.
- Consult Professionals: Itâs always wise to engage experts early on. They can provide insights that might not be immediately obvious to someone without construction experience.
Adjusting Estimates Over Time
As the project progresses, circumstances can change. Market conditions, availability of materials, or an increase in labor costs can all necessitate a reevaluation of your financial estimates. Adjusting your initial figures regularly can help you stay on track and avoid nasty surprises.
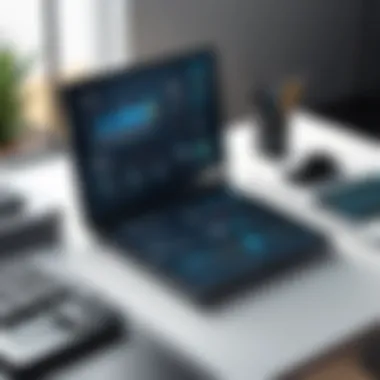
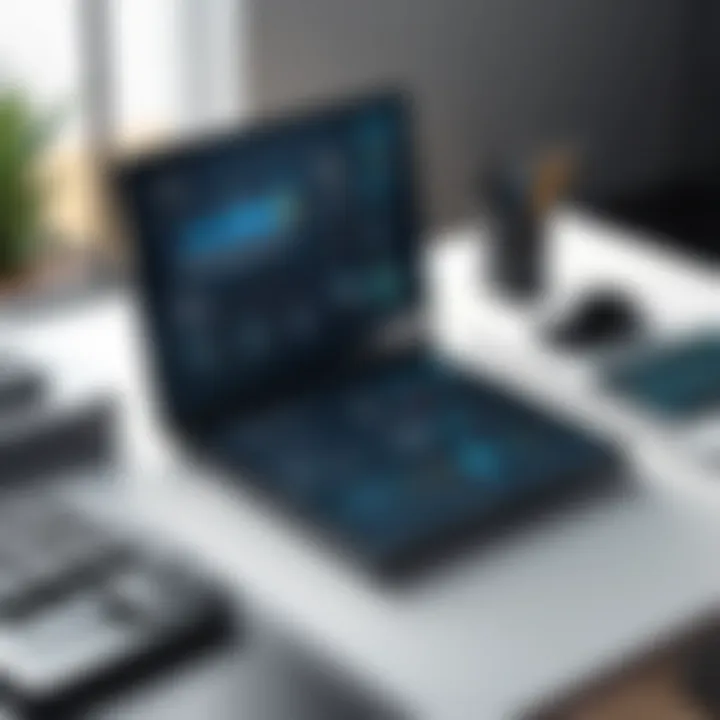
- Regular Review Frequency: Set specific times to reassess your budgetâmonthly, bi-monthly, or even weekly, depending on the scale of the project. Each review should consider any changes in quotation or labor costs.
- Communicate with Stakeholders: All team members, owners, and stakeholders should be in the loop regarding any budget adjustments. This way, everyone has a shared understanding of the current financial state and can provide input on necessary changes.
- Trend Observations: Keep an eye on trends in material prices and labor markets. Utilizing historical data can aid in predicting future price changes. For example, a sudden rise in lumber prices could warrant adjusting your budget if that material is significant for your project.
Comparing Estimates with Real Costs
Finally, once construction is underway, contrasting your original budget estimates with actual costs becomes critical. This ongoing analysis allows decision-makers to understand their financial performance and improve future budgeting processes.
- Establish a Tracking System: Use spreadsheets or specialized budgeting software to log all expenditures against your estimates. It should be structured in such a way that you can easily see where variances occur.
- Analyze Discrepancies: If certain costs are significantly higher or lower than anticipated, delve into the reasons why. Recognizing these patterns can guide future projects. For example, if labor consistently overages, you may need to adjust your initial hourly estimates in future planning.
- Learn from the Process: After the completion of the project, take time to conduct a thorough review of the entire budgeting and cost estimation process. Identify what strategies worked and what could be tweaked for better outcomes next time. Document these findings for reference.
Important Note: Continuous monitoring allows businesses to remain flexible. The ability to pivot and adapt is crucial in todayâs unpredictable markets.
By meticulously analyzing cost estimates, you empower yourself and your team to make informed decisions, ensuring that your shop construction project not only comes in on budget but establishes a strong foundation for future endeavors.
Leveraging Technology in Cost Calculations
In an era where digital solutions shape practically every industry, the construction of shops is no exception. Leveraging technology in cost calculations introduces a level of precision that was previously difficult to attain. With the rise of specialized software tools and cloud-based solutions, accurate financial predictions have become less of a guessing game and more of a reliable strategy.
Using technology not only enhances the estimation process but also helps in streamlining project planning and budgeting. Many professionals, from operators to architects, now depend on digital tools to pull data and generate wrap-around assessments designed specifically for their unique situations. This shift has paved the way for more informed decision-making in a landscape laden with variables.
Software Solutions Available
When it comes to calculating the costs involved in building a shop, thereâs a plethora of software options to consider. For instance, programs like RSMeans Data Online provide an extensive database of construction costs that are current and region-specific. Using such software can offer insights into local material prices and labor wages, which can make or break a budget.
While some developers might lean towards comprehensive all-in-one platforms, others may prefer modular solutions that can integrate into existing workflows. This flexibility allows decision-makers to select tools that align closely with their operational needs. Further, with advancements in technology, there's also an increasing focus on mobile applications which allow for on-the-go access to these essential calculations.
Highlights of notable software solutions include:
- CoConstruct: Tailored for home builders and remodelers, it simplifies project management and budgeting.
- PlanSwift: A digital takeoff and estimating software that enhances productivity and accuracy in cost estimation.
- Sage Estimating: Known for its flexibility, it aids in creating detailed project insights while managing historical data.
"Choosing the right software can drastically reduce the risk of cost overruns during the construction process."
The Role of Cloud Computing
Cloud computing has also made its mark in the realm of cost calculations. It facilitates the centralization of data, allowing team members from different locations to access and modify cost estimates in real-time. This collaborative approach encourages transparency and provides an accurate view of a project's financial standing at any time.
Adopting cloud technology means your information is stored securely and can be easily retrieved. In contexts where market conditions fluctuateâlike changes in material pricing or labor ratesâhaving quick access to project analytics becomes invaluable. Moreover, cloud solutions often come with built-in automation features that help in generating reports and tracking fluctuations in estimates without extra manual input.
Benefits of cloud computing in cost calculations include:
- Real-time accessibility and updates.
- Enhanced collaboration among team members across various projects.
- Improved data security and backup.
- Cost-effective solutions with reduced need for extensive IT infrastructure.
With advancements occurring at lightning speed in the digital landscape, harnessing technology effectively is integral for those involved in shop construction projects. From estimating costs accurately to sharing vital information with stakeholders, the blend of software solutions and cloud computing is proving to be an indispensable asset.
Case Studies of Shop Construction Costs
When it comes to understanding the financial landscape of building a shop, real-world examples carry a weight of knowledge that pure data often cannot convey. Case studies provide a lens through which one can evaluate various decision-making processes, outcomes, and strategies employed by different businesses. By examining specific instances in the shop construction realm, we gain valuable insights into budgeting methods, material procurement, labor costs, and the unforeseen pitfalls that might be lurking around the corner.
Small Business Case Study
Consider a local bakery that sought to open its first brick-and-mortar location. With a vision fueled by passion, the owners kicked off planning by utilizing a cost-to-build calculator, which first helped them estimate their start-up expenses. They quickly learned that construction costs in their chosen area could vary based on location and local demand.
In the initial stages, the bakery projected $120,000 in total costs. This estimate encompassed:
- Architectural Fees: $10,000
- Construction Costs (Labor and Materials): $75,000
- Equipment Costs: $25,000
- Permitting and Licenses: $10,000
However, as they navigated the construction process, they confronted unexpected challenges. Issues arose regarding zoning regulations which led to additional expenses, forcing them to adjust their overall budget. They eventually realized the necessity of establishing a 10% contingency fund to accommodate such unforeseen expenses.
This small business example underscores the vital importance of recognizing that flexibility in budgeting can be a game changer. Taking lessons from this case study, other small business owners might consider allocating a percentage of their estimated budget toward potential overruns. Itâs crucial to remember that hidden costs often sneak up when one least expects them.
"Failing to plan is planning to fail."
Retail Chain Analysis
Shifting gears to a larger scale, letâs examine a renowned retail chain that undertook the construction of a new outlet in a bustling urban area. This company, well-versed in the nuances of shop development, initiated their cost calculations with meticulous accuracy by studying past projects through a well-designed cost-to-build calculator.
Initial project estimates surged to around $2 million for the new establishment, broken down into:
- Site Preparation and Engineering Work: $500,000
- Construction of Building: $1.2 million
- Interior Setup and Fixtures: $200,000
- Marketing and Launch Costs: $100,000
Despite their extensive experience, the retail chain faced hiccups too. They discovered that local labor rates were significantly higher than anticipated, meaning labor expenses consumed a larger chunk of their budget than planned. Additionally, as they dove deeper into construction, supply chain disruptions posed challenges in obtaining specific materials necessary for their unique store design.
In response to these challenges, they leveraged data analytics to include alternative suppliers and used just-in-time inventory methods to minimize costs related to inventory storage. This case highlights how large-scale operations can adapt and thrive, even when unexpected challenges arise.
Through these case studies, whether from small enterprises or well-established chains, one learns that the journey of calculating construction costs is as valuable as the end result itself. Solid budgeting efforts augmented by strong adaptability are key takeaways for anyone aiming to build a shop.
Common Mistakes in Cost Calculation
When diving into the complexities of shop construction, itâs all too easy to trip over the subtle miscalculations that can have significant consequences for your project. Recognizing common mistakes in cost calculation is vital. Setting realistic budgets is indispensable not just for the project itself but also for maintaining financial health.
A misstep in budgeting can derail entire projects, leading to undue stress and, ultimately, wasted resources. As the old saying goes, "A penny saved is a penny earned." This couldn't ring truer when it comes to shop building. By understanding these pitfalls, youâre better equipped to navigate the financial landscape, ensuring that your project's estimates reflect reality.
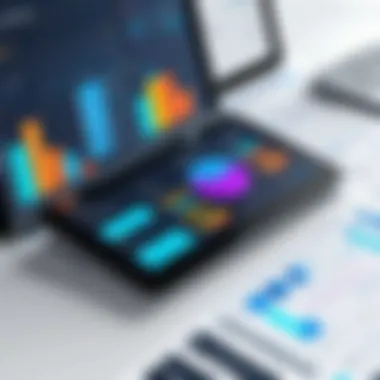
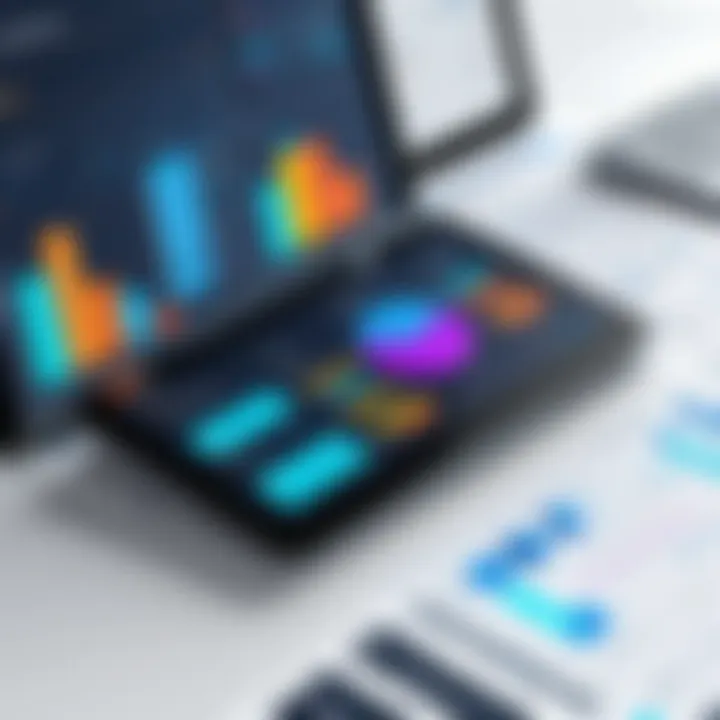
Underestimating Hidden Costs
One of the primary errors people make during the budgeting phase is overlooking hidden costs. Itâs like buying a car and only considering the sticker price. The initial outlay for building materials, labor, and equipment is just the tip of the iceberg.
Hidden costs can range wildly, affecting the overall project scope and financial planning. Some common categories of hidden costs include:
- Site preparation expenses: You might think youâve got a solid piece of land, but there may be unforeseen issues such as grading or soil issues that could add to your costs.
- Utility connections: Connecting water, electricity, and sewer lines can come with fees and complications that you never accounted for.
- Contingency fund: Itâs wise to set aside a small percentage of your overall budget for unexpected surprises.
Not addressing these hidden costs upfront can create cash flow issues later on, impacting your ability to complete the project on time and within budget. A well-rounded cost calculator will prompt users to factor in these intricacies, ensuring a more accurate portrayal of expected costs.
Ignoring Regulatory Fees
Another frequently overlooked aspect are the regulatory fees associated with building. Itâs easy to focus on construction costs and forget about the red tape waiting in the wings. Not all states or municipalities have the same requirements, and these fees vary widely.
This includes:
- Building permits: Almost every construction project will require some form of permit. Ignoring this could lead to fines or even halting construction completely.
- Impact fees: Depending on where you construct, there may be additional impact fees designed to offset the cost of new developments on infrastructure.
- Zoning compliance costs: Understanding the zoning regulations applicable to your site can save you headaches down the line.
For decision-makers and entrepreneurs, being caught off guard by sudden, unanticipated expenses can take the wind out of your sails. Ensuring your cost to build a shop calculator incorporates these regulatory fees provides you with a thorough financial overview and helps reinforce the foundation of your budgeting strategy.
> "If you fail to plan, you're planning to fail."
Future Trends in Shop Construction Costs
The landscape of shop construction is evolving, driven by both technological advancements and rising environmental consciousness. Keeping a finger on the pulse of these changes not only helps in making informed decisions but also offers a competitive edge in a saturated marketplace. Awareness of future trends in shop construction costs can fundamentally influence budgeting strategies, enabling stakeholders to allocate resources more efficiently and anticipate future expenses.
Sustainable Building Practices
With the growing concern about environmental sustainability, shop construction is witnessing a surge in sustainable building practices. Such practices not only minimize the carbon footprint but also offer significant long-term savings. For instance, by utilizing eco-friendly materials like recycled steel or bamboo, contractors can reduce overall costs while adhering to stricter environmental regulations.
Additionally, implementing energy-efficient designs can have a substantial impact on operational expenses. Features such as solar panels, energy-efficient HVAC systems, and high-performance insulation can reduce utility costs considerably over time. As more states and municipalities adopt incentives for green building, stakeholders can leverage these opportunities to lower initial costs, making sustainability both an economical and ethical choice.
Investing in sustainable practices today paves the way for cost savings tomorrow. The cycle of initial investment leading to reduced long-term expenses is not only prudent but necessary in todayâs economy.
Impact of Economic Changes
Economic fluctuations significantly shape construction costs, as they influence material prices, labor rates, and peripheral expenses. For decision-makers, recognizing these economic trends is crucial. For example, a surge in demand for construction can lead to a spike in material costs, such as lumber or concrete, which could inflate overall project budgets substantially.
Moreover, shifts in interest rates can affect financing options, which in turn impacts shop construction planning. Higher interest rates can lead to increased borrowing costs, compelling builders to rethink their financial strategies. On the flip side, when the economy is on an upswing, investments in shop construction typically see greater returns, necessitating a balance between timing and cost estimation.
Notably, global events can also surface unforeseen consequences on supply chains. Builders must learn to navigate these waters more cautiously, ensuring that contingency funds are in place to account for any sudden shifts in costs. Understanding the economic climate is no longer optional; it is a prerequisite for effective planning.
Resources for Further Research
When embarking on a shop construction project, having access to reputable materials for further research can be invaluable. Resources can serve as the backbone of a strong financial strategy. They distill complex cost concepts into digestible formats, enabling decision-makers to grasp the nuances without spinning their wheels. Whether you're a seasoned entrepreneur or a new business owner, diving into these resources can enhance your decision-making capabilities as well as illuminate the broader landscape around construction costs.
By engaging with this information, you not only elevate your knowledge but also preempt potential pitfalls that often lead to budgetary woes later on. From literature that covers theoretical underpinnings to practical tools designed for instant calculations, these resources play a critical role in optimizing your shop projectâs profitability and efficiency.
Books and Publications
Getting your hands on the right books and publications can be a game changer. They often provide comprehensive insights into the cost of building a shop, covering topics such as materials, labor, and design efficiencies.
- "Construction Costs Reference Book" by Alan Simmons: This book gives a broad overview, offering thorough insights into various regional costs and how they fluctuate. You can expect reliable benchmarks for estimating your shop's construction expenses.
- âThe Lean Startupâ by Eric Ries: While not specifically about shop construction, it offers valuable principles that can be applied to effectively budget and resource-manage during the build phase.
- Industry Journals: Publications like the âJournal of Construction Engineering and Managementâ often feature articles on recent trends and financial analytics that can lead to smarter, data-driven decisions.
These resources collectively equip you with critical context and strategies.
Online Tools and Calculators
Why not embrace technology in your quest to build a shop wisely? Various online calculators and tools can simplify your calculations and save you oodles of time.
- Square Footage Calculator: Tools that help you estimate the cost per square foot can be invaluable. Websites like Reddit host communities discussing these useful apps, offering personalized recommendations.
- Construction Cost Estimator by HomeAdvisor: This user-friendly tool provides estimates based on specific variables you input, thus tailoring your queries to your unique situation.
- Local Building Codes Resources: Certain state or municipal websites provide calculators that incorporate local codes and regulations into their estimates. This consideration not only ensures compliance but can also unearth additional costs you might not have considered initially.
Utilization of these digital tools allows you to focus more on strategy and less on guesswork as you prepare for your shopâs construction phase.
Integrating insightful books and cutting-edge online tools is essential for a thorough grasp of construction costs, especially in a climate where every dollar counts.
By tapping into these resources, you solidify your foundation, ensuring that the pressures of planning a shop construction are met with informed choices and judicious resource management. As the adage goes, knowledge is power, and in this case, itâs a powerful ally your project will greatly benefit from.
End
In the realm of shop construction, a well-rounded assessment culminates in the vital segment of conclusion. This part not only sums up the key insights derived from each preceding section but also cements the value of the cost to build a shop calculator in practical applications.
Summarizing Key Insights
To distill the discussion, it is clear that utilizing a cost to build a shop calculator enhances decision-making. From analyzing initial budgets to tracking ongoing expenses, these calculators offer a backbone to financial planning. Significant variables such as location, materials, labor, and design complexity play crucial roles in shaping the final cost estimates. Thus, leveraging the right tools can uncover hidden expenses and avert pitfalls associated with underestimating costs.
Moreover, integrating technology such as software solutions and online calculators further streamlines this process, making it easier for entrepreneurs and industry professionals to navigate the complexities of shop construction costs. This not only provides clarity but also empowers users to make informed decisions based on accurate, real-time data.
Recommendations for Future Projects
As you embark on your shop construction endeavors, consider the following recommendations to enhance effectiveness:
- Do Your Homework: Before diving into any construction project, research thoroughly. Understanding local regulations and market conditions is paramount.
- Utilize Advanced Tools: Engage with online calculators and software that sync with local pricing trends. This will facilitate more accurate estimations.
- Plan for Contingencies: Always account for unexpected changes in material costs or labor availability. A buffer of about 10-15% in your budget could save you from unpleasant surprises.
- Seek Professional Advice: Consult with experienced builders or financial advisors. Their seasoned insight could highlight areas you might overlook.
Ultimately, honing in on precise calculations not only steers your financial direction but also sets the stage for a successful shop project. Armed with comprehensive insights and clear recommendations, you're well-poised to tackle your construction goals head-on.